- HOME
- Technical Information
- AMILAN™ Nylon Resin
- About heat-resistant nylon resins CM1026 and CM3006
- General properties
General properties
Characteristics of heat-resistant grades CM1026 and CM3006
CM1026 is the heat-resistant grade of nylon 6, and CM3006 is the heat-resistant grade of nylon 66. Nylons are heat-resistant resins, having one of the highest melting points among thermoplastic resins. Toray's newly developed heat-resistant grades CM1026 and CM3006 possess the superb heat resistance of nylon and exhibit minimal thermal degradation under very humid conditions. Additionally, Toray offers CM3006E as a heat-resistant grade of nylon 66 designed for applications that require excellent electrical properties at high temperatures.
Mechanical properties
Table 1 compares the mechanical properties of CM1026 and CM3006 to general injection-molding nylons CM1021 and CM3001N. There is virtually no difference in mechanical properties compared to the general grades. Figures 1, 2, 3, 4 and 5 show changes in the general properties (tensile yield strength, flexural modulus and Izod-impact strength) of CM1026 and CM3006 as a function of temperature.
Property | Unit | Test method (ASTM) |
CM1021 | CM1026 | ||
---|---|---|---|---|---|---|
In a dry state | Atmospheric equilibrium water absorption 3.5% |
In a dry state | Atmospheric equilibrium water absorption 3.5% |
|||
Tensile-yield strength | kg/cm2 | D638 | 740 | 310 | 775 | 340 |
Tensile-yield elongation | % | D638 | ||||
Tensile-breaking strength | kg/cm2 | D638 | ||||
Tensile-breaking elongation | % | D638 | 200 | 250 | 150 | 200 |
Flexural-yield strength | kg/cm2 | D790 | ||||
Flexural modulus | kg/cm2 | D790 | 24,000 | 5,300 | 25,000 | 6,000 |
1% compressive-distortion stress | kg/cm2 | D659 | 255 | 55 | 260 | 60 |
Compressive-yield strength | kg/cm2 | D659 | 840 | - | 870 | - |
Shear strength | kg/cm2 | D732 | 590 | 430 | 600 | 435 |
Rockwell hardness | R scale | D785 | 114 | 85 | 115 | 86 |
Izod-impact strength 23°C | kg·cm/cm | D256 | 6 | >50 | 5 | 50 |
(1/2”) -30°C | kg·cm/cm | D256 | 4 | 10 | 4 | 10 |
Linear expansion coefficient | /°C | D696 | 8×10-5 | - | 7×10-5 | - |
Heat distortion temperature (18.56kg/cm2) | °C | D648 | 65 | - | 67 | - |
Heat distortion temperature (4.64kg/cm2) | °C | 150 | - | 155 | - | |
Melting point | °C | 215 | - | 215 | - | |
Specific gravity | - | 1.13 | - | 1.14 | - | |
Water absorption 2 hours at 100°C |
% | D570 | 4.4 | - | 4.3 | - |
Water absorption 24 hours at 23°C |
% | 1.9 | - | 1.8 | - | |
Burning characteristics | UL D635 |
94V-2 Self-extinguishing |
94V-2 Self-extinguishing |
Property | Unit | Test method (ASTM) |
CM3001N | CM3006 CM3006E |
||
---|---|---|---|---|---|---|
In a dry state | Atmospheric equilibrium water absorption 2.5% |
In a dry state | Atmospheric equilibrium water absorption 2.5% |
|||
Tensile-yield strength | kg/cm2 | D638 | 800 | 530 | 810 | 550 |
Tensile-yield elongation | % | D638 | ||||
Tensile-breaking strength | kg/cm2 | D638 | ||||
Tensile-breaking elongation | % | D638 | 110 | 200 | 80 | 200 |
Flexural-yield strength | kg/cm2 | D790 | ||||
Flexural modulus | kg/cm2 | D790 | 28,000 | 12,000 | 28,000 | 12,000 |
1% compressive-distorton stress | kg/cm2 | D659 | 280 | 90 | 285 | 95 |
Compressive-yield strength | kg/cm2 | D659 | 910 | - | 910 | - |
Shear strength | kg/cm2 | D732 | 675 | 600 | 680 | 600 |
Rockwell hardness | R scale | D785 | 118 | 100 | 118 | 101 |
Izod-impact strength 23°C | kg· cm/cm | D256 | 4 | 14 | 4 | 14 |
(1/2”) -30°C | kg·cm/cm | D256 | 2 | 7 | 2 | 7 |
Linear expansion coefficient | /°C | D696 | 10×10-5 | - | 9×10-5 | - |
Heat distortion temperature (18.56kg/cm2) | °C | D648 | 75 | - | 77 | - |
Heat distortion temperature (4.64kg/cm2) | °C | 180 | - | 180 | - | |
Melting point | °C | 255 | - | 255 | - | |
Specific gravity | - | 1.14 | - | 1.14 | - | |
Water absorption 2 hours at 100°C |
% | D570 | 3.9 | - | 3.8 | - |
Water absorption 24 hours at 23°C |
% | 1.5 | - | 1.4 | - | |
Burning characteristics | UL D635 |
94V-2 Self-extinguishing |
94V-2 Self-extinguishing |
Figure 1: Change in yield strength as a function of temperature (nylon 6)
Figure 2: Change in yield strength as a function of temperature (nylon 66)
Figure 3: Change in flexural modulus as a function of temperature (nylon 6)
Figure 4: Change in flexural modulus as a function of temperature (nylon 66)
Figure 5: Change in impact strength as a function of temperature
Resistance to thermal degradation
Ⅰ. Continuous thermal resistance
Not only nylons but all plastic materials exhibit degradation of physical properties when exposed to heat and oxygen in high-temperature atmospheres. The degree of degradation increases with higher temperatures or longer durations of exposure.
The stress-strain curve from a tensile test most clearly expresses this degradation of properties.
Figure 6 shows an example model for nylon 66. When exposed to high temperatures, at first elongation at breakdown declines gradually (the yield point does not change significantly). Finally, the yield point terminates (brittle fracture failure) and stress and elongation decrease.
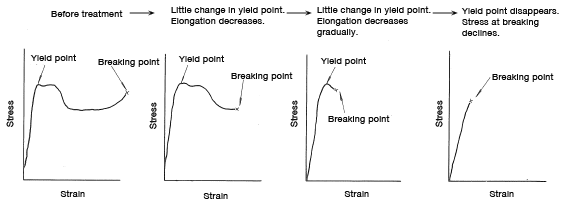
Figure 6: Change in the stress-strain curve resulting from thermal degradation
We can conclude that the change in elongation allows us to determine the extent of degradation. Figures 7, 8 and 9 show the change in elongation, tensile strength and impact strength in CM1021 and CM1026 resulting from exposure to high temperatures. Figures 10, 11 and 12 show the change in elongation, tensile strength and impact strength in CM3001N and CM3006 resulting from exposure to high temperatures. Clearly you can see higher temperatures and longer durations lead to greater declines in elongation and tensile strength.
Figure 7: Thermal degradation test (Tensile strength)
Figure 8: Thermal degradation test
(Tensile-breaking elongation)Figure 9: Thermal degradation test (Izod-impact strength)
Figure 10: Thermal degradation test
(Change in tensile strength)Figure 11: Thermal degradation test
(Change in tensile-breaking elongation)Figure 12: Thermal degradation test
(Change in Izod impact strength)
Based on this data, Figure 13 plots the temperature and time where elongation and tensile strength have decreased 50%.
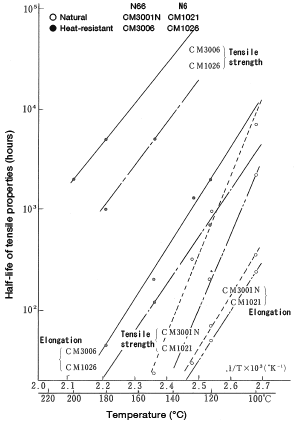
Figure 13: Thermal resistance (Half-life of tensile properties)
This is referred to as an Arrhenius plot, which facilitates estimating the relationship between temperature and lifetime. The same expressed in a formula would look like this:
Figure 13 shows a stark difference between CM1026 and CM3006 on the one hand and CM1021 and CM3001N on the other.
Table 2 shows the impact strength results from a tensile-impact strength test. Figures 14, 15 and 16 compare these results with a foreign competitor’s heat-resistant grade product.
Figure 14: Thermal degradation properties
(tensile strength, 180°C)Figure 15: Thermal degradation properties
(tensile impact, 150°C)Figure 16: Thermal degradation properties
(tensile impact, 120°C)
Conditions | Tensile- impact strength(kg·cm/cm2) | ||
---|---|---|---|
CM3006 | CM3006(Black) | Foreign competitor A’s Heat-resistant grade |
|
Before treatment | 331 | 318 | 257 |
180°C 2 days 5 days 10 days |
567 420 116 |
560 400 113 |
485 412 125 |
150°C 2 days 5 days 10 days |
545 330 221 |
455 320 215 |
401 388 226 |
120°C 2 days 5 days 10 days |
456 460 449 |
391 427 444 |
359 321 402 |
(Notes)
1) Test: ASTM D1822 1/8"t L type
2) Measured at 23°C, RH65%
3) 150°C and 120°C tests still underway.
Ⅱ. Heat cycling properties
Nylon is used frequently in environments where temperatures fluctuate from high to low and low to high. For example, nylon used in engine compartment components is exposed to a repetitive cycling of temperatures as high as 120°C (when the engine is running) to as cold as -30°C to -40°C (when left outside in the bitter cold). To anticipate how a material will perform under such a severe environment, heat cycle tests are performed. The test specimen is left in 120°C air for one hour, then immediately exposed to a -40°C environment. The results of these heat cycle tests are shown in Table 3.
Even after 70 cycles, both CM1026 and CM3006 retained at least 90% of their tensile-breaking strength. CM1026 retained 80% of its elongation and CM3006 retained 60%. CM1026 and CM3006 both retained at least 80% of their Izod-impact strength.
Unit | CM1026 | CM3006 | |
---|---|---|---|
Before treatment Tensile-breaking strength Elongation Izod-impact strength |
kg/cm2 % kg·cm/cm |
727 231 4.9 |
818 97 4.1 |
10 cycles Tensile-breaking strength Elongation Izod-impact strength |
kg/cm2 % kg·cm/cm |
718 185 4.7 |
888 90 3.9 |
10 cycles Tensile-breaking strength Elongation Izod-impact strength |
kg/cm2 % kg·cm/cm |
739 189 4.4 |
822 72 3.6 |
10 cycles Tensile-breaking strength Elongation Izod-impact strength |
kg/cm2 % kg·cm/cm |
748 178 4.3 |
809 63 3.6 |
10 cycles Tensile-breaking strength Elongation Izod-impact strength |
kg/cm2 % kg·cm/cm |
692 182 4.3 |
783 58 3.7 |
10 cycles Tensile-breaking strength Elongation Izod-impact strength |
kg/cm2 % kg·cm/cm |
679 163 4.0 |
742 55 3.5 |
(Notes)
1) Conditions 120°C 1hr- -40°C 1hr
2) Test specimen: ASTM D638 Type I (3-mm thickness), n = 10
3) Measurement conditions: 23°C RH65%
Ⅲ. Electrical properties
Demand is growing for heat-resistant nylon in materials and components used in electronics equipment. In these applications, the relationship between electrical properties and temperature, as well as any change in electrical properties when exposed to high temperatures for extended periods of time, are important factors to consider.
Compared to standard nylons, CM1026 and CM3006 experience little change in electrical properties when exposed to high temperatures.
Figures show the change in volume resistivity and dielectric tangent when exposed to 150°C or 120°C for extended durations of time, compared to standard nylon grades.
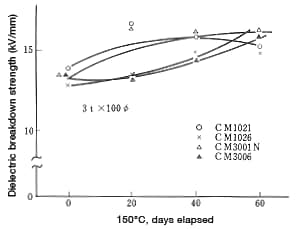
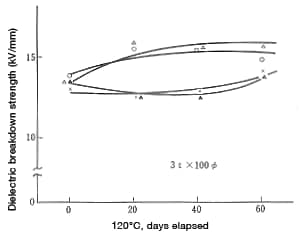
Figure 17
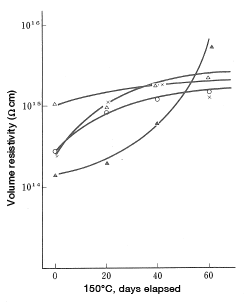

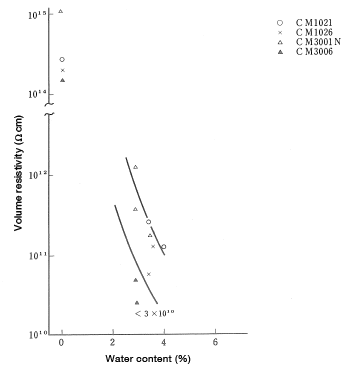
Figure 18
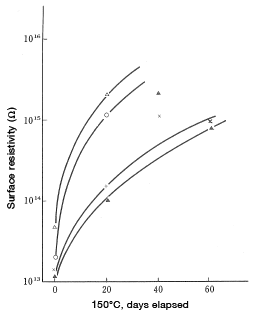

Figure 19
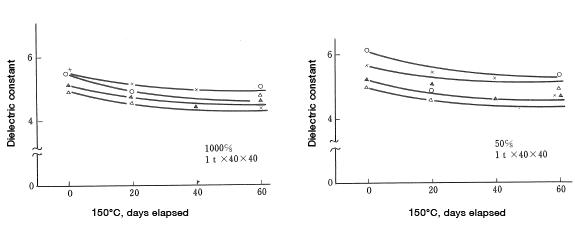
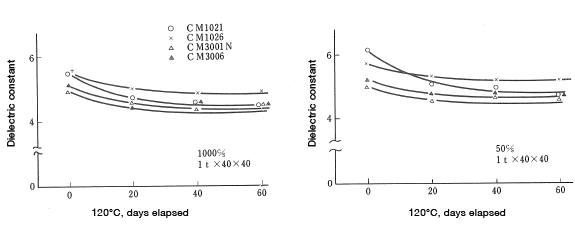
Figure 20
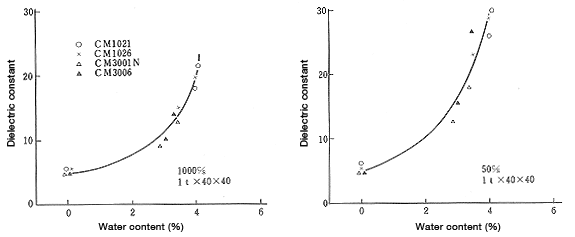
Figure 21
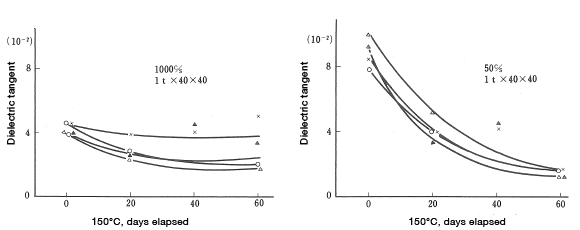
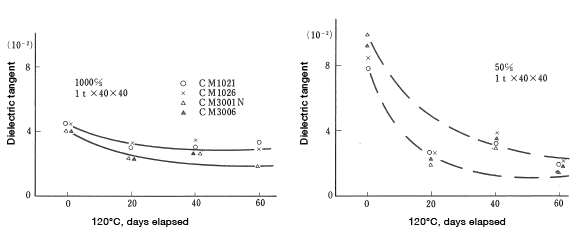
Figure 22
Ⅳ. Resistance to oil
In recent years, more and more automotive components are taking advantage of nylon’s superior resistance to oil. CM1026 and CM3006 are the ideal materials to use in high-temperature environments such as automotive engine compartments, where components come in direct contact with gasoline, brake oil or gear oil. Examples of some applications include fuel strainers, oil reserve tanks, canisters, fuel pipes and more.
Table 4 shows the change in properties of CM3006 when immersed in regular or high-octane, commercially available gasoline for three months at room temperature to demonstrate resistance to gasoline. Izod-impact strength and Rockwell hardness remained mostly unchanged, tensile-yield strength declined only slightly and elongation grew. This could be attributable to toluene or other aromatic hydrocarbons contained in the gasoline.
Immersion duration (months) |
Tensile-breaking strength kg/cm2 |
Elongation (%) |
Izod-impact strength kg·cm/cm |
Rockwell hardness R scale |
---|---|---|---|---|
0 1 2 3 |
895 831 849 849 |
95 85 125 150 |
4.5 4.3 4.5 4.7 |
121 122 122 122 |
Immersion duration (months) |
Tensile-breaking strength kg/cm2 |
Elongation (%) |
Izod-impact strength kg·cm/cm |
Rockwell hardness R scale |
---|---|---|---|---|
0 1 2 3 |
895 828 827 827 |
95 75 160 140 |
4.5 4.6 4.9 4.7 |
121 122 121 121 |
(Notes)
1) Plans call for the immersion test to continue for two years at room temperature
2) Test conditions: 23°C RH65%
Tensile: ASTM D638 n = 5
Impact: ASTM D256 n = 10
Hardness: ASTM D785 n = 10
Table 5 shows the results of changes in weight and properties after 300 or 600 hours immersed in 120°C synthetic gasoline (isooctane/toluene = 70/30Vol%). These results are illustrated in Figures 23-26.
Material and category | Treatment time(hrs) | ||
---|---|---|---|
0 | 302 | 600 | |
CM3006 Weight change % Tensile-yield strength kg/cm2 Tensile-breaking strength Elongation % Tensile-impact strength kg·cm/cm2 |
- 814 622 98 317 |
+0.56 828 612 53 377 |
+0.87 676 514 66 370 |
CM3006 (Black) Weight change % Tensile-yield strength kg/cm2 Tensile-breaking strength Elongation % Tensile-impact strength kg·cm/cm2 |
- 805 666 99 311 |
+0.58 815 587 61 398 |
+0.93 661 481 67 380 |
Foreign competitor A’s heat-resistant grade BLACK Weight change % Tensile-yield strength kg/cm2 Tensile-breaking strength Elongation % Tensile-impact strength kg·cm/cm2 |
- 808 588 37 327 |
+0.49 815 617 41 397 |
+0.77 675 518 38 375 |
(Notes)
1) Gasoline: isooctane/toluene = 70/30(vol%)
2) Temperature: 120±5°C
3) Test
Tensile: ASTM D638 Type13mm n = 5
Tensile impact: ASTM D1822 1/16" L TYPE n = 10
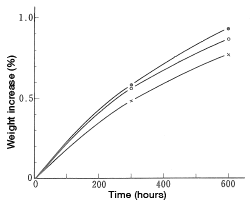
Figure 23
Resistance to hot gasoline
(Weight increase (%))
Gasoline: isooctane/toluene = 70/30 (vol%)
Temperature: ±5°C
Sample: Tensile test specimen (ASTM D638 Type1 3 mm)
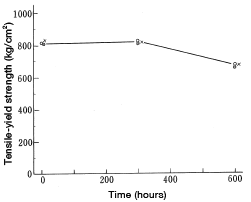
Figure 24:
Resistance to hot gasoline
(Tensile-yield strength)
Gasoline: isooctane/toluene = 70/30 (vol%)
Temperature: 120±5°C
Sample: ASTM D638 Type1 3mm
○CM3006
●CM3006 (Black)
× Foreign competitor A’s heat-resistant grade
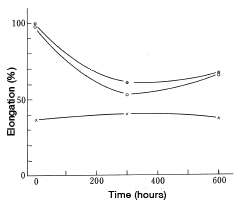
Figure 25
Resistance to hot gasoline
(Elongation)
Gasoline: isooctane/toluene = 70/30 (vol%)
Temperature: 120±5°C
Sample: ASTM D638 Type1 3mm
○CM3006
●CM3006 (Black)
× Foreign competitor A’s heat-resistant grade
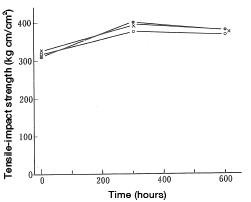
Figure 26:
Resistance to hot gasoline
(Tensile-impact strength)
Gasoline: isooctane/toluene = 70/30 (vol%)
Temperature: 120±5°C
Sample: ASTM D1822 1/16" L TYPE
○CM3006
●CM3006 (Black)
× Foreign competitor A’s heat-resistant grade
Next, to investigate the effects of exposure to gear oil, our nylon products were immersed in 80°C or 100°C gear oil continuously for 90 days. The measurement results of tensile properties and impact strength are shown in Figures 28 and 29. No property changed significantly, confirming that our nylons are largely unaffected by the test conditions.
As shown in Figures 30 and 31, exposure to brake fluid leads to greater elongation and impact strength and reduced tensile-yield strength.
Figure 27: Resistance to gear oil (Elongation)
Figure 28: Resistance to gear oil
(tensile-breaking strength, impact strength)
Figure 29: Resistance to brake fluid (elongation)
Figure 30: Resistance to brake fluid (elongation)