- HOME
- Technical Information
- AMILAN™ Nylon Resin
- Physical properties
Physical properties
Ⅰ. Water absorption rate
At the molecular level, nylon contains hydrophilic amide groups. Therefore nylon is water-absorbent. Water absorption will result in dimensional change.
Assuming ordinary atmospheric conditions (23°C/60%RH), the equilibrium water absorption is 3.5% for nylon 6, 2.5% for nylon 66, and 1.5% for nylon 610. (The water-absorption rates shown in Table 36 represent values based on immersion in water and therefore differ from atmospheric equilibrium water absorption.) Figure 34 shows the change over time of water-absorption rates for each type of nylon.
Even using the same type of nylon, water-absorption speed will vary depending on the shape of the formed product. Figure 35 illustrates that phenomenon.
Figures 36 and 37 show the water-absorption curve of nylon 6 in 100°C water and in atmospheric air, respectively. As you can see, the relationship between water absorption y (%) and time t can be represented by the following formula.
y=m·tn
The values m and n are constants determined by the type of nylon, shape of the formed product and the molding conditions (crystallinity).
(* Theoretically, n = ½)
Table 3 shows the values for m and n for a 60mmφ×3mm disc and a 12.7×6.35×127mm square bar.
Figure 34: Change in water absorption in 60mmφ×3mm discs at 20°C, RH60%
Figure 35: Change in water absorption per surface area
Figure 36: Water-absorption curve of CM1017 (nylon 6) (in 100°C water)
Figure 37: Water-absorption curve of CM1017
Type of nylon | Disc(60mmφ×3mm ) | Square bar (12.7×6.35×127mm) | ||||||
---|---|---|---|---|---|---|---|---|
20°C water | 20°C RH60% | 20°C water | 100°C water | |||||
m | n | m | n | m | n | m | n | |
CM1017 (nylon 6) | 2.8 | 0.45 | 0.40 | 0.45 | 0.9 | 0.46 | 1.3 | 0.45 |
CM3001-N (nylon 66) | 1.5 | 0.44 | 0.32 | 0.39 | 0.6 | 0.43 | 1.0 | 0.45 |
CM2001 (nylon 610) | 0.6 | 0.40 | 0.24 | 0.38 | 0.2 | 0.46 | 0.5 | 0.44 |
Next we will use a diffusion equation to find the change over time in water absorption of nylon molded products.
For simplification, the water-absorption direction in a semi-infinite object shall be one-dimensional. C(x,t) represents the water present in a place located distance x from the object surface at time t. Using these assumptions, the change over time in concentration C can be expressed as:
Formula (a)
D represents a diffusion constant.
Average concentration (t) based on arbitrary measurements at arbitrary times can be expressed as:
Formula (b)
Wherein:
Cs = equilibrium water absorption under the respective conditions;
D = the diffusion constant (m2/s);
V = the volume (m3) of the molded product; and
S = the surface area (m2) of the molded product.
Relative to actual measurements, the relationship betweenand
forms a straight line until
it equals approximately 0.8. Table 4 shows the diffusion constant D for a number of nylon molded products based on the range where a linear relationship exists.
Form of molded product | Conditions | Diffusion constant D |
---|---|---|
Machined cylindrical rod | In 100°C water | 3.48×10-11m2/s |
Injection molded product | In 20°C water | 7.84×10-13m2/s |
20°C/60%RH | 6.31×10-14m2/s |
Use formula (b) to find the time it takes for an injection-molded product to reach a certain water-absorption rate when immersed in 20°C water:
Formula (c)
t = time elapsed (seconds);
= water-absorption rate (%) after a given time t; and
Cs = equilibrium water absorption (%) under the applicable environmental conditions.
The result obtained is:
= shape coefficient (1/m)
Please note that this formula can only be used to calculate the time required to reach up to 80% of equilibrium water absorption. The time required to reach full equilibrium water absorption is approximately 2.5 times the time required to reach 80% of equilibrium water absorption.
Use formula (c) to find the time required to reach 80% of equilibrium water absorption in CM1017 (60mmφ×3mm disc, ω = 733) immersed in 20°C water. Based on Table 4, we know D = 7.84×10-13m2/s.
Similarly, find the time required to reach 80% of equilibrium water absorption in the atmosphere at 20°C, 60%RH.
Therefore, the time required to reach full equilibrium water absorption would be 330 × 2.5 = 825 hours and 4,110 × 2.5 = 10,275 hours, respectively.
Ⅱ. Dimensional change resulting from water absorption
Figure 38 shows the change over time in dimensions of a CM1017 (nylon 6) square bar left in a desiccator after injection-molding. As you can see, in a dry state at room temperature (20°C, 0%RH), dimensions shrink as the residual stress (induced by the injection-molding process) relaxes. Therefore, the actual dimensional changes at a constant temperature constitute the net effect of dimensional expansion resulting from water absorption and dimensional shrinkage resulting from the relaxation of residual stress from the injection-molding process.
Figure 39 shows shrinkage resulting from heat treatment and change over time in dimensions after heat treatment. After heat treatment, almost no dimensional change can be observed. Dimensions expand about 0.2% to 0.3% for every 1% of water absorption.
Figure 38: Differences in dimensional change in
CM1017 (nylon 6) (12.7×6.35×127mm square bar)
under different environmentsFigure 39: Shrinkage: Change in dimensions immediately following injection-molding, immediately following heat-treatment, and change over time after heat-treatment
Ⅲ. Thermal properties
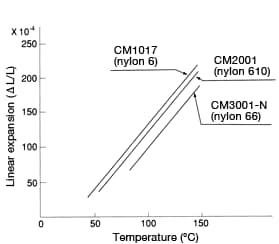
Figure 40: Linear expansion of each type of nylon
Compared to other general-purpose thermoplastic resins, nylon has a very high melting point. The melting point of nylon 66 is 255°C, nylon 6 is 225°C and nylon 610 is 220°C.
However, for applications requiring continuous use under load, temperatures should not normally exceed 100°C for nylon 66, or 70°C for nylon 6 and nylon 610. Compared to metallic materials, nylon’s thermal properties feature low thermal conductivity and a large linear expansion coefficient. Figure 40 shows post-heat-treatment linear expansion in each type of nylon. Even the same type of nylon will exhibit significantly different linear expansion behavior if the nylon’s thermal history differs. This is attributable to the effects of crystallinity and residual stress from injection-molding.
Ⅳ. Aging properties
Nylon is a polymer and thus degenerates when exposed to heat, ultraviolet rays and other elements. Table 5 shows outdoor-exposure test results for CM1017 (nylon 6) and CM3001-N (nylon 66). The effects of exposure on mechanical properties are pronounced in terms of breakdown elongation and impact strength in particular. A dry sample of CM1017 exhibits about 10% degeneration after one year of exposure; however, a sample of CM1017 at equilibrium water absorption exhibits almost no degeneration. After one year of exposure to the elements, degeneration does not advance further in nylon 6 or nylon 66.
Category | Unit | Type | CM1017 (nylon 6) |
CM3001-N (nylon 66) |
|||
---|---|---|---|---|---|---|---|
Exposure time | 0 years | 1 year | 0 years | 1 year | 1 year and 9 months |
||
Tensile strength | MPa | In a dry state Equilibrium water absorption |
85 40 |
75 40 |
80 50 |
67 48 |
56 46 |
Tensile breaking elongation |
% | In a dry state Equilibrium water absorption |
150 200< |
6 40 |
100 200< |
12 35 |
6 30 |
Flexural strength | MPa | In a dry state Equilibrium water absorption |
120 45 |
82 41 |
115 65 |
110 62 |
80 - |
Flexural modulus | GPa | In a dry state Equilibrium water absorption |
3.0 1.0 |
2.8 1.0 |
2.8 1.4 |
2.6 1.4 |
2.4 1.4 |
Izod impact strength |
J/m | In a dry state Equilibrium water absorption |
50 400 |
40~10 - |
50 300 |
40~10 - |
50~30 - |
Rockwell hardness | R scale | In a dry state Equilibrium water absorption |
119 90 |
106 92 |
119 100 |
110 104 |
114 103 |