- HOME
- テクニカル情報
- PPS樹脂 トレリナ™
- 各種性質
- 二次加工
- ネジ締結、セルフタップ
ネジ締結、セルフタップ
Ⅰ. ネジ(ボルト)締結
樹脂成形品を金属の本体に固定する場合や樹脂同士を接合する場合、成形品の下穴をボルトとナットで締結する方法、成形品のめねじにネジで締結する方法、めねじを用いず下穴のある樹脂ボスに直接タップを立てながらねじ込むセルフタップなどのネジ締結が用いられます。一般的に樹脂は金属よりも強度やクリープ特性(応力緩和)などの面で劣ることから、過度な締め付けトルクによる割れや、ねじ山破壊、緩みが問題になることがあります。
1 ネジの各部名称について
ネジの各部名称をFig.10.35に示します。
Fig.10.35 ネジの各部名称
- ※参考文献:日本機械学会編「機械工学便覧 A.基礎編 B.応用編 新版第9版発行」より
2 ボルト締結時の発生応力について
Fig.10.36 ボルト締結時の軸力
2つの成形品同士をボルトとナットを用いてFig.10.36に示すように締結するとボルト軸部には引張力Fと圧縮力Fがつりあった状態(外力ゼロ)で存在しているとき、このFを予張力(または軸力)といい、初期の締め付け力を示しています。
おねじであるボルトとめねじであるナットをトルク法にて締結する場合、締め付けトルクTと軸力Fには、式10.1に示す関係が成立します。(モトシュの式)
式10.1の右辺第1項は、
ネジ面に働く摩擦トルク、第2項は、ボルトの軸に働くトルク、第3項
は、ナット座面に働く摩擦トルクをそれぞれ示しています。潤滑油を使用せずにトルク法で締結すると、トルクエネルギーの大半(約9割以上)は第1項と第3項の摩擦によって熱に変換されるため、締め付けトルクの効率を高めるためには摩擦係数を下げることが必要です。
また、式10.1を一般的なメートルネジ(α=30°)に適用すると式10.2を得ます。
(潤滑の場合≒0.15)とし、Table.10.12のネジに示す各呼び径(外径)のメートルネジの締め付けトルクと軸力の関係をFig.10.37に示します。軸力が過剰に高いと成形品の締め付け部から放射状にクラックが入る可能性があります。これは、成形品表面には圧縮応力が働いていますが、ボルト穴はインサート金属と同様に横に広がるように変形しようとするため成形品内部には引張り応力が発生し、軸力が許容応力を超えた場合にクラックや割れにいたると考えられます。
Fig.10.37 メートルネジのトルクと軸力の関係
Table.10.12 メートルネジの寸法
ねじの呼び | M2 | M3 | M4 | M5 | M8 | M10 | M12 | M14 | M16 | |
---|---|---|---|---|---|---|---|---|---|---|
呼び径d | mm | 2 | 3 | 4 | 5 | 8 | 10 | 12 | 14 | 16 |
ピッチP | mm | 0.40 | 0.50 | 0.70 | 0.80 | 1.25 | 1.50 | 1.75 | 2.00 | 2.00 |
有効径dp | mm | 1.74 | 2.68 | 3.54 | 4.48 | 7.15 | 9.03 | 10.86 | 12.70 | 14.70 |
谷径dr | mm | 1.57 | 2.46 | 3.24 | 4.13 | 6.65 | 8.38 | 10.11 | 11.84 | 13.84 |
また、ナットをゆるめる場合のトルクは、式10.1の右辺第2項のボルトに働くトルクがマイナス方向に働くことから式10.3で表されます。式10.3から、戻しトルクは締め付けトルクのおおよそ80%程度になります。
Ⅱ. セルフタップ
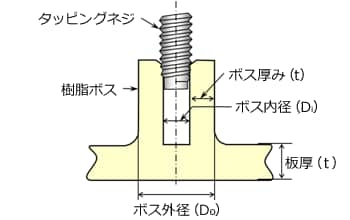
樹脂部品のネジ締結には、下穴のある樹脂ボスを成形品に設けて、タッピングネジを用いてタップを立てながらねじ込んで締結するセルフタップ法(Fig.10.38)が用いられることがあります。
1 タップネジについて
トレリナ™のセルフタップに用いるタッピングネジとしては1~3種タッピングネジのいずれでも加工できますが、ピッチが0.8mm以下の場合にボスの下穴を削ってしまい十分な締結力が得られない場合がありますので注意が必要です。
2 樹脂ボスの設計
タッピングネジの形状に合わせ、かつネジの強度が十分発揮できるよう樹脂ボス部を設計する必要があります。
(1) 下穴径および入り口形状
使用するタッピングネジの有効径と同等かやや小さめで、谷径よりもやや大きめ、ネジの呼び径の85%くらいが適切であり、式10.4に示すセルフタップネジの引っかかり率は50~70%を目処に設計してください。下穴径が過大の場合、ネジ締め付け時に樹脂ボス部のメネジが破壊し、下穴径が過小の場合、樹脂ボスの破壊またはネジ自身の破壊の原因になります。また、下穴の入り口は可能なかぎり皿状や曲面状にして呼び込み穴(深さ:1mm前後、径:ネジ外径+0.1~0.2mm)を設け締結時に入り口付近が欠けないよう配慮してください。
(2) ボス外径
ネジ呼び径の2.5倍が標準です。ボス外径が過小で肉厚が薄いとショートショットやウエルドなどの成形不良の原因となります。また、これらの不良がない場合でも、ボス部の縦割れまたは横割れの原因となります。
(3) ねじ込み深さ
ネジ呼び径の2.5倍が標準です。ねじ込み深さが過小の場合、樹脂のメネジ破壊を起こします。
(4) 板厚
ネジ呼び径と同程度の肉厚とし、強度が不足する場合はコーナーR(0.3~0.5)を十分にとり、更にリブ補強するなどが必要です。板厚を過大にすると、内面にヒケが発生するため注意してください。
3 ボス部の外径設計について
ネジで締め付けていくと、ボス部に縦われと横割れを起こすような応力が発生します
(1) 縦割れについて
Fig.10.39 ボス外径と発生応力の関係
例として、ネジの呼び:M3、=2.57mm、
=7.5mmとして、M3ネジ自身の破壊強度2450Nとして発生応力とボス外径の関係を求めます。Table.10.13より、M3のネジのピッチ及び有効径をそれぞれ用います。(
:=0.5(mm)、
=2.68(mm)) 締付けトルクが既知の場合は、式10.2またはFig.10.32より軸力を求めますが、今回はネジの破壊強度を最大軸力Fとして、それぞれを式10.5及び10.6に代入するとFig.10.39を得ます。発生応力が、100MPa以下となるためには、ボス外径
は7mm以上が必要であることが判ります。
(2) 横割れについて
横割れは、式10.7を用いて求めることができます。
縦割れと同じ条件にて、求めたボス外径と発生応力(横)の関係をFig.10.38に示します。発生応力が、100MPa以下となるためには、ボス外径は6mm以上が必要であることが判ります。
4 下穴深さまたはネジの有効長さの設計について
ねじ込む深さが過小な場合ボス部のめねじ破壊を引き起こします。めねじ山の根元に発生するせん断応力
は式10.8で求めることができます。
Fig.10.40 ネジの有効長さと引き抜き強さの関係
例としてネジの呼び:M3、κ=0.82、=65MPaとし、
とネジの引き抜き強さとの関係をFig.10.39に示します。有効深さが6mm以上あれば、引き抜き強さはネジ自身の破壊強度2450Nを超えます。なお、3種タッピングネジの下部にはテーパーが3~4山ついており、この部分は結合には十分寄与しないため、ボス部の下穴深さはこの分を多く見積もっておく必要があります。
5 ボス取り付け部の板厚設計について
ボス取り付け部の板厚tは式(10.9)にて求めることができます。
例としてネジの呼び:M3、=2450N(ネジの破壊強さ)、
=65MPa、
=7.5mm、
=2.57mmとすると、t=2.45mmとなります。従って、呼びM3のネジに対してはボス部取り付け部の板厚は2.35mm以上あることが望ましいといえます。
6 試験例1
トレリナ™A504X90およびA310MX04の6mmt角板に4.5mmΦの下穴をあけ、M6のタッピングネジを用いて3.92N・mのトルクで締付けました。その後、ヒートサイクル処理(200℃×30min⇔常温×30min×10cycle)を行い、ゆるみトルクを測定しました。A504X90、A310MX04ともにゆるみトルクは0.98N・m(トルク保持率:25%)にまで低下します。ヒートサイクル処理では、高温と常温を繰り返すことによりネジと樹脂ボスの接触面に線膨張差が生じることからゆるみトルクが低下します。また、成形時の金型温度よりも処理温度が高い場合、後結晶化の影響により寸法が変化するためアニール処理を行うことも有効ですが、線膨張差の因子が支配的であるためアニールによる抑制効果はあまり期待できません。そのため、高いゆるみトルクの保持率が必要な場合は、金属インサートで設計してください。
7 試験例2
トレリナ™A504X90とA310MX04の3mmt角板に1.8mmΦ(引掛かり率:35%)の下穴をあけ、M2(d:1.8mm、dr:1.46mm)のタッピングネジを用いて0.4N・mのトルクで締付けると樹脂ボスのめねじ破壊を起こします。一方、下穴径を1.5~1.6mmΦ(引掛かり率:73~92%)にしてネジの締め付けと緩和を繰り返すと摩擦トルクが過大となるためネジ頭の十字穴が破壊します。
また、M2.5(d:2.48mm、dr:1.90mm)のタッピングネジで下穴径を2.1mm(引掛かり率:66%)として、締め付けトルク0.5N/mでネジの締め付けと緩和を10回繰り返した後測定したゆるみトルクは0.35~0.4N/m(保持率:70~80%)であり、ネジ山破壊などは認められませんでした。
Ⅲ. 圧入(プレスフィット)
Fig.10.41 圧入(プレスフィット)
樹脂成形品を組み立てる工程では、金属製のシャフトなどを圧入(Fig.10.41)して固定することが多くあります。圧入は、圧入代(式10.10)によって発生する弾付け力とシャフトと成形品の摩擦によって固定します。圧入に必要な力と引き抜き力は本来等しいですが、実際には応力緩和の影響があることから引き抜き力が小さくなります。
1 許容応力について
圧入代を設計する場合、材料の許容応力を決める必要があります。許容応力は、式10.11に示すように基準強さを安全率で除した値です。これは、ある一定期間内(設定耐用年数)に材料が破壊しないように設ける限界応力であり、製品破壊の支配因子が引張り強さであれば引張り降伏強さや破壊強さ、疲労特性が支配因子であれば疲労強度が基準強さとなります。安全率の決め方は環境条件、製品形状(応力集中、ウエルドなど)、機能の重要性(安全性)などの限界条件により異なりますが、金属などの構造部材は安全率として、静的荷重に対しては3倍、動的荷重に対しては5~10倍とされています。一方、熱可塑性樹脂は未だ明確に確立されていないため、金属と同等か少し高めに安全率を設定することが多いようです。
2 圧入代の設計について
圧入部がボスである場合、圧入代は式10.9~10.10(ラメの式)に許容応力を与えることにより求めることができます。
例として、トレリナ™A504X90(引張り破断強さ:190MPa、ヤング率:16000MPa、ポアソン比:0.36)、A310MX04B(引張り破断強さ:130MPa、ヤング率:25000MPa、ポアソン比:0.34)、A900(引張り降伏強さ:80MPa、ヤング率:4300MPa、ポアソン比:0.40)のそれぞれの円筒成形品(外径:20mmΦ)に金属シャフト(外径
:10mmΦ)を圧入する場合の圧入代を求めます。製品には引張り方向の静的荷重のみが負荷され、安全率は3倍とします。
◆トレリナ™の圧入代計算例
許容応力
式10.9より、
式10.10に代入すると、
式10.8に代入すると、
A504X90の内径:
同様に、A310MX04、A900を求めると
A310MX04の内径 :
A310MX04の内径 :
グレード | 限界圧入代率 (%) |
---|---|
A504X90 | 0.72 |
A310MX04 | 0.31 |
A900 | 1.15 |
強化材の含有率が高く弾性率の高いグレードは圧入時の変形に追従できる比例限度が小さいために圧入代も小さくなります。更に実際の圧入では、成形品の寸法公差、抜き勾配および作業環境温度による線膨張の影響により圧入金属や成形品内径が変動するため圧入代が小さい場合は生産管理がより難しくなります。また、圧入代は、Fig.10.42に示すように外径による影響は小さく、材料の強度と弾性率が大きく影響することから、Fig.10.43に示すように安全率のとり方で大きくことなります。安全率を1として、トレリナ™の各グレードのそれぞれの限界圧入代率について式10.10を変形した式10.11より求めるとTable.10.13となります。PPS樹脂は、剛性が高いため他のプラスチックと比較すると限界圧入代率は低い傾向にあります。圧入代を大限界以上にするとボスの破壊や座屈となるため、過剰に大きくすることは避けてください。
Fig.10.42 成形品外径と圧入代の関係(A504X90)
Fig.10.43 安全率と圧入代の関係(A504X90)
3 加熱圧入について
加熱圧入は、金属を加熱して圧入と同時に成形品表面の樹脂を溶融させて圧入する方法です。そのため、限界圧入代率が小さい場合などに適した方法であり、加熱方法には、シャフトを直接加熱する熱圧入、高周波で加熱する高周波加圧、超音波による摩擦熱により加熱する超音波圧入などがあります。インサートする金属にローレット加工や溝付の抜け防止をしておくことで、溶融樹脂が凹部に入り込むため強固な引き抜き強さを得ることができます。