- HOME
- Technical Information
- SIVERAS™ LCP Resin
- Characteristic (2)
Characteristic (2)
Low warpage
Compared to other engineering plastics, LCP resin has (1) good dimensional stability and (2) lower distortion (attributable to its excellent flowability, which makes it possible to use a lower injection pressure), which helps prevent warpage and twisting.
However, there has been a developing need for a grade of LCP resin that meets more stringent requirements for low warpage. Warpage occurs in two ways.
Ⅰ. Warpage after molding
- Material grade with low anisotropy
- Grade with excellent flowability
Category | Filler-reinforced | Non-reinforced | |||
---|---|---|---|---|---|
L304G35 | L304G35H | L304M35 | LCP | ||
Type of filler | GF | 〇 | 〇 | 〇 | |
Filler | 〇 | ||||
Mold shrinkage (%) | MD direction | 0.06 | 0.10 | 0.18 | −0.15 |
TD direction | 0.50 | 0.69 | 0.32 | 1.55 | |
Anisotropy | TD/MD | 8.3 | 6.9 | 1.8 | −10.3 |
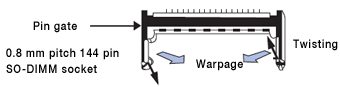
Molded product: Notebook PC memory
socket Non-reinforced
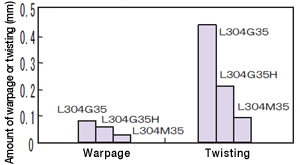
A material with greater anisotropy tends to exhibit more warpage. A greater difference in mold shrinkage in the machine direction versus the transverse direction tends to indicate greater anisotropy in the material. In an LCP resin, there is already anisotropy in the polymer itself. (This feature represents the greatest difference between LCP and other engineering plastics.) Therefore, the anisotropy in an LCP resin is greatest when the LCP is non-reinforced (no filling material). Adding such filling materials as glass fibers (GF) disrupts the polymer orientation and relaxes anisotropy. Moreover, a filling material with low anisotropy is preferable to that with high anisotropy. That is to say, granular or tabular filler with low anisotropy is preferred over a fiber-like filling material such as GF molded product: Notebook PC memory socket Non-reinforced
Ⅱ. Warpage after reflow soldering
LCP resin is used in SMT connectors mounted on IC circuit boards.
When the connector is mounted, there is a step where heat is applied to melt soldering (reflow step). Warpage occurs as a result of this step.
Warpage after reflow is caused by the relaxation of residual stress in the molded product. That relaxation is caused by exposure to the heat used in the reflow step.
SIVERAS™ exhibits better flowability than competitor LCPs. That makes it possible to use lower peak pressure during injection-molding, which in turn results in less residual stress and a lower probability of warpage resulting from the reflow step.
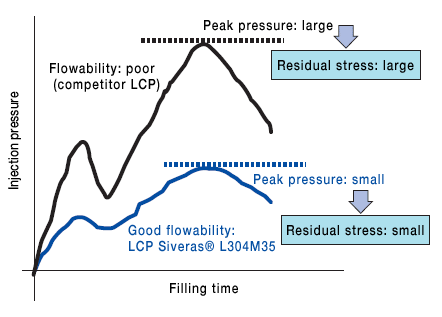
Examples of pressure waves during injection-molding of LCP