- HOME
- Technical Information
- TORAYCON™ PBT Resin
- Chemical properties
Chemical properties
Chemical properties
Ⅰ. Chemical resistance
Table 11 shows the chemical resistance of TORAYCON™ non-reinforced grade (1401X06) after immersion for six months in different chemicals at room temperature. The study looked for changes in appearance, weight, dimensions and tensile strength. Table 12 provides qualitative comparisons with other engineering plastics.
TORAYCON™ is resistant to a broad range of chemicals. It exhibits resistance to inorganic chemicals, with the exception of concentrated sulfuric acid, concentrated hydrochloric acid and strong alkali. TORAYCON™ exhibits favorable resistance to organic chemicals—alcohols, ethers, aliphatic hydrocarbon and polymeric esters do not attack TORAYCON™. In particular, TORAYCON™ exhibits favorable resistance to gasoline and engine oils, making it a superb choice for automotive applications.
However, exposure to acetone, benzene or phenol causes swelling, as is the case with most other engineering plastics. For that reason, exercise caution in determining fitness for use.
Also note that ortho-chlorophenol and solvents combining ethane tetrachloride with phenol will cause TORAYCON™ to dissolve.
Chemical | Weight change (%) | Dimensional change (%) | Tensile strength retention (%) | Appearance |
---|---|---|---|---|
Pure water | +0.3 | 0 | 99 | No change |
3% sulfuric acid | +0.3 | +0.1 | 97 | 〃 |
30% sulfuric acid | +0.2 | 0 | 99 | 〃 |
10% nitric acid | +0.3 | 0 | 99 | 〃 |
35% hydrochloric acid | +0.5 | 0 | - | Some loss of glossiness |
1% sodium hydroxide | +0.3 | +0.1 | 92 | 〃 |
10% sodium hydroxide | -0.1 | +0.1 | 91 | 〃 |
10% sodium chloride solution | +0.3 | 0 | 95 | No change |
40% chromic anhydride | -0.2 | 0 | 100 | 〃 |
Methanol | +1.3 | +0.4 | 85 | 〃 |
Ethanol | +0.3 | 0 | 97 | 〃 |
Acetone | +3.9 | +1.0 | 72 | 〃 |
Methyl ethyl ketone | +2.9 | +0.5 | 77 | 〃 |
Ethyl acetate | +2.7 | +0.4 | 80 | 〃 |
Heptane | +0.1 | 0 | 100 | 〃 |
Cyclohexane | 0 | 0 | 100 | 〃 |
Glacial acetic acid | +2.2 | +0.2 | 78 | 〃 |
Benzene | +3.0 | +0.5 | 70 | 〃 |
Toluene | +2.1 | +0.3 | 85 | 〃 |
5% phenol | +9.6 | +1.7 | 60 | Yellowish discoloration and swelling |
Carbon tetrachloride | +0.6 | 0 | 100 | No change |
Dichloroethane | +16.8 | +4.7 | 50 | Swelling |
Dioctyl phthalate | -0.2 | 0 | 100 | No change |
Dimethyl formamide | +2.7 | +0.3 | 80 | 〃 |
1% surfactant | +0.2 | +0.1 | 99 | 〃 |
Gasoline | +0.2 | +0.1 | 99 | 〃 |
Olive oil | 0 | 0 | 100 | 〃 |
Kerosene | 0 | 0 | 100 | 〃 |
Heavy oil | 0 | 0 | 100 | 〃 |
Machine oil | +0.1 | +0.1 | 100 | 〃 |
Type of plastic | PBT resin | Modified PPO | Polyacetal | Polyamide | Polycar- bonate |
||
---|---|---|---|---|---|---|---|
(homopo- lymer) |
(copo- lymer) |
(6) | (66) | ||||
Water absorption (%)* | 0.08 | 0.07 | 0.25 | 0.22 | 1.32-1.90 | 1.5 | 0.15 |
Mild acid | Safe | Mostly safe | Partly dangerous | Mostly safe | Safe | ||
Strong acid | Partly dangerous | Mostly safe | Dangerous | Dangerous | Partly dangerous | ||
Mild alkali | Mostly safe | Mostly safe | Partly dangerous | Mostly safe | Mostly safe | Mostly safe | |
Strong alkali | Dangerous | Mostly safe | Dangerous | Mostly safe | Mostly safe | Dangerous | |
Active gas | Mostly safe | Immersed in chlorine gas | Immersed in chlorine gas | Mostly safe | |||
Oil | Safe | Mostly safe | Mostly safe | Mostly safe | Partly dangerous | ||
Acetone | Mostly safe | Mostly safe | Mostly safe | Mostly safe | Dangerous | ||
Benzene | Mostly safe | Dangerous | Mostly safe | Safe | Dangerous | ||
Carbon tetra chloride | Safe | Dangerous | Safe | Mostly safe | Dangerous | ||
Alcohol | Safe | Mostly safe | Safe | Partly dangerous | Partly dangerous | ||
Ester | Mostly safe | Dangerous | Mostly safe | Safe | Dangerous | ||
Gasoline | Safe | Partly dangerous | Safe | Safe | Dangerous | ||
Solvent | Ortho chloro phenol | Carbon tetra chloride | Special | Phenol, formic acid, metacresol | Methylene chloride, chloroform |
*ASTM D570 (1/8" plate thickness, for 24 hours) All under no load.
White paper
Toray's TORAYCON™ PBT Resin Designed for Safety and ReliabilityVastly improved alkali-resistance through water-repellent technology and hydrolysis-resistance technology
Since the products involved in the various advanced driver-assistance systems (ADAS) that support this evolution are made to help drivers with things like peripheral monitoring, they are being used in increasingly harsh environments. In this whitepaper, we will look at how we've increased the alkali-resistance—a characteristic weakness of conventional PBT resin—to produce a new, vastly improved, highly durable material.
Ⅱ. Stress cracking resistance
Table 13 shows the number of days before cracks appear on the surface of a dumbbell-shaped test specimen left to sit after deforming as shown in Figure 22.
TORAYCON™ non-reinforced grade (1401X06) indicates greater resistance to stress cracking than polyacetal.
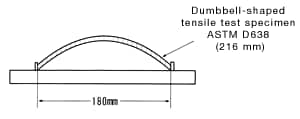
Figure 22: Stress cracking resistance test (test specimen thickness: 3.2mm)
Test conditions | Number of days until cracks appear | |
---|---|---|
1401X06 | Polyacetal | |
In air (145-150°C) | 14-16 | 2-3 |
Engine oil (85-90°C) | 28 or more | 6 |
Ⅲ. Resistance to hot water
Figures 23 and 24 show the resistance to hot water of TORAYCON™ non-reinforced grade (1401X06) and glass-fiber reinforced grade (1101G-30). Similar to polycarbonate resin, the TORAYCON™ molecule contains an ester bond, which causes the molecule to hydrolyze after immersion in hot water for extended durations of time. The hydrolysis reduces the degree of polymerization, which in turn diminishes strength. So exercise caution before using TORAYCON™ in applications involving such conditions. That said, TORAYCON™ can withstand warm water of about 60°C for extended durations of time.
As shown in the section on heat-cycle resistance, TORAYCON™ can withstand exposure to hot water, if intermittent or short-lived.
Figure 23: Resistance to hot water of 1401X06
Figure 24: Resistance to hot water of 1101G-30