- HOME
- テクニカル情報
- ナイロン樹脂 アミラン™
- 射出成形
- 成形品の寸法の出し方
成形品の寸法の出し方
金型の彫込み寸法
射出成形品を形成する金型の彫込み寸法は次式であらわされます。
L=M(1+S-E)・・・・・・・・・・ 7式
ただし、L:金型の彫込み寸法 M:製品寸法 S:成形収縮率
E:環境や使用条件(温度、吸水、クリープなど)による寸法変化
SやEなどの寸法変化の要因を以下の項目で詳細に述べます。
成形収縮
Ⅰ. 成形収縮の定義
線形成形収縮率(成形収縮率は通常これを云う)SL、体積成形収縮率SVは次の式で定義されます。
ただしL0:金型彫込みキャビティ寸法 L:成形後24時間、室温に放置した後の寸法、V0:金型彫込みキャビティ内容積、Ⅴ: 成形後24時間、室温に放置した後の製品体積。
収縮が均一に、かつ等方的に起るならば、なので、8式に代人すると
一般には収縮が均一に、かつ等方的に起らないので10式は成立しません。
Ⅱ. 成形収縮の発生原因
- 溶融ポリマーから凝固冷却する密度変化(これが主原因です)。
- 金型離型後の除圧による弾性回復と塑性変化
- 結晶化度の変化
ナイロンはとくに結晶化度の影響が大きく、この結晶化度は結晶化速度の温度スペクトルの形(注)、その
温度領域を通過する時間、冷却時間に依存します。
注)
- ポリマーに加わる圧力
- 内部ひずみも含めた結晶核の数
- ポリマー分子の易動数
などによって変化します。
Ⅲ. 成形収縮率の推定
成形収縮率は次の順序で推定して下さい。
- 図5.1成形品の肉厚と成形収縮率から、標準の成形収縮率α0を拾って下さい。
- 金型温度、冷却時間によって、α0に加減して修正下さい。
金型温度Tmが50°Cより高く、冷却時間が長い場合、+0.015×(Tm-50)%
金型温度Tmが50°Cより高く、冷却時間が短い場合、+0.010×(Tm-50)%
金型温定Tmが50°Cより低く、冷却時間が短い場合、-0.007×(50-Tm)%
金型温度Tmが50°Cより低く、冷却時間が長い場合、-0.005×(50-Tm)% - 形状によって修正して下さい。
凹凸の少ない、ボスや突起のない平面状の成形品は修正の必要なし。
ⅰ) 軸受やブッシュなどのように円筒形状の成形品は、内径はマイナスに外形はプラスに修正。その修正程度は形状の複雑性に非常に左右されますので、データの蓄積があれば参考にして推定して下さい。 この現象は金型の中子、ピンなどによる吸収の阻止によって起り、残留応力となって成形品中に凍結されます。
ⅱ) なお吸水や加熱によって残留ひずみが解放されますと、収縮が起ります。
複雑な一般成形品は各部で成形収縮率が違います。原則的にⅰとⅱの組合わせで推定して下さい。 - ゲートからポリマーがキャビティの中に充満する際には、分子配向が起ります。その配向性によって修正して下さい。その修正程度は非強化グレードの場合、成形品の肉厚が薄いほど(2mm以下)、射出速度が大きいほど、金型温度が高いほど、流れ方向が直角方向より大きい。ガラス繊維入りは逆。
- ゲート断面積によって修正して下さい。
成形試料 80mm×80mm×t mm
ゲート:フイルム
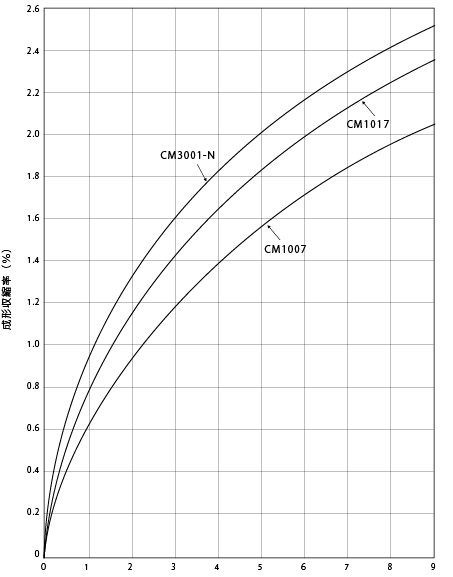
図5.1. 形品の肉厚(mm)
成形条件 : ポリマー温度
CM3001-N ・・・ 270~280°C
CM1007、CM1017 ・・・ 250~260°C
金型温度 ・・・ 40~60°C
吸湿(吸水)による膨脹、収縮
Ⅰ. 吸湿(吸水)現象
ナイロンは吸湿性高分子であるため、吸水によって機械的性質の変化とともに寸法変化も起します。しかし吸湿 現象を理解し、その適切な処理を行なうことによって、かなり精度の高い成形品を得ることができます。 吸湿、吸水現象は微小な物質がその物質へ拡散する現象です。従って拡散方程式を用いて理論的に解析できます。
Ⅱ. 吸水速度
解析を簡単にするため、半無限物体で吸水の方向を一次元として、物体の表面からXなる距離のところにおける
時刻tの濃度をC(X,t)とすれば、濃度の時間的変化は下記の式で表わされます。
ただし Dは拡散常数
8式から任意の時間における平均濃度(t)は
従って
ただし
t:(s) 経過時間
C:(%) 時刻tにおける吸水率
Cs:(%) それぞれの環境条件における平衡吸水率、図5.2参照
W=S/V:(1/m) 形状係数
S:(m2) 露出している表面積
Ⅴ∵(m3) 体積
D:(m2/S) 拡散常数 表 5.1を参照
12式は平衡水分率の80%まで吸湿するのに要する時間を算出するのに適用できます。それ以上の吸湿には適用できませんので注意して下さい。参考に60φ×3mm円枚の20°C水中とRH60%における実測の吸水曲線を図5.3、
図5.4に示します。
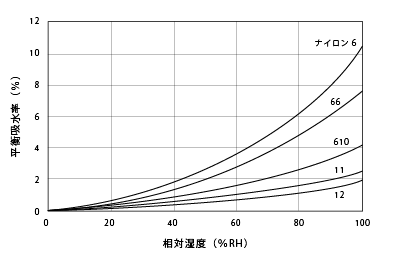
図5.2. 各種ナイロンの平衡吸水率(23°C)
ナイロン. タイプ | 条件 | 拡散常数D(m2/S) | |
---|---|---|---|
CM1017 | 丸棒機械加工品 | 100°C水中 | 3.48×10-11 |
CM1017 | 射出成形品 | 20°C水中 | 7.84×10-13 |
CM1017 | 射出成形品 | 20°C、RH60% | 6.31×10-14 |
CM1011G-30 | 射出成形品 | 100°C水中 | 2.73×10-10 |
CM1011G-30 | 射出成形品 | 20°C、RH60% | 1.75×10-10 |
CM3001-N | 射出成形品 | 20°C、RH60% | 2.01×10-13 |
CM3001-N | 射出成形品 | 20°C水中 | 4.42×10-13 |
図5.3.CM1017の吸水曲線
図5.4. 吸水率の経日変化
60mmφ×3mm円板,20°C RH60%
問題例1
60mmφ×3mmの円板、材質はCM1017、を20°C水中にて飽和の80%吸水率まで吸水するに要する時間を算出する。
<解>
表5.1からD=7.84×1013m2/S
以上の値を12式に代入する
問題例2
上記の成形品が20°C、RH60%空気中において吸水率が平衡吸水率80%まで吸湿するに要する時間を算出する。
<解>
表5.1からD=6.31×1014m2/S W=733の値を12式に代入する。
Ⅲ. 吸水濃度の分布
成形品中の吸水濃度の分布は次式で求められます。
従って成形品中の任意場所、任意時刻における濃度は誤差関数を用いて計算できます。また成形品の吸水率は濃度曲線の積分値であることもわかります。
問題例1.
厚肉板、材質はCM1017を20°C水中にて浸漬した時、49、100、529時間後の濃度分布を求める。
<解> 図5.5(Cs=10.8%)
問題例2.
同じ成形品が20°CRH75%、空気中におかれた時、289、1024、7056時間後の濃度分布を求める。
<解> 図5.6(Cs=5.5%)
図5.5.CM1017 水中濃度分析
図5.6. CM1017,20°C RH75%濃度分布
Ⅳ. 吸湿(吸水)、放散の経日変化
角板(80mm×80mm×3mm)、材質はCM1017、を吸水処理(沸とう水で3時間、2時間、1時間、0.5時間煮沸、常温の水で吸水)したものと、成形のまま何ら吸水処理しないもの、を恒温(230±1°C)室内に放置し、450日間の吸水率の経日変化を測定しました。その結果は図5.7のとおりです。梅雨期の高湿度が時間的に多少ずれて吸水率の増大に影響していることがわかります。
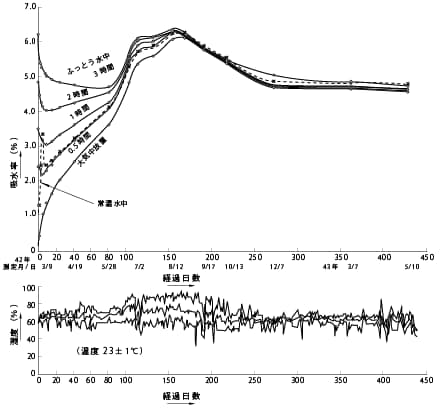
図5.7. 吸水、放散の経日変化
Ⅴ. 吸湿(吸水)による体膨張率
角板(80mm×80mm×3mmと5mm)、材質はCM1017について吸水による体膨張率(体積増加率)を測定し た結果、図5.8のとおりでした。 この実験式は β=0.86X ・・・・14式 ただしβ:体膨張率、X:吸水率 ナイロン6では1%吸水するごとに、約0.086%体積増加することがわかります。
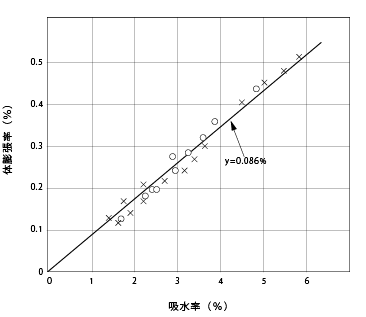
図5.8. 吸水による体膨張率
Ⅵ. 吸湿(吸水)よる線膨張率
等方的に、かつ均一に線膨張する場合
吸湿あるいは吸水によって等方的に、かつ均一に線膨張する場合には下記の式が誘導されます。
V0=a・b・C、Ⅴ=a・b・C(1+α/100)3 、定義から
ただし、V0:吸水前の成形品体積、Ⅴ:吸水した時の成形品の体積
a、b、C:成形品の長さ、幅、高さ、α:線膨張率、β:体膨張率
前節の実験式からβ=0.86%/%の値を15式に代入するとα=0.28%となります。すなわちナイロン6では1%吸水するごとに、約0.28%寸法が増加することがわかります。
一般にナイロンは1%吸水するごとに寸法が0.2~0.3%増すことが知られております。
Ⅶ. 非等方的に、かつ不均一に線膨張する場合
一般成形品の吸水による線膨張は非等方的で不均一です。その主たる原因は分子配向ひずみ(ポリマーの金型内流動による)と残留ひずみ(金型形状の拘束による成形収縮の凍結ひずみ)の、吸水による緩和です。
平板の場合
円枚(60mmφ×3mmと5mm)材質CM1017、角板(80mm×80mm×3mm)材質CM1011G-30、の厚さ方向(2軸)、平面方向(x軸ポリマーの流動方向、y軸ポリマーの流動方向に直角方向)の吸水による線膨張率を測定した一例を図5.9、図5.10、図5.11に示します。これから、
ⅰ 厚さ方向の寸法増加率が意外に大きいことがわかります。しかも成形品の肉厚が薄いほど大きい。
ⅱ 平面方向の寸法増加率は吸水率が2~3%まではあまり変わりません。むしろ若干吸水によって収縮することがあります。
図5.9.円板(60φ×3.5)の吸水による
線膨張率 材質CM1017図5.10. 角板の吸水による線膨張率(平面方向)
材質CM1011G-30図5.11. 角板の吸水による線膨張(厚さ方向)
材質CM1011G-30
これらは分子配向の緩和による影響と考えられます。ここで分子配向ひずみについて詳述します。
分子配向には充填時配向、パッキン時配向、冷却時配向があります。充填時配向とは、ポリマーがキャビティ
充填時に流れる方向に分子配向される状態を指します。これは急激に冷たい金型に庄入される場合、壁面に接触している層は急冷され、零に近い速度となり、中心部になるほど大きい速度になり、従って流れ方向の各層間でせん断応力が生みだされ、鎖状の高分子は引伸しを受け配向します。ガラス繊維入りナイロンの場合、ガラス繊維の配向とも一致します。また薄肉ほど配向が大きくなる事も理解できます。
パッキン時配向とは、ポリマーがキャビティを充満後、プランジャニ次圧力によってゲートがシールするまでポリマーは流動し、この際も若干分子は配向されますが、この状態を指します。射出時間(保庄時間)が短かすぎれば、逆にポリマーは内圧が零になるまで、ゲートがシールする問キャビティ外へ逆流します。いずれにしてもゲートがシールするまでポリマーは圧力が低い方向へ流れ、分子が若干配向します。
冷却時配向とは、冷却時にポリマーは凝固する低温部へおしつけられ、内部のポリマーは動き配向する状態を指します。これは肉厚が不均一なところほどこの配向が大きく起ります。すなわち、空孔(巣)の面に垂直に分子配向が起ります。
以上、分子配向には三種類ありますが、この中で充填時配向が顕著に成形品にあらわれます。
さてこのような分子配向が吸水によってどのように緩和されていくかその過程を考察しますと、ポリマーは流れ
方向に各層状に配向されていますので、その層の間に水が浸入することによって厚み方向には容易に膨張することが可能ですが、平面方向にはかなり長く、分子の緩和は互いに影響を及ぼして容易でないため、あまり膨張できないと考えられます。むしろ厚み方向の伸びが、分子のリコイルを容易にさせ、平面方向の寸法を縮ますことさえ生じます。
円筒状品の場合
軸受(外径60mmφ、内径54mmφ、高さ30mm)材質CM1017の吸水による内外径の寸法変化率を測定した結果を囲5.12に示します。これから①内径の線膨張率は外径のそれより小さいことがわかります。しかも吸水率1~
4%までは膨張でなく収縮が起こっています。外径の膨張率も1~3%までは少ない。
②100°C水中で吸水させたものが、20°C水中で吸水させたものより、線膨張率が小さいことがわかります。
③①の原因は前項の分子配向ひずみの緩和もありますが、ポリマーの冷却時の金型形状(中子などの)の拘束による残留ひずみの緩和が主たるものと考えられます。すなわち残留ひずみが高温になるほど、しかも吸水によって緩和しやすくなり、②の現象も理解できます。
一般成形品の場合
一般形式品の吸水による寸法変化率は平板の場合、円筒状品の場合の複合と考えられ、下記の式であらわされま
す。
Ew=A-B-C ・・・・16式
ただし、
A:吸水による膨張、1%吸水するごとに0.25~0.3%の膨張
B:分子配向ひずみの緩和による収縮、ゲート位置(ポリマーの流れ方向)成形品の肉厚によって影響されます。
C:残留ひずみの緩和による収縮、金型形状、中子、成形条件によって影響されます。
これらA、B、Cの値は多分に経験的なものから割出されますので、データの蓄積を日常の業務に取入れる必要があります。
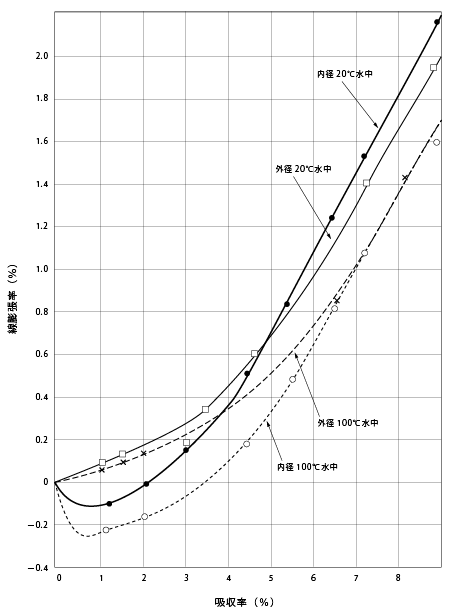
図5.12.軸受(60φ×54×30)の吸水による寸法変化率
温度による膨張、収縮
ナイロンも含めて一般のプラスチック成形品の温度による寸法変化は大きいので注意する必要があります。高温
になると軟化し、変形が生じたり、低温になるとインサート金具部付近でクラックが生じたりします。
温度による寸法変化はポリマーの線膨張係数を用いて算出できますが、実際には適用が困難です。
これは成形品の残留ひずみの緩和が起ったり、ナイロンの場合には結晶性ポリマーなので結晶化が促進されるた
め線膨張係数も一様でないからです。また全体的には成形品の熱膨張、収縮には前節の吸水と同様に異方性が生じ
ます。各項にわたって詳述します。
Ⅰ. 熱膨張係数
各ナイロンの線膨張係数は表5.2のとおりです。これらの数値は残留ひずみのない熱処理された試料で測定されたものです。
ナイロン・タイプ | 線膨張係数 |
---|---|
ナイロン6 | 0.8×10-4/°C |
ナイロン66 | 1.0×10-4/°C |
ナイロン610 | 1.2×10-4/°C |
ナイロン12 | 1.2×10-4/°C |
Ⅱ. 熱処理による結晶化度の上昇
ナイロンの射出成形品の結晶化度は前述したように金型温度によって左右されますが通常の5~15%くらいです。ところで水、流動パラフィン、シリコンオイル、焼入油などで高温で熱処理すると、結晶化度が上昇します。 その測定結果の一例を図5.13に示します。
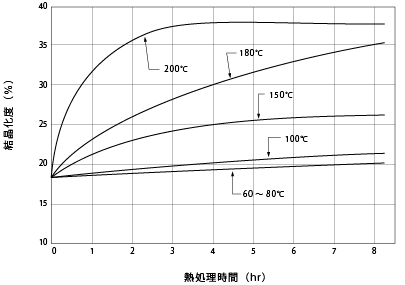
図5.13.処理による結晶化度の変化
さらに熱処理して興味あることは、成形のままの成形品では表層と内部の結晶化度は不均一で、表層は低く、内
部は高いですが、熱処理によって均一にすることができます。表5.3を参照下さい。すなわち、成形条件などのばらつきによって生じる成形品の結晶度の不均一は、熱処理によって均一化できるということです。
この結晶化度の上昇によって密度はあがり、寸法は減少します。
試料採取箇所 | 成形のままのもの | 熱処理したもの (175°C×0-5)hr |
|
---|---|---|---|
ゲート部 | 表面層 | 25 | 31 |
中心層 | 30 | 33 | |
中間部 | 表面層 | 25 | 32 |
中心層 | 30 | 33 | |
末端部 | 表面層 | 24 | 31 |
中心層 | 29 | 33 |
ここで結晶化度について説明します。
ナイロンは結晶性ポリマーですが、ほとんどの場合完全結晶ではなく、結晶と非晶の混在状態で構成されています。そこで全体に占める結晶部の割合を結晶化度と呼びます。そして次のように定義されます。
ただし
dc:結晶質の密度
da:非晶質の密度
d:試料の密度
ナイロンのdc、daを表5.4に示します。
ナイロン・タイプ | dc | da |
---|---|---|
ナイロン6 | 1.212 | 1.113 |
ナイロン66 | 1.24 | 1.09 |
ナイロン610 | 1.157 | 1.041 |
Ⅲ. 残留ひずみの緩和
残留ひずみには一般に分子配向ひずみと、形状からくる冷却ひずみの二つがあります。これらはガラス転移点以上の高温にさらされますと、分子の熱運動が活発になり残留応力も緩和されるようになります。
ナイロンの射出成形品にどのくらいの残留ひずみがあるか測定することはきわめてむずかしい現状です。かなりの残留応力がある場合なら、5%硫酸、5%カセイソーダ水溶液にてソルベントクラックを生じさせるテスト法、熱膨張率測定法、内周削り法などがあります。
一般にナイロンはポリスチレンやポリカーボネートなどの他の熱可塑性樹脂にくらべて、残留応力によるクラックは起りがたい。これはナイロンの吸湿性による破断の伸びの増加と弾性係数の低下によるものと考えられます。
軸受(外径31.75mmφ、内径26.26mmφ、高さ25.40mm)、材質CM3001-Nの油熱処理(155°C、0.5hr)による寸法変化の測定結果を表5.5に示します。この熱処理による寸法変化は前項の結晶化度による影響も加算されていると考えられますが、形状からくる(中子による成形収縮の拘束)冷却ひずみの緩和によって起ったものと考えられます。
成形条件 | 内径収縮率(%) | 長さ収縮率(%) |
---|---|---|
金型温度(°C) | ||
21 38 65 93 |
1.5 1.3 1.0 0.3 |
0.6 0.3 0.4 0.1 |
成形周期(sec) | ||
射出時間/冷却時間 20/20 20/10 10/5 |
1.3 1.2 0.5 |
0.3 0.4 0.3 |
成形圧力(MPa) | ||
140 70 |
1.2 1.4 |
0.4 0.0 |
シリング温度(°C) | ||
315-270-260 345-285-260 370-285-260 |
1.2 0.9 0.8 |
0.4 0.5 0.5 |
Ⅳ. クリープ変形
一定荷重(応力)下で時間の経過にともなって、そのひずみ(寸法変化)が増加する現象をクリープと云います が、プラスチックは常温附近においても、勿論高温になればかなり顕著に起りますので注意する必要があります。 図5.14に応力20MPaでCM3001-N、CM1017の引張クリープ変形を示します。
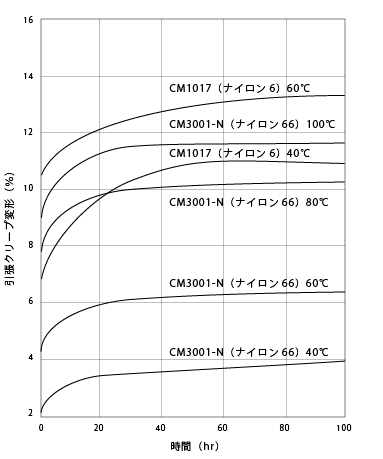
図5.14. CM1017(ナイロン6),CM3001-N
(ナイロン66)の引張クリープ変形(応力20Mpa)
Ⅴ. 熱応力の発生
温度による寸法変化が起りえない状態におかれた時には、その変形量に対応する熱応力が発生します。温度上昇時には圧縮熱応力が、温度下降時には引張熱応力が発生します。これはインサート部品のある場合には低温におけるクラック発生の原因となります。
熱応力は次式であらわされます。
σ=E・α・Δt ‥・・17式
ただしσ:熱応力(MPa)
E:その温度における縦弾性係数(MPa)
α:線膨張係数(1/°C)
Δt:温度差(°C)
この熱応力がそのポリマーの引張、圧縮降伏点以上に達する時、破壊が起ります。さらに前項の残留応力が加算される場合は、はるかに容易に割れが発生することがあります。
(b)まとめ
温度変化による膨張、収縮Etをまとめますと次のようになります。
①常温から高温へ変化する場合
Et=1・α・Δt-Δρ-ε+Ec ・・・・‥ 18式
ただし
1・α・Δt:線膨張、1:成形品の長さ、α:線膨張係数
Δt:温度差
Δρ:結晶化度(密度)上昇による体積収縮の一次元方向
ε:残留ひずみの緩和による収縮
Ec:クリープ変形による膨張(引張応力の場合)
②常温から低温へ変化する場合、
Et=1・α・Δt
引張熱応力がインサートや形状によっておさえられた時に、成形品にクラックが発生する場合があります。
(とくに残留応力が大きく凍結されている時)
残留応力の緩和による収縮
前節ですでに述べましたように、成形品に残留する応力やひずみには、(1)溶融ポリマーの急冷による熱応力に起因するひずみ、(2)分子配向によるひずみ、(3)軟化点、融点附近の材料の容積(密度)変化によるひずみ、があります。そしてこれらのひずみは前述した吸水、温度変化によって緩和され、寸法上では収縮を起します。
Ⅰ. 熱応力によるひずみ
金型中に充填されたポリマーは金型壁面に接触した瞬間には静水力学的に作用され、壁面に垂直に応力が生じます。次第に冷却されて外面がかたまってくると内部に溶融した流体を有しながら剛体となり、いっそう冷却が進むと、表面に接線方向の圧縮応力があらわれ、室温までさがっても成形品に残留応力、ひずみとなって残ります。
キャビティ(金型彫込み形状)の複雑さ、インサートなどによってこの熱応力が凍結されます。一般成形品はこのような残留ひずみが多く残ります。
これらの熱応力が成形品にあらわれる現象として、金型中のポリマーの圧力が冷却の進行とともに下り、この圧力零の点が冷却の初期にあらわれますと、外面の固化部分が応力を保持できず、成形品に凹みとなってあらわれます。
圧力零の点が冷却の中頃にあらわれますと、中心部はまだ流動しうるので外面に引かれ、気泡(巣)が発生します。
圧力零の点が冷却の後期にあらわれますと、凹みや気泡があらわれず、残留ひずみとなって残されます。これが本項目のものなのです。
Ⅱ. 分子配向ひずみ
本項目についてはすでに吸水による膨張、収縮の節で詳述しましたが、充填時配向のみ再述します。
金型中に溶融ポリマーが圧入する時、壁面でのせん断応力の勾配の結果ポリマー分子の流動配向が起り、分子鎖が流れの方向に配列します。この場合温度が高ければ分子は熱弾性的に収縮しますが、外部から冷却されるために、この熱弾性的収縮による緩和が分子鎖間の相互作用のため、制約を受けて凍結し、残留ひずみとなって成形品中に残ります。この分子配向ひずみは成形肉厚が薄いほど大きいので成形収縮の異方性があらわれることも理解できます。
これらの分子配向が抜形品に強く残れば、吸水および高温への変化によって成形品寸法の後収縮となってあらわれます。スチロール樹脂などではき裂の原因ともなるようです。(ナイロンでは分子配向ひずみによってき裂は起りません)
Ⅲ. 容積(密度)変化によるひずみ
ナイロンは結晶性高分子ですから、融点を境として密度が変化します。しかも結晶化度の影響も無視できません。 この密度(容積)の変化が物理的に止められますと、残留ひずみとして成形品に残ります。しかし一般に時間の経過にともない緩和されて行きますので、それほど重要ではありません。
Ⅳ. 残留応力の緩和
以上に述べた残留応力、ひずみの緩和は、吸水、温度による影響によって起ります。本項については前述の各節を参考して下さい。
成形精度
一定の成形機、一定の成形条件(シリンダー温度、金型温度、サイクル、射出圧力、など)連続成形した場合、各ナイロンとも成形寸法のバラツキは図5.15に示すくらい起ると予測されます。
粗雑、標準、精密の違いはどのくらい成形条件を一定にコントロールできるか、成形機、金型温度、材料の流動性などによって決定させるものです。
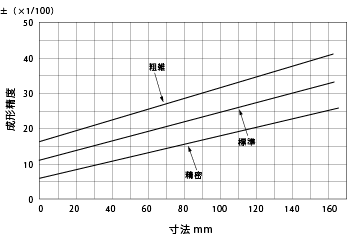
図5.15.成形精度
ナイロン成形品の寸法の安定化処理(まとめ)
Ⅰ. 成形品の寸法精度
ナイロン成形品の寸法誤差発生の主な原因は
- 金型に直接関係するもの
金型の基本的な構造
金型の型式
金型の製作誤差
金型の摩耗 - 成形工程に関係するもの
成形方式の種類
成形条件の変動
成形操作の変動 - 成形材料に関係するもの
グレードの変更
ロットぶれ
潤滑剤の添加量 - 成形彼の経時変化によるもの
吸湿、放散などによる吸水変化
温度変化
クリープ変化
以上の原因がありますので、各項目別に寸法精度を推測し総和して下さい。
Ⅱ. 寸法安定化のための後処理
- 熱処理
成形品が使用される温度よりも10~20°C高めに熱処理するとよいです。熱処理時間は熱伝導の問題ですから計算できます(熱伝導方程式により)。熱処理剤はナイロンをおかさず、熱的に安定で操業上危険のないものであれば何でも良いですが、一般に水、流動パラフィン、焼入用シリコンオイルが良好です。熱処理液は十分にかきまぜ、局部過熱が起らないように注意しなければなりません。
小型部品を一度に多量行なう時は、金属綱のかごに入れて行なうのが便利です。
所定の熱処理を終えたら浴から取出し、ボール紙製の箱などに入れて、除冷しなければなりません。
使用温度が70°C以下であれば、沸とう水処理で(次項の吸水処理もかねた)、充分です。
- 吸水処理
成形品が使用される湿度を調べ、図5.2から平衡吸水率を把握します。その平衡吸水率より1~ 2%ほど余分に吸水処理を行ないます。
吸水処理時間は12式から算出して下さい。吸水処理の方法は熱処理と同じ方法でよいです。 - 調湿処理
吸水処理によって、成形品が充分吸収し安定化したと考えるのは早計です。すなわち図5.3、図5.4に示されるように表面は10%でも内部は0%というように部分的に吸水率がことなります。そこで使用される雰囲気中に放置して調湿します。調湿期間は成形品の肉厚によって左右されますが、3週間以上かかります。図5.7にその一例があります。