- HOME
- Technische Informationen
- TORAYCON™ PBT Resin
- Mechanical properties
Mechanical properties
Mechanical properties
The crystallinity of TORAYCON™ PBT Polymer falls within the range of 35% to 45% when molded using standard conditions. The mechanical properties of TORAYCON™ are less dependent on molding conditions than other crystalline resins. Also, its water uptake is extremely low, so the effects of water absorption on its mechanical properties are negligible.
Ⅰ. Tensile properties
The breaking elongation of TORAYCON™ 1401X06 is 300% at room temperature—a very large value that explains the resin's resilient characteristics.
While TORAYCON™ also has superb heat-resistance properties, its tensile properties are affected by environmental temperatures, as is the case with other thermoplastic resins. Abbildung 1 shows the temperature dependence of tensile strength in 1401X06 and 1101G-30. Abbildung 2 shows the strain-rate dependence of tensile strength in 1401X06. The glass-fiber reinforced grade (1101G-30) exhibits favorable mechanical properties, but limited breaking elongation of only 3-5%.
Abbildung 1: Temperature dependence of tensile strength
Abbildung 2: 1401X06 strain rate
Ⅱ. Flexural properties
The flexural properties of TORAYCON™ PBT Polymer are influenced by environmental temperatures, as is the case with other thermoplastic resins.
Abbildung 3 shows the temperature dependence of flexural strength in TORAYCON™. Abbildung 4 shows the temperature dependence of flexural modulus.
Abbildung 3: Temperature dependence of flexural strength
Abbildung 4: Temperature dependence of flexural modulus
Even at high temperatures, the 1101G-30 grade exhibits superb mechanical properties—at 130°C, its flexural strength is 95 MPa and its flexural modulus is 3.5 GPa.
Ⅲ. Impact strength
TORAYCON™ PBT Polymer is resilient to impact, too. Table 2 shows the impact strength of each grade.
Although the resin's Izod impact strength (using a notched sample) cannot be categorized as high compared to other engineering resins, TORAYCON™ is extremely strong against falling-dart impact, a better measure of impact strength in practical applications. For example, the falling-dart impact strength of TORAYCON™ is 40 times that of polyacetal.
Category | Unit | Non-reinforced | Glass-fiber reinforced | |
---|---|---|---|---|
1401X06 | Polyacetal | 1101G-30 | ||
Tensile impact strength a) | kJ/m2 | 310 | 260 | - |
Falling-dart impact strength b) | N·m | 17 | 0.4 | 0.4 |
Izod impact strength | ||||
Unnotched sample c) | kJ/m2 | NB | - | 6.5 |
Notched sample d) | J/m | 50 | 60 | 80 |
a) ASTM D1822 S Type dumbbell 1/8" thickness
b) 40mmφ, 22mm t disc, falling dart tip 5 mm R
c) 1/8" thickness
d) 1/2" thickness
Abbildung 5 shows the temperature dependence of impact strength. TORAYCON™ retains excellent impact strength even at low temperatures.
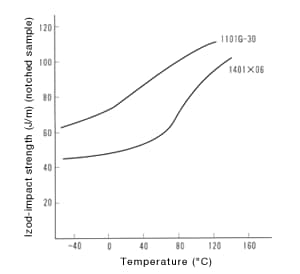
Abbildung 5: Temperature dependence of impact strength
Ⅳ. Creep-resistance properties
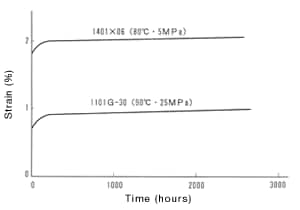
Abbildung 6: Tensile-creep curve
Exposure to stress for extended durations of time can lead to creep rupture or creep deformation problems.
Abbildung 6 shows the tensile creep properties of TORAYCON™ PBT Polymer.
TORAYCON™ exhibits superior resistance to creep. The glass-fiber reinforced grade (1011G-30) is suited for particularly high-temperature, high-stress applications.
Ⅴ. Fatigue resistance
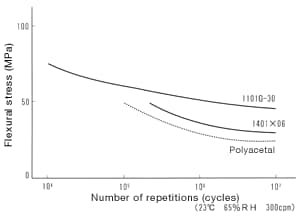
Abbildung 7: Fatigue curve
TORAYCON™ PBT Polymer boasts excellent resistance to fatigue. Abbildung 7 shows its fatigue-resistance properties using a cantilever flexural fatigue test.
The non-reinforced grade (1401X06) exhibits superior resistance to fatigue than polyacetal, which had been considered the most fatigue-resistant among thermoplastic resins.
Fatigue resistance after 107 cycles is 30 MPa in 1401X06 and 45 MPa in 1101G-30.
Ⅵ. Resistance to friction and wear
TORAYCON™ PBT Polymer withstands friction and wear superbly. See Table 3 for a comparison to polyacetal resin.
Category | Unit | Non-reinforced | Glass-fiber reinforced | ||
---|---|---|---|---|---|
1401X06 | Polyacetal | 1101G-30 | |||
Taper abrasion loss a) | mg/1000 cycles |
10 | 14 | 23 | |
P V value | V=23m/min | MPa·m/min | 20 | 23 | - |
V= 5m/min | 25 | - | 36 | ||
Kinetic coefficient of friction b) | P=0.3MPa V=23m/min |
0.26 | 0.30 | 0.35 | |
P=1MPa V=10m/min |
0.30 | 0.35 | - | ||
Stationary abrasion loss b) | P=1MPa V=23m/min |
mg/(h·cm2) | 0.50 | 0.57 | - |
P=2MPa V= 5m/min |
0.80 | 0.80 | - | ||
Abrasion rate c) | V=23m/min | m3/(kg·m) | 0.01 | 0.12 | - |
V= 5m/min | 2.0 | 3.6 | - |
a) ASTM DIO44, Wheel CS-17, Load 1000 g
b) Suzuki abrasion tester, non-lubricating, counterpart material S45C
c) Okoshi abrasion tester, load 3.7 kg, travel distance 100 m
Ⅶ. Weatherability
TORAYCON™ PBT Polymer degrades little when exposed to ultraviolet rays. Abbildungs 8-12 show the results from accelerated weathering and outdoor exposure tests performed on 1401X06 and 1101G-30.
Both 1401X06 and 1101G-30 exhibit minimal physical degradation or dimensional change when exposed to the outdoors. That said, as is the case with other resins, applying white or black coloration is recommended for applications requiring exposure to direct sunlight for extended durations of time.
Abbildung 8: Change in physical properties resulting from exposure to outdoors (Part 1)
Abbildung 9: Change in physical properties resulting from exposure to outdoors (Part 2)
Abbildung 10: Change in water absorption resulting from exposure to outdoors
Abbildung 11: 1401X06 weatherability (irradiation under Sunshine Weather Meter)
Abbildung 12: 1101G-30 weatherability (irradiation under Sunshine Weather Meter)
Ⅷ. Heat-cycling resistance properties
Tables 6 and 7 show the heat-cycling resistance properties of TORAYCON™ PBT Polymer.
Both the 1401X06 and 1101G-30 grades exhibit superb heat-cycling resistance, with little physical degradation or dimensional change.
However, exercise caution before using TORAYCON™ in applications requiring exposure to hot water for extended durations of time. See below for more details.
That said, as the hot-cold heat-cycling test results in Tables 6 and 7 show, TORAYCON™ can be used in applications where the product is exposed to hot water intermittently or for short durations of time.
Category | Unit | 1401X06 | 1101G-30 | ||||
---|---|---|---|---|---|---|---|
Before | After 15 cycles | After 30 cycles | Before | After 15 cycles | After 30 cycles | ||
Tensile strength | MPa | 56 | 50 | 49 | 140 | 130 | 130 |
Tensile breaking elongation | % | 300 | 280 | 270 | 4.2 | 3.8 | 3.8 |
a) 1 cycle constitutes: room temperature (1 hour) → boiling water (1 hour) → room temperature (1 hour)
Category | Unit | 1401X06 | 1101G-30 | ||
---|---|---|---|---|---|
Before | After | Before | After | ||
Tensile strength | MPa | 56 | 52 | 140 | 136 |
Tensile breaking elongation | % | 310 | 300 | 4.0 | 3.6 |
Impact strength without notches b) | kJ/m2 | NB | NB | 65 | 55 |
Water absorption | % | - | 0.29 | - | 0.21 |
Dimensional expansion | % | - | -0.12 | - | -0.01 |
a) Heat cycling conditions
3 cycles, where 1 cycle constitutes: boiling water (2 hours) → 0°C water (2 hours).
b) Test specimen 1/2"thickness