- HOME
- テクニカル情報
- PPS樹脂 トレリナ™
- 各種性質
- 二次加工
- 物理的接合について
物理的接合について
Ⅰ. 熱溶着法について
複数個の成形品を組み合わせて1個の部品を作製する場合、熱可塑性樹脂では熱溶着法が一般的に用いられます。熱溶着法は、Fig.10.7に示すように、成形品の接合部界面をFig.10.1に示したような方法を用いて溶融し、加圧しながら冷却することで接合を行います。溶着部の強度は、接合界面の分子の拡散による絡み合いと結晶化により発現するため、基本的にはPPS樹脂は同種同士の組合せとなりますが、SP値(Solubility Parameter)が近いポリマーであれば異種材同士でも接合できる場合があります。PPS樹脂を用いて、他のポリマー(ポリアミドやポリエステル等)と接合する場合は、ポリマーアロイ化など特殊な材料設計が必要となります。フィルムやチューブなどの多層押し出し成形で異種材同士を組み合わせるケースもありますので、具体的に接合したい異種ポリマーについては当社にご相談ください。
Fig.10.7 熱溶着のメカニズム
Ⅱ. 熱溶着法の特徴比較
トレリナ™の接合に用いることができる代表的な熱溶着の特徴をTable.10.8に示します。溶着方法により特徴が異なるため、製品の大きさや形状、製品に求められる特性、経済性(装置価格やサイクルなど)を考慮して選択する必要があります。
Table.10.8 熱溶着法の特徴比較
項目 | 代表的な熱融着法 | |||||
---|---|---|---|---|---|---|
熱板溶着 | 超音波溶着 | 振動溶着 | スピン溶着 | レーザー溶着 | DSI成形 | |
適合形状 (制限有無) |
極端な3次元形状以外 | 比較的小さい部品 (成形品サイズによる制限) |
極端な3次元形状以外 (振動方向による制限) |
円筒形のみ | 比較的肉厚の薄い部品 (レーザービームの透過による制限) |
金型から抜ける形状 |
適合材料 | 熱可塑性樹脂一部不可 | 熱可塑性樹脂全般 | 熱可塑性樹脂全般 | 熱可塑性樹脂全般 | 一部不可 (透過材と吸収材の組合せ) |
熱可塑性樹脂全般 |
接合部外観 | 一部はみ出し | 一部はみ出し | 一部はみ出し | 一部はみ出し | 良好 | 良好 |
溶着サイクル | 遅い | 速い | 速い | 速い | 速い | 製品取出し 1回/2ショット |
消費電力 | 小 | 小 | 中 | 小 | 小 | 大 |
再現性 | 中 | 高 | 高 | 高 | 高 | 高 |
内臓部品への影響 | 熱 | 振動 | 振動 | 回転 | なし | - |
Ⅲ. トレリナ™のグレード選定について
熱溶着法を行う場合、どの方法を選択しても分子の絡み合い効果を強めて、高い溶着強度を得るために必要な特性は総じて共通しています。材料選定に当たっては、製品特性に合わせた機械特性などに加えて、以下の点についても配慮してください。
◆熱溶着用PPSを選定する際のポイント
- リニア型PPS
- 高分子量(低流動性)
- 固化が遅い(低結晶化温度、エラストマー改質など)
- 強化材料の含有率が低い
◆トレリナ™熱溶着推奨グレード
非強化PPS樹脂全般:A900、A670系
リニア型PPS:A602系、A604系
エラストマー改質PPS:A673M
- ※架橋型PPSやハイフィラーグレードも熱溶着は可能ですが、溶着強度や最適溶着条件幅(プロセ スウインド)が推奨グレードと比較すると小さい傾向があります。
Ⅳ. 熱板溶着について
熱板溶着(Hot-plate welding)による接合は、Fig.10.8に示すように成形品の溶着部分を熱板で同時に溶かし、溶けた部分同士を合わせて冷え固まるまで加圧状態で保持することにより接合する方法です。
Fig.10.8 熱板溶着法のプロセス
熱板で成形品を溶かす場合、成形品に直接熱板を直接当てて溶かす接触法と熱板の輻射熱により間接的に溶かす非接触法の2つに大別できます。(Fig.10.8)
接触法は、熱板から成形品への熱伝達率が高いため熱板の温度は樹脂の融点+20~50℃程度でよく、トレリナ™の場合300~330℃の熱板で溶着できます。非接触法と比較して、プロセスウインドは比較的広く取ることができますが、熱板に直接当てることから、糸引きが発生しないように熱板の状態管理(樹脂の離型処理)が重要となります。
非接触法は、熱板と成形品の間に断熱効果が高い空気層が存在するため熱板の温度は接触法よりも高く設定する必要があります。熱板温度は、熱板と成形品の隙間の大きさにもよりますが、通常600℃以上が必要です。ただし、熱板と成形品の隙間が小さすぎる場合や、必要以上に熱板の温度を上げすぎると成形品表面の熱履歴が過剰に高くなり、樹脂の分解によるガス発泡を引き起こして溶着不良となるため、隙間距離と熱板温度の関係を把握することが重要です。一方で、非接触法は、プロセスウインドは狭いものの、熱板に樹脂が付着しないことから熱板の管理は容易であり連続生産に向いています。
溶着に影響する主な条件因子は、熱板温度、加熱時間、溶着代に加えて、接触法の場合は溶融代、非接触法の場合は試験片と熱板の隙間距離(mm)です。溶着代は溶融後の成形品同士を押し込むストローク(mm)または圧力(MPa)、溶融代は加熱時に熱板に成形品を押し込むストローク(mm)または圧力(MPa)であり、溶融代や溶着代が過小の場合、溶融不足や溶着不足となり、過大の場合はバリとなって排出される量が増え、溶着不足になります。
◆試験例 ~トレリナ™の熱板溶着性について~
トレリナ™の熱板溶着性をTable.10.9に示します。非強化PPS樹脂は、熱板温度により伸びが異なるものの、ほぼ母材自身の引張り強さと同じ溶着強度が得られているのに対して、エラストマー改質型のA575W20は母材自身の強度の30%にも満たない溶着強度です。溶着部は、強化材の配向が乱れることや結晶状態が周囲と異なることから応力集中しやすく母材ほどの高い強度は得られません。また、強化材の含有率が高いA310MX04は、見かけの接合面積は同じであっても、強化材がPPS分子の拡散を阻害していることから、溶着に影響する真の接合面積は他の材料よりも小さく溶着強度が低くなります。
Table.10.9 トレリナ™の熱板溶着性(接触法)
"トレリナ" グレード |
熱板溶着条件 | 熱板溶着特性 | ||||||
---|---|---|---|---|---|---|---|---|
熱板温度 (℃) |
加熱時間 (sec) |
溶融代 (mm) |
溶着代 (mm) |
冷却時間 (sec) |
引張り強さ (MPa) |
引張り破断伸び (%) |
破壊状態 | |
A670X01 (非強化PPS) |
300 | 60 | 0.8 | 0.9 | 30 | 42 | 14 | 母材表層破壊 |
310 | 60 | 0.8 | 0.9 | 30 | 43 | 35 | 母材破壊 | |
A575W20 | 320 | 30 | 0.9 | 1.2 | 30 | 40 | 1.0 | 母材表層破壊 |
A310MX04 | 320 | 30 | 0.9 | 1.2 | 30 | 16 | 0.4 | 界面破壊 |
形状:ASTM1号形状の1/2切削片、溶融代と溶着代のストロークは両側移動量
Ⅴ. 超音波溶着について
Fig.10.9 超音波溶着法
超音波溶着(Ultrasonic welding)は、超音波(20~40kHz)を利用して接合面を摩擦発熱により溶融して接合する方法です。超音波溶着は、Fig.10.9に示すように成形品の一部にホーンと呼ばれる共振体を接触させて成形品に超音波振動を加えます。超音波による振動エネルギーは、接合界面で相手材との繰り返し衝撃により熱エネルギーに変換(摩擦発熱)されPPS樹脂を溶融させます。このように、ホーンから離れた位置で接合する方法を伝達接合といい、超音波の減衰を抑制し成形品内を効率よく伝播させて接合部に集中することが重要です。一般的に、成形品が大きくなるとホーンと接合面の距離が長くなり、超音波の減衰により溶着性が低下するため、小型の成形品に適している溶着方法です。
超音波溶着を行う場合、ホーンの形状、ホーンを接触させる位置、接合部の設計などを最適にすることで高い溶着強度や溶着時間の短縮ができます。特に重要な接合部の設計については、フラットな接合面同士(バットジョイント)では超音波が拡散して溶着にバラツキが生じることからFig.10.10に示すように接合部面に突起状のエネルギーダイレクター(以下ED)を設けることが有効です。EDの大きさは、溶着面積の大きさに合わせることが重要であり、過小な場合溶着面積が小さくなるため溶着強度不足となり、過大にするとバリになります。
Fig.10.10 エネルギーダイレクター(バットジョイント)
トレリナ™は結晶性が高いため成形品のサイズが大きくなるに従いEDでは、十分な溶着強度が得られない場合がでてきます。その際は、Fig.10.11に示すシェアジョイント、スカーフジョイント、ビートジョイントなどの継ぎ手形状にすることで溶着強度を高めることができます。特に円筒形状においては、シェアジョイントが超音波に有利です。
◆試験例 ~トレリナ™の超音波熱板溶着性について~
Fig.10.12に示すハット型の円筒形状(シェアジョイント)を用いたトレリナ™の超音波溶着性をFig.10.13~14に示します。溶着荷重は、上部成形品を固定し、開口部から圧子を5mm/minの速度で挿入し、下部成形品に負荷をかけて溶着部で破壊したときの荷重を示します。超音波溶着性は、溶着時間や加圧力に依存して変化するものの、溶着時間の方がより溶着強度に影響していることが判ります。加えて、高い加圧力で溶着時間を長くすると、溶融代がバリとして排出されることや残留ひずみの影響が強くなるため溶着強度が低下する恐れがありますので、適性な範囲での条件設定をお願いします。また、架橋型ポリマータイプのA504X90と比べるとリニア型ポリマータイプのA604が超音波溶着性に優れる傾向が認められます。
Fig.10.11 超音波溶着の継ぎ手構造例
Fig.10.12 超音波溶着性評価形状(東レ法)
Fig.10.13トレリナ™の超音波溶着性(溶着時間依存性)
Fig.10.14トレリナ™の超音波溶着性(加圧力依存性)
- ※発振周波数:20Hz、加圧力依存性:加圧力=100kPa
Ⅵ. 振動溶着について
振動溶着(Vibration welding)は、一方の成形品を固定し、他方の成形品を加圧しながら横振動させ、摩擦溶融させて接合する方法です。振動溶着機は、Fig.10.15に示すように電磁コイルとスプリングの反発力を利用して横方向の振動を発生させ、一定の振幅(振動数240Hzでは1~1.8mm)で接合面を繰り返し摩擦します。摩擦発熱により成形品表面から徐々に溶融代を形成していく一方で、加圧力により溶融代の一部はバリ(Flash)として排出され、設定した溶着深さ(1~2mm程度)に達したところで冷却工程に移ります。振動溶着は、溶着時間が3~10秒程度かかることから、超音波溶着と比較して溶着サイクルが長いこともあり、成形品サイズが大きく超音波溶着できない場合に用いられます。例えば、自動車のインテークマニホールドなど成形品サイズが大きく複雑な形状の中空体を形成する方法として採用されています。
振動溶着を検討する際の注意点として、横方向の振動に限定されることから、接合面が3次元の複雑な形状などは部品を複数に分割しないと接合できないことがあるため、振動方向に配慮した接合部の設計が必要です。また、Fig.10.15に示す一般的なジョイント形状は振動エネルギーが分散して溶着性のばらつきの原因となることから振動エネルギーを接合部に集中させるために溶着リブを設けることやバリ取り処理をなくすためにバリ溜まりを設けることが有効です。
Fig.10.15 振動溶着機の構成及び接合部の形状例
Fig.10.16 振動溶着における3つのフェーズ
振動溶着時の接合部の状態は、Fig.10.16の時間と溶着深さの関係に示すように、溶着開始直後から融点近傍に達するまでのクーロン摩擦領域(Ⅰ)、固体状態から溶融状態に遷移する遷移領域(Ⅱ)、十分融点に達して安定的に溶融が進む定常溶融領域(Ⅲ)の3つのフェーズに分けることができます。溶着時間は、これら3つのフェーズの合計時間であり、材料組成以外では主に振幅、加圧力、溶着深さの3つの条件因子で決まってきます。特に、加圧力は、摩擦係数や定常溶融領域の傾きに影響する重要な因子です。
また、Fig.10.17に示すように溶着リブを設けた接合の場合、溶着強度に寄与する有効溶着範囲(図中記号W)に注意する必要があります。同じ溶着深さであっても低加圧時と高加圧時では溶着リブのコーナーの溶融状態に違いが生じます。それによって、溶着面積に違いがでるため、溶着時間は長くなるものの加圧力が低い方が溶着強度が高くなる傾向があります。
Fig.10.17 溶着リブの有効溶着範囲について
◆試験例1 ~溶着リブ付成形品の加圧力依存性について~
Fig.10.18に示すパイプ形状(溶着リブ付)を用いて振動溶着により中空成形品を作製し、水圧試験による耐圧強度を求めました。Fig.10.19に加圧力と溶着時間の関係を示すとおり、加圧力に依存して溶着時間が短くなります。これは、加圧力が強いほど接合面の摩擦係数も高くなることから、クーロン摩擦領域が短くなり、更に定常溶融領域の傾きが大きくなるためと考えられます(Fig.10.16)。一方で、Fig.10.20に示すようにトレリナ™A604(GF40%強化)は加圧力を強くすると耐圧強度は低下傾向を示します。これは、加圧力が高くなるほど有効溶着範囲が小さくなることに加えて、残留ひずみが大きくなるためと考えられます(Fig.10.17)。一方、トレリナ™A673Mは強化材の含有率が低いことに加えて、エラストマーにより残留ひずみや応力集中の緩和効果が働くためA604よりも溶着性が優れています。
また、自動車のインテークマニホールドなどに用いられるナイロン樹脂(N6GF30%)と比較すると、結晶性の違いなどによりPPS樹脂はやや低めです。
Fig.10.18 耐圧試験用成形品形状及び溶着部形状
Fig.10.19 加圧力と溶着時間の関係
Fig.10.20 加圧力と耐圧強度の関係
- ※溶着深さ:1.5mm、振幅:1.5mm、成形温度:320℃、金型温度:80℃(低温金型成形)、アニールなし
耐圧強度:水圧試験機付属の圧力ゲージ値
◆試験例2 ~トレリナ™の振動溶着性~
Fig.10.21に示す試験片(溶着リブなし)を用いて振動溶着し、短冊状(t3mm)に切削(端面はフライス加工)して曲げ試験片を作製しました。Fig.10.22にGF強化グレードの振動溶着性を示します。GFの含有率が低く、固化の遅いA602L X01(GF20%強化)は振動溶着性が高い傾向にあります。また、架橋型ポリマータイプのA504X90と比べるとリニア型ポリマータイプのA604が超音波溶着性に優れることがわかります。エラストマー改質および非強化グレードの振動溶着性をFig.10.23に示します。強化材の含有率が高いA575W20は溶着強度が低いのに対して、非強化PPSは溶着強度が高いことがわかります。特にエラストマーで改質したA670T05は母材と同等の溶着強度であり振動溶着性に優れています
Fig.10.21 振動溶着性評価試験片の作製方法および試験条件
Fig.10.22 GF強化グレードの振動溶着性
Fig.10.23 エラストマー改質・非強化グレードの振動溶着性
- ※溶着深さ:1.5mm、振幅:1.5mm、成形温度:320℃、金型温度:80℃、アニール:130℃×1hr
Ⅶ. レーザー溶着について
レーザー溶着(Laser welding)は、基本的にラップ接合で用いられる方法であり、Fig.10.24に示すようにレーザー光線のエネルギーをレーザー吸収材の表面で熱エネルギーに変換し溶融させ、更に他方の成形品を熱伝達により溶融させてお互いを接合する方法です。レーザー溶着は金属でも用いられることが多い工法ですが、金属のラップ接合は表面から接合部まで全てを溶かし込むのに対して、熱可塑性樹脂の場合は前述したとおり透過材を通してレーザー光を接合部で熱エネルギーに変換することから接合部のみが溶融するため熱による歪が小さく高い溶着強度を得ることができます。また、熱板溶着などの熱溶着法では、溶融代の一部がバリとして排出されますが、レーザー溶着は溶融代を排出することなく溶着できるためバリレス化が図れることが大きな特徴です。一方で、透過材と吸収材の組合せによる制限があり、一般的にはナチュラル色(透過材)とカーボンブラックなどで着色した黒色(吸収材)の組合せになります。
レーザー溶着において、接合面の加圧は熱板溶着などのように外力で溶融代同士を押し込むことはなく、基本的には溶融時の体積膨張(比容積変化)によって接合界面に発生する圧力上昇を利用して行います。 レーザー溶着で設定する加圧力は、成形品同士の隙間が大きいと比容積変化による圧力が十分得られないことと、熱伝達による透過材の溶融不良となることから、矯正・保持することを目的としています。
Fig.10.24 レーザー溶着方法およびメカニズム
熱可塑性樹脂のレーザー溶着は、前述した通り透過材と吸収材から構成されますが、特に透過材のレーザー透過性が重要です。レーザー光線には、半導体レーザー(波長:635~940nm)、Nd:YAGレーザー(波長:1060nm)、CO2レーザー(波長:9600、10600nm)など様々ありますが、透過材には使用波長領域の透過率が15%以上、更にプロセスウインドを広くする(生産安定性向上)ためには20%以上必要です。一般的にPPS樹脂のような高結晶性ポリマーに強化材を配合した材料は、結晶構造部分や強化材(GFや無機フィラ-)によりレーザー光線が反射や拡散等により成形品中で減衰し、接合面ではなく透過材でエネルギー変換されて溶融するためレーザー溶着には不向きな材料です。
トレリナ™A602L X01は、PPSポリマーの結晶性や強化材を最適化することによりレーザー光線の減衰を抑制し、高いレーザー透過率を実現したレーザー溶着用グレードです。Table.10.10に特性を示します。
Table.10.10 トレリナ™ A602L X01の特性 (レーザー溶着グレード)
項 目 | 単 位 | レーザー溶着グレード | 一般グレード | |
---|---|---|---|---|
A602L X01 | A604 | |||
密 度 | kg/m3 | 1480 | 1660 | |
引張り強さ | MPa | 140 | 190 | |
引張り伸び | % | 2.0 | 2 | |
曲げ強さ | MPa | 200 | 290 | |
曲げ弾性率 | GPa | 8.0 | 15.0 | |
シャルピー衝撃強さ | kJ/m2 | 9 | 11 | |
レーザー光線透過率 (波長:940mm) |
t1mm | % | 35 | 17 |
t2mm | % | 23 | 6 | |
t3mm | % | 9 | 2 | |
レーザー溶着強度 | 2mmt | MPa | 42 | 溶着不可 |
- ※レーザー溶着条件: 出力30W、走査速度:5mm/sec、ラップ接合
◆レーザー溶着性の評価方法について
レーザー溶着性は以下の条件にて作製した試験片の引張せん断強さで求めています。
Fig.10.25 レーザー溶着形状
(溶着試験片の作製条件)
溶着機: 定格出力35W 半導体レーザー
波 長: 940nm
焦点径: 0.6mmΦ (ジャストフォーカス)
接合形式: ラップ方式(Fig.10.25)
溶着長さ: 20mm
引張り速度: 1mm/min
レーザー透過材: トレリナ™A602L X01 (t1mm)
レーザー透過率: 35% (波長:940nm)
◆試験例1 ~レーザー溶着条件の依存性について~
レーザー溶着条件と溶着強さの関係をTable.10.11及びFig.10.26~27に示します。吸収側の表面熱量が0.14J/mm以下では未溶融となり、0.88J/mm以上になると発泡形態が確認されることから、過大な入力エネルギーにより400℃以上に樹脂温度が達したため分解ガスにより発泡していると考えられます。
また、Fig.10.26に示す引張りせん断荷重は、吸収側表面熱量に依存して高くなるものの、同時に溶着面積も大きくなることから、実質的な溶着面積で除して引張りせん断応力(Fig.9.28)に換算すると、約0.25~0.7J/mmの表面熱量で溶着強度が飽和しており、0.7J/mmより熱量が高くなると発泡により溶着強度が低下することがわかります。そのため、トレリナ™A602L X01を用いてレーザー溶着を行う場合は、約0.25~0.7J/mmの熱量となるように条件を設定することで安定した高い溶着強度が得られると考えられます。
Table.10.11 トレリナ™A602L X01 レーザー溶着条件と溶着強さの関係
項目 | 単位 | 結 果 | |||||||
---|---|---|---|---|---|---|---|---|---|
出力 | W | 20 | |||||||
走査速度 | mm/sec | 50 | 30 | 25 | 20 | 15 | 10 | 8 | 5 |
吸収側表面熱量※1 | J/mm | 0.14 | 0.23 | 0.28 | 0.35 | 0.47 | 0.70 | 0.88 | 1.40 |
溶着状態(断面)※2 | - | ×(未着) | ○ | ○ | ○ | ○ | ○ | ×(発泡) | ×(発泡) |
引張りせん断荷重 | N | 0 | 583 | 770 | 980 | 1125 | 1270 | - | 1000 |
引張りせん断応力 | MPa | 0 | 38 | 38 | 38 | 38 | 36 | - | 20 |
溶着面積※3 | mm2 | 0 | 15.3 | 20.3 | 25.8 | 29.6 | 35.3 | - | 50 |
- ※1 吸収側表面熱量(J/mm)=出力(W)/走査速度(mm/sec)×透過側試料の透過率(%)
- ※2 溶着状態 : 断面の偏光顕微鏡観察より状態を確認。問題なし=○、問題あり=×
- ※3 溶着面積 : 引張り試験後の破面観察により溶着している面積を求めた。
Fig.10.26 レーザー溶着条件と引張りせん断荷重の関係
Fig.10.27 レーザー溶着条件と引張りせん断応力の関係
◆試験例2 ~レーザー溶着時の隙間の影響について~
Fig.10.28 隙間(擬似)形成方法
レーザー溶着は、接合面に隙間があると溶着強度に影響がでます。隙間ができる主な原因として、成形品のソリやヒケが挙げられます。Fig.10.28に示すように透過材と吸収材のオーバーラップ部にスペーサーを挿入して擬似的に隙間を作りレーザー溶着を実施しました。結果をFig.10.29~30に示します。レーザー溶着における隙間依存性は表面熱量に依存しています。これは、比容積変化による加圧力が低下し、溶着面積の縮小化と相互の分子拡散の程度が小さくなっているためと考えられます。レーザー溶着における隙間は、極力なくす必要があり、0.05mm以上の隙間は溶着部の信頼性が低くなるために注意が必要です。
Fig.10.29 レーザー溶着条件の隙間依存性(せん断荷重)
Fig.10.30 レーザー溶着の隙間依存性(せん断応力)
資料ダウンロード
「防水×振動レス×短タクトタイム」で注目!!レーザー溶着工法に適したPBT、PPS樹脂とは?
昨今の高機能化するデバイス部品の製造では、熱可塑性樹脂を高品質かつ高効率で接合する工程が求められます。内蔵される精密素子への影響がなく、かつタクトタイムを短縮するレーザー溶着工法において、より高品位かつ高効率となるPBT、PPS材料を紹介します。
高性能樹脂のレーザー溶着を実現レーザー溶着向けPBT、PPSの具体的使用方法とその特性
熱可塑性樹脂のレーザー溶着は、部品製造の生産性と質を高める工法として期待されます。レーザー溶着にPBTやPPSを用いる場合の具体的な方法や、それによって得られる部品の特性を解説します。
Ⅷ. 射出溶着(DSI成形)について
射出溶着は、射出成形機を用いて一次成形品を金型にインサートし、次いで二次材を射出成形して溶着する方法です。DSI(Die Slide Injection)成形は、(株)日本製鋼所が開発した2筒式射出成形機で、金型のスライド機構を活用して、一次成形と二次成形を連続して行う2色成形の一種であり、中空体を射出成形で作製することができます。DSI成形による溶着は、Fig.10.31の箱型中空体の接合例に示すように一次成形品同士の接合界面に2次材を射出成形し、二次材の熱量で一次材の接合界面を溶融させて接合させます。接合面の状態を10.3.7項に示した振動溶着と比較すると、振動溶着は振幅分の隙間やバリ溜まりが必要であるのに対して、DSI成形は一次材と接する全面で溶着できるため、溶着面積が大きくとれることから、高い溶着強度が得られます。
Fig.10.31 DSI成形の接合例(振動溶着との比較)
また、一次成形品を一旦取出してからインサート溶着する場合と比較しても、一次成形品の温度が高いことや後結晶化が進行していないことから溶着強度は高くなります。
DSI成形による射出溶着サイクルをFig.10.32に示します。油圧ユニットにて可動側のスライドコアを移動させることにより、一次材と二次材を切り替えながら連続的に中空部品を成形することができます。一次材に求められる成形性は通常の射出成形と同じですが、2次材は1次材を溶融させる熱量を保持した状態で流動末端まで流れることが求められることから流動性や固化特性が重要となります。通常は、溶着性や経済性の観点から同種の組合せで行われることが多いものの、DSI成形機は2筒式であるため、必ずしも同種である必要はなく、一次材の流動性が低い場合や固化が速い場合は、二次材を変更した方がより高い溶着強度が得られる場合があります。
Fig.10.32 DSI成形機による射出溶着サイクル
◆試験例 ~DSI成形による耐圧強度について~
Fig.10.33に示すパイプ形状を用いてDSI成形により中空成形品を作製し、水圧試験による耐圧強度を求めました。Fig.10.34にトレリナ™のDSI溶着性を示します。架橋型ポリマーのA504X90と比較して、リニア型ポリマータイプのA604の溶着性が優れています。また、強化材含有率が高いA310MX04は流動性が低いために2次材成形時のショートショットにより溶着はできないものの、流動性に優れるA575W20は溶着することが可能です。ただし、強化材の含有率の影響により耐圧強度はやや低めです。また、エラストマー改質型のA673Mは耐圧強度が高く、更に同形状の振動溶着と比較して約3倍の耐圧強度が得られます。
Fig.10.33 耐圧試験用成形品形状及び溶着部形状
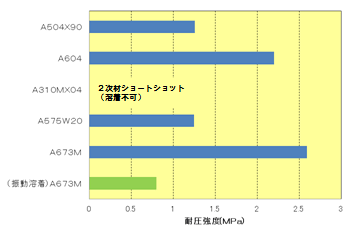
Fig.10.34 レーザー溶着条件の隙間依存性(せん断荷重)
成形機 : 日本製鋼所製 J220E2-M2
成形温度 :
一次材 (ノズル側) 320-320-310-300(℃)
二次材 (ノズル側) 320-320-310-300(℃)
金型温度 : 140℃