- HOME
- テクニカル情報
- ナイロン樹脂 アミラン™
- 射出成形
- ナイロンの成形にあたって
ナイロンの成形にあたって
ナイロンの成形上の注意
ナイロンは、結晶性、吸湿性高分子ですから、成形にあたっては次の点に留意して下さい。
- ナイロンの融点と成形温度を表1.1に示します。ナイロンは図1.1に示す通り、溶融粘度の温度依存性が大きいので、成形温度は正確に調節して下さい。
- ナイロンは結晶性高分子なので固化する際の体積収縮が大きく、比較的肉厚(6mm以上)の成形品は巣やヒケができやすく、冷却固化により生じる体積収縮分を補充しなければなりません。
- ナイロンは吸湿性が大きいので、長く放置したペレットを使用する時は0.15~0.2%以下の吸水率まで乾燥して下さい。
タイプ | 融点(°C) | 成形温度(°C) |
---|---|---|
ナイロン 6 | 225 | 245~280 |
ナイロン 66 | 265 | 270~295 |
ナイロン 610 | 225 | 245~280 |
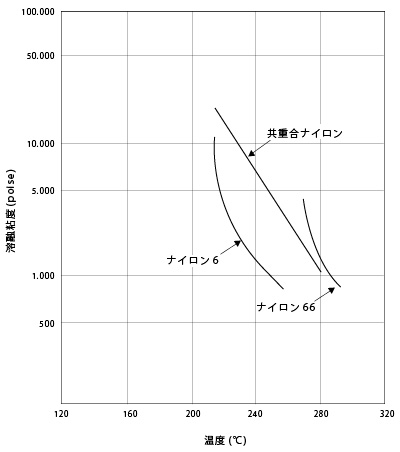
図1.1. 東レナイロン樹脂各タイプの溶融粘度の温度による変化
ナイロン・ペレットの取扱い
Ⅰ. ナイロン・ペレットの包装と保管
東レナイロン樹脂は厳密な品質管理のもとに製造され、防湿袋で密封包装されていますので、袋から取り出したペレットは、開封後ただちに使用すれば予備乾燥は必要ありません。破袋しない限り、保管中の吸湿は殆どないと考えられますが、破袋の可能性のある乱暴な扱いや、極端に湿気の多い場所での保管は避けて下さい。
Ⅱ. ペレットの吸湿とその影響
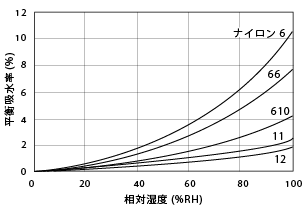
図1.2. 各種ナイロンの平衡吸水率(23°C)
開封後のナイロン・ペレットは大気に触れることにより吸湿します。その吸湿速度と平衡吸水率はナイロンの種類、強化材(例えばガラス繊維)の添加量、ペレットの形状、大気の温度、湿度などに支配されます。
各種ナイロンの相対湿度と大気中平衡吸水率との関係を図1.2に示します。強化ナイロンの場合は、おおむね強化材の重量分率あたりの吸水率を差し引くことにより求められます。
主要なナイロン・ペレットを大気中に放置したときの吸水速度を図1.3~4に示します。これらのデータから、高温多湿期の吸水速度がかなり速いことが判ります。
成形前にある限度以上に吸水したペレットを使用すると、成形品の表面に銀条が生じたり、成形品内部に気泡がが生じるなど成形品外観の問題のほか、分子量低下により物性が損われることがあります。射出成形に使用するナイロン・ペレットの水分率は、0.15~0.2%程度以下が望ましく、そのためには次の事項に注意する必要があります。
図1.3. ナイロン6ペレットの大気中放置下の
吸水速度図1.4. ナイロン66ペレットの大気中放置下の
吸水速度
- 冬期に冷たいペレットを急に暖かい成形室内に持ち込んで開封すると、結露することがあるので、開封する前にあらかじめ暖かい室内に置いておくことが必要です。
- 開封したままでペレットを放置することは絶対に避けるべきで、一旦開封したペレットは使い切ることが望ましく、ペレットが残る場合は密閉できる清潔な金属容器に保管することをお勧めします。便宜的には袋中の空気を十分に抜いてから、開封部を熱シールする、袋の片隅だけを斜めに切ってペレットを取り出し ガムテープなどでシールするなどの方法が考えられますが、防湿性が不十分なので、できるだけ早く使い切るのが望ましいことは言うまでもありません。
- 成形機ホッパー内へのペレットの投入量は、あらかじめ時間当たりの使用量を概算して決めて、ホッパー内で長時間大気にさらされることのないようにする。図1.3~4から、多湿期は30分から1時間程度、低湿期は3~4時間程度を目安にするのが望ましいと考えられます。
Ⅲ. 吸湿ペレットの乾燥
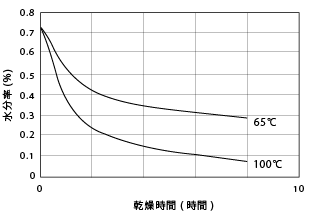
図1.5. ナイロン6ペレットの真空乾燥曲線
A. 真空乾燥
ナイロンを乾燥するにあたり最も推奨される方法です。乾燥条件としては、温度80~120°C、真空度1013hPaが適当です。乾燥時間はペレットの水分率によって決まりますが、10~48時間程度です。尚、高温乾燥品をそのまま取り出して容器に収納すると酸化着色することがあるので、真空下で70°C以下に下げてから取り出すのが望ましい。
ナイロンの真空乾燥曲線の例を図1.5に示します。
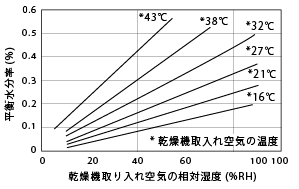
図1.6. ナイロン・ペレットの熱風乾燥条件と
平衡水分率(乾燥温度:80°C)
B. 熱風乾燥
熱風循環棚式乾燥機、ホッパードライヤー、および、これらに除湿装置の付いたものがあります。熱風乾燥でのナイロン・ペレットの乾燥度は、ペレットの形状、初期および最終の水分率、乾燥温度と乾燥空気の温度、相対温度によって決まります。ナイロン・ペレットを80°Cで熱風乾燥したときの乾燥空気の状態と平衡水分率との関係を図1.6に示します。この図から、乾燥度は乾燥機取り入れ空気の絶対湿度(含水量)に支配されることが判ります。普通の熱風循環式乾燥機やホッパードライヤーの場合乾燥空気を直接大気から取り入れるので、乾燥度は大気の相対湿度に支配され、従って、季節によって変動し易いと言えます。低吸湿度のペレットを乾燥して逆に水分が高くなる危険性があり、また、高温多湿期は十分に乾燥しきれない可能性があります。
乾燥温度は高いほど、時間が長いほど乾燥度は向上しますが、高温で熱風乾燥すると酸化着色することがあるので、乾燥温度は制約されます。乾燥温度と時間を変えて熱風乾燥したときのナイロン・ペレットの色調変化を図1.7に示します。通常の熱風乾燥機の場合、酸化着色を防止するには乾燥温度を80~90°C以下にすることが必要です。
ナイロン・ペレットの熱風乾燥曲線を図1.8に示します。過度に吸湿すると、酸化着色しないような温度では短時間で乾燥し切れないことが判ります。
図1.7. ナイロン66ペレットの熱風乾燥による色調変化
図1.8. ナイロン6のペレットの熱風乾燥曲線
(注:乾燥機取りれ空気の露点により異なる)
図1.9~10に除湿装置付きの乾燥曲線を示します。この方式は、水分を含んだ空気を除湿装置を通して脱湿し、その乾燥空気を熱風にして循環、再生使用するものであり、ペレットは常に極めて低湿度の空気に触れることになります。前述の季節変動などが防止できるので、より好ましい方法といえます。但し、この方式の場合も酸化着色に注意を要することは同様であり、除湿能力には限界があるため、ナイロン・ペレットは出来る限り多量に吸湿させないのが好ましいことは言うまでもありません。
図1.9. ナイロン66ペレットの除湿乾燥曲線(80°C)
図1.10. ナイロン66ペレットの除湿乾燥曲線
(70°C 乾燥空気の露点-35°C)
再生使用
スブルー、ランナー等の再生使用をするに当っては、再生使用する材料を乾燥状態で保管しておくか、または成形前に適正な条件で乾燥する必要があります。再生材の性質は熱履歴を受けること、および、強化材科では成形工程で剪断力を受け強化材が損傷することにより変化します。一般的に、再生により機械的強度は低下し、一方、電気特性、摺動特性、燃焼性、耐薬品性等は変化しません。再生による特性変化を、非強化ナイロン6、66について図1.11~12に、ガラス繊維強化ナイロン6,66について図1.13~22に示します。条件は次の通りです。
シリンダー温度(ナイロン6) :260°C
シリンダー温度(ナイロン66):290°C
金 型 温 度:80°C
再生方法:成形品を粉砕機で粉砕し所定の再生材比率でバージン材と均一混合し射出成形に供する。
再生回数:1~5回
非強化品は引張破断伸度以外は、ほぼ100%物性値を保持します。ガラス繊維強化品は再生材比率20%以内であれば、衝撃強さ以外の物性は90%以上保持されるとの試験例を得ています。しかし、再生材の使用に当っては、再生材の管理を厳密に行い、製品の要求特性を十分検討した上で再生材比率を決めることが重要です。また、再生材の粉砕の際、カッター刃の微粉が混入する恐れがありますので、特に、小型の電気部品の場合注意が必要です。その他、材料の微粉のため成形が不安定になることがあります。このようなときは微粉の除去をお奨めします。
尚、UL認定材料については、UL746Dに、工程内リサイクルについて重量で25%以内の再生材の添加を認める旨が記載されています。25%を超える再生材の添加については、ULが確認試験を行い認可する旨が記載されています。
図1.11. 非強化ナイロン6の再生による
引張破断伸度の変化図1.12. 非強化ナイロン66の再生による
引張破断伸度の変化図1.13. 30%ガラス繊維強化ナイロン6の
再生による引張強さの変化図1.14. 30%ガラス繊維強化ナイロン66の
再生による引張強さの変化図1.15. 30%ガラス繊維強化ナイロン6の
再生による引張破断伸度の変化図1.16. 30%ガラス繊維強化ナイロン66の
再生による引張破断伸度の変化図1.17.30%ガラス繊維強化ナイロン6の
再生による曲げ強さの変化図1.18. 30%ガラス繊稚強化ナイロン66の
再生による曲げ強さの変化図1.19.30%ガラス繊維強化ナイロン6の
再生による曲げ弾性率の変化図1.20. 30%ガラス繊維強化ナイロン66の
再生による曲げ弾性率の変化図1.21. 30%ガラス繊維強化ナイロン6の
再生による衝撃強さの変化図1.22. 30%ガラス繊維強化ナイロン66の
再生による衝撃強さの変化