- HOME
- テクニカル情報
- ナイロン樹脂 アミラン™
- 射出成形
- 金型
金型
金型の構造と部品名
ストリッパープレート方式

突き出しピン方式
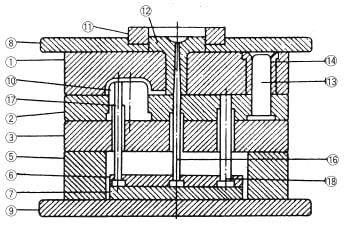
図3.1. 射出成形用金型
- 固定側型板(JISB5106)
- 可動側型板(JISB5106)
- 受け板(JISB5106)
- ストリッパープレート(JISB5106)
- スペーサブロック
- 突き出し板上
- 突き出し坂下
- 固定側取付け板
- 可動側取付け板
- コア
- ロケートリング(JISI∋5111)
- スプルプシュ(JISB5112)
- ガイドピン(JISB5107)
- ガイドピンプシュ(JISB5110)
- ガイドピンプシュ(JISB5110)
- スプルロッビング
- 突き出しピン(JISB5108)
- リターンピン(JISB5109)
金型温度コントロールの重要性
成形品の性能向上、成形の能率化のためには、金型温度調節器やカートリッジ・ヒーターなどを用いて金型温度をコントロールすることが必要です。
ナイロンは結晶性高分子であり、この結晶化度を左右する最大の因子が金型温度です。
Ⅰ. 機能的性質
表3,1に金型温度による機械的性質の変化を示します。成形品の剛性を高く、引張や曲げ強さを大きくしたいときは、金型温度を高くコントロールし結晶化度を高くすることで実現できます。ただし、多少脆くなります。要求性能が反対の場合は金型温度を低くします。
Ⅱ. 成形品の外観
透明性を増すためには金型温度を低く保ちます。表面光沢をよくするには金型温度を30°C以下にするか、80°C以上の高温に保ちます。
なし地(あばたとも云う)は金型表面がきれいに研磨してあるにもかかわらず、成形品表面が無数の小さな凹凸ができている成形不良減少をいいますが、金型温度を30°C以下の低温にするか、80°C以上の高温に保つことにより解決します。
性質 | 単位 | 金型温度(°C) | ナイロン | ||
---|---|---|---|---|---|
6 | 66 | 610 | |||
引張降状強さ | MPa | 20 80 |
75~80 85 |
750 80 |
50 55 |
引張破断伸度 |
% | 20 80 |
200< 150 |
150 100 |
200< 200< |
曲げ強さ | MPa | 20 80 |
95 120 |
100 115 |
72 95 |
曲げ弾性率 | GPa | 20 80 |
2.8 3.0 |
2.7 2.7 |
1.8 2.0 |
Ⅲ. 成形収縮率と密度
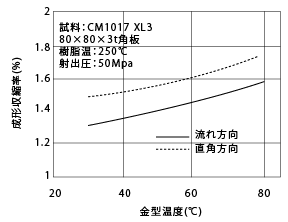
図3.2. 金型温度による成形収縮率の変化
金型温度による成形収縮率の変化の一例を図3.2に示します。成形条件の中で成形収縮率を左右する最大の因子が金型温度です。従って型彫込み寸法値の推定にはどのくらいの型温で成形するか決めて、見積らねばなりません。
金型温度による密度の変化を図3.3に示します。密度は結晶化度に比例するので、金型温度40°C以下では低い値で、80°C以下では高い値で安定しているとみられます。金型温度が50~70°Cの領域は、金型温度の僅かな変動によって結晶化温度が大きく変わる遷移領域であり、この領域では成形品の品質が不安定になるので避けるのが望ましいと考えられます。
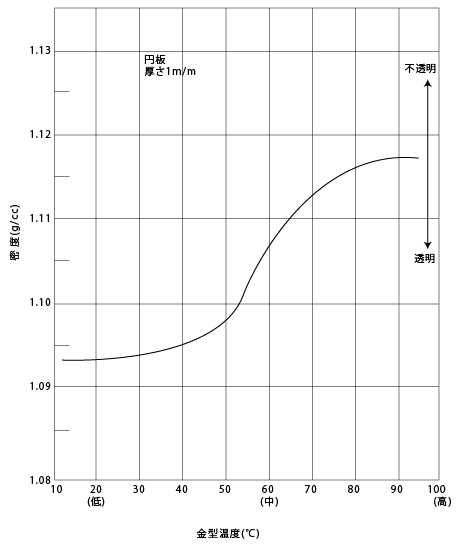
図3.3. 成形直後の密度と金型温度
Ⅳ. 成形性
溶融ポリマーの流動性は後述しますが、金型温度が高いほど良好です。成形サイクルについては型温を低くして 固化を速めてサイクルを上げる場合と、型温を高くして、溶融ポリマーの充填をしやすくしてサイクルを上げる場合とがあります。いずれをとるかは、成形品の形状、金型の構造、成形品の肉圧などによって異なります。
Ⅴ. 成形時の金型温度の変動
金型は溶融ポリマーから熱をとり、冷却水や金型表面から放熱させる一種の熱交換機と考えられます。
安定した連続成形可能な金型温度、すなわち溶融ポリマーからの摂取熱量と冷却水などによる放熱量がバランスとれた定常状態の一定金型温度があります。温度調節している金型でも成形開始から定常状態まで若干の時間を要しますが、温度調節していない金型ではその時間が長く、その温度に達するまでの成形ショットはすべて不良品として捨てなければなりません。その間の成形品は寸法が一定せず、良好な所望の物性が安定して得られません。このような無駄をなくすためにも金型の温度コントロールは重要です。
金型の予熱にガス・バーナーやトーチ・バーナーを使って局部的に加熱することがよくありますが、金型に熱歪みが生じて好ましくありません。
Ⅵ.冷却歪みの防止
成形品の各部分が不均一に冷却すると不均一な収縮による歪みが生じるので、成形品の各部は均一に冷却するよう金型設計することが重要です。もちろん分子配向と成形圧力による歪みは零にすることは不可能ですが、この冷却歪みは金型温度の適切なコントロールによってなくすことができます。
実際の金型設計にあたって、スライド・コア、押出しピン、入子、時にはBe-Cu鋳込みキャビティ・ブロックなどがあって、キャビティ内が均一に冷却するように計算どおりに冷却孔を配置できない場合があります。このような場合には、速く冷却する部分は温水で加熱してブレーキをかけ、全域の冷却(収縮)速度を均一にします。さらにこのような部分的な加熱によって溶融ポリマーのキャビティ内流動をよくして成形性も向上できます。
金型温度コントロールの設計
Ⅰ. 設計上の原則
“冷却孔は突出しピンに優先する”というのが設計の原則です。
一般にキャビティは複雑な形状なので、突出ピンを設計後で金型の構造上許される範囲内で冷却孔を配置し、適当な冷媒流量と温度を苦労して設定するケースが多いようですが、まず金型温度コントロールから金型設計を着手することが重要です。
Ⅱ. 金型の伝熱面積
金型温度コントロールをするうえに必要な金型冷却孔の伝熱面積は次式で表わされます。(外気への放熱、型板、ノズルタッチの伝熱を無視した場合)
ここで
A:伝熱面積(m2)
W:成形品の重量(kg)
N:単位時間当たりのショット数(1/h)
Cp:樹脂の比熱(1.4~2.1)(J/g・°C)
C:冷却水の比熱(4.2)(J/g・°C)
t1:樹脂の温度(°C)
t0:成形品の取出し温度(°C)
ΔT:金型と冷却水の平均温度差(°C)
h:冷却孔側の境膜伝熱係数(90~140)(W/m2・°C)
λ:冷却水の熱伝導率(600~700)(W/m・°C)
d :管径(m)
u :冷却水の流速(m/s)
ρ:冷却水の密度(1000)(kg/m3)
μ:冷却水の粘度(0.001)(Pa・S)
上記の数値をある程度仮定して得たモノグラフが図3.4です。これから得られた伝熱面積を最小値として参照下さい。
問題例1
1ショット重量70g、ショット数60ショット/時間、で成形する時金型の冷却孔の伝熱面積を推定する。
〈解〉
図3.4のモノグラフ上でW=70gの点とN=60shot/hrの点を結び、A線上に交叉する点、A=400cm2が求める所要伝熱面積です。
問題例2
金型の冷却孔の太さを12.7φとすれば、上記問題の場合の冷却孔の長さを推定せよ。金型の大きさが30cm角ならばストレートの孔を何本あけたらよいか。
(解)
少なくとも100cm以上の冷却孔の長さを必要とします。
また、一辺が30cmの金型ではストレート孔を3.3本以上、すなわち4本あける必要があります。
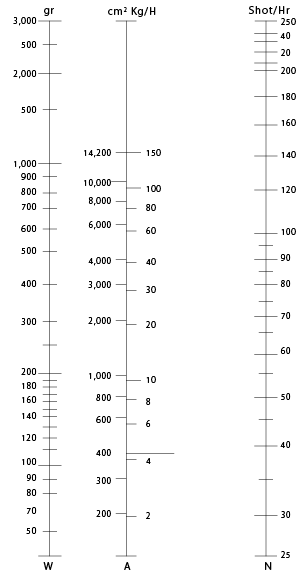
図3.4. 金型の所要伝熱面積
Ⅲ. 冷却孔の分布と大きさ
理論的には溶融ポリマーがキャビティ内に持ち込むエンタルピー分布、あるいは重量分布に相似します。
この冷却分布が適正であるかどうかをテストするには、所要の冷却時間を短縮させて成形した時の硬化状態をチェックします。
冷却孔の太さは9.5~12.7mmφが適当で、そしてキャビティ面から25~40mmのへだたりが必要です。近過ぎますと不均一な冷却をおこし成形品に冷却歪を生じ、遠すぎますとその効果に時間がかかります。
冷却水の流れの方向はランナに対して遠い方のキャビティから近い方に向って冷却が進み、同一キャビティ内ではポリマーの流れ方向に対して向流になっていることが望ましい。
図3.5. 角型コアの冷却(1)
図3.6. 角型コアの冷却(2)
図3.7. 流式冷却水路
図3.8. せき板を設けた冷却孔
図3.9. 太い円形コアの冷却
図3.10. 細いコアの冷却(噴流式)
図3.11. リブ状冷却水路
図3.12. プローブレーカを設けたコア
図3.13. 併列に冷却したコア
図3.14. キャビティ側の冷却方法
図3.15. 絶縁板をりつけたスプールブッシュ
図3.16. バルブエジェクタを用いた金型の冷却
図3.17. スプールブッシュの冷却
ガス抜き
成形性をよくするため、高速射出すればするほど、また金型精度を上げるほど、樹脂の流れによって金型内に封じ込められた空気が成形不良の原因をなします。そのため、バリが出ない程度に、出ても簡単に仕上げられるようにガス抜きをつけます。
ガス抜きのとり方は図3.18から図3.21に示します。
ガス抜き不良によって起る成形不良にはディーゼル燃焼によるやけ(高温高圧によって圧縮ガスが燃焼する現象)、ウエルドの融着不良、空気の抱き込みによる気泡の発生があります。
図3.18. 突出しピンを利用したガス抜き
図3.19. 4個取りの連続ガス抜き
図3.20. 連続ガス抜きを設けた金型
図3.21. 突出しピンを利用したガス抜き
抜き勾配
抜き勾配は成形品形状の複雑さ、キャビティ探さ、成形品の肉厚などによって異なりますが、通常1/2~1°以上必要です。
突出し方法
突出ピン位置は離型を円滑にするために充分検討して下さい。その要点は、成形品の離型時に変形や、歪みを残さないように押出ピン位置はバランスよくつける。突出しピンの痕跡が成形品に目立たない位置につける、ピン先面の研磨を充分して離型しやすくなるなどです。スプル突出しのピン形状は図3.22を参照下さい。
成形品突出しの方法のうち、突出しピンによる方法は図3.23に、ストリッパープレートによる方法は図3.24に、スリーブによる方法は図3.25に示します。これらは成形品の形状によって選定して下さい。
図3.22.スプール突出しピンと引抜き方法
A:Z型 B:逆テーパ C:溝つき D:円錐
1.可動型板 2.ランナ 3.スプル・ブッシュ
4.固定型板 5.スプル孔図3.23.突出しピン
1.突出し板(上) 2.突出しピン 3.可動型板
4.固定型取付板 5.スプル 6.スプリング
7.可動側取付板 8.コア 9.成形品
10.型人子 11.スプルブッシュ 12.スプル突出しピン
13.突出し枠 14.固定型板 15.受け板
16.リターンピン 17.突出し板(下)
図3.24.突出しストリッパープレート
1.突出し板(下) 2.保持ボルト 3.固定型取付板
4.スプリング 5.可動型取付板 6.受け板
7.ガイドピン 8.成形品 9.スプルブッシュ
10.固定型枚 11.トリッパープレート 12.リターンピン
13.可動型板 14.型入子 15.コア
16.スプル突出しピン 17.突出し板 18.突出しボルト図3.25.突出しスリーブ
1.突出しスリーブ 2.型人子 3.可動型取付板
4.可動側固定板 5.コア 6.可動型板
7.成形品 8.固定型板 9.スプル
10.リターンピン 11.前進可動型板 12.冷却パイプ
13.型入子 14.突出し板(上) 15.突出し板(下)