- HOME
- Technical Information
- CAE Analysis, Analysis and Processing Technologies
- Processing Technologies
- Blow Molding Technologies
Molding Technology for Hollow Parts: 3D Suction Blow Molding
The molding technology used to form hollow resin parts depends on the shape, with various mass production technologies such as extrusion molding, blow molding, and the joining of injection-molded parts all applied and widely used in the industry. Toray possesses materials suitable for 3D suction blow molding, and also provides support for this relatively new molding technology.
Ⅰ. Features of 3D Suction Blow Molding
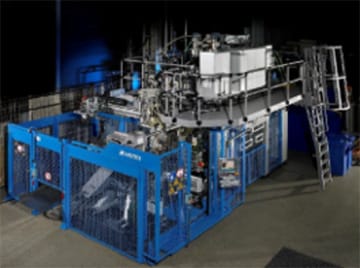
General-purpose blow-molding technologies, such as those used for plastic bottles, are constrained to mostly symmetrical shapes because the parison follows gravity when blown up in the mold. In contrast, 3D suction blow molding, as the name suggests, blows up parisons introduced into the mold cavity under suction to create a 3D shape, enabling parts with long and complex shapes to be formed in one shot. In addition, a control mechanism called Radius Wall Thickness Control (RWTC) facilitates even thickness and enables the difference between the inside and outside circumference to be adjusted, irrespective of changes in thickness or increases and decreases in wall thickness for each part. Toray has partnered with Kautex Maschinenbau, a leading German machinery manufacturer, to promote the fusion of material and molding technologies.
Ⅱ. Compatible Resins
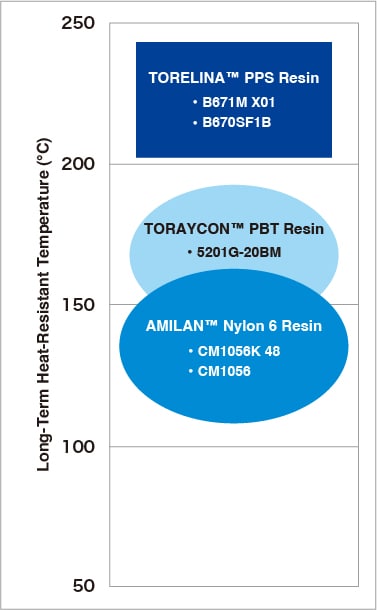
In general, blow molding resins require an optimized melt viscosity and retention stability in order to be compatible with the process. In addition, the RWTC control mechanism mentioned above is useful for 3D suction blow molding, and an optimized melt viscosity is desirable for each shear rate optimized for parison shape retention.
With this in mind, Toray has selected matrix polymers to develop and provide optimal materials for a range of environmental temperatures. The figure shows our approach to grade deployment. In particular, PPS resin has high heat resistance that provides high part performance, but the low melt viscosity means it is generally difficult to optimize for 3D suction blow molding. However, Toray's proprietary technology has succeeded in developing ultra-flexible PPS that can handle various processing methods.
Ⅲ. 3D Suction Blow CAE
3D suction blow molding requires the parison to pass through the cavity during the suction process without being destroyed, while determining factors such as wall thickness after blow up requires repeated mold creation and investigation into molding conditions, which takes a lot of time and effort.
To solve such problems, Toray Engineering D Solutions Co., Ltd. is developing and commercializing analysis technology using 3D TIMON™ CAE software for the first time ever.
In addition to materials, we offer a total solution that covers shape investigation, mold design and molding conditions.
Analysis technology with 3D TIMON™ CAE software