- HOME
- Technical Information
- TORELINA™ PPS Resin
- Various Properties
- Thermal Properties
- DSC Analysis of TORELINA™
DSC Analysis of TORELINA™
The differential scanning calorimeter (DSC) offers a technique that is indispensable to the analysis of resin materials. By determining the thermal flow rate difference between a sample cell and a reference cell, a range of thermal properties can be determined, such as the melting point (Tm) of the organic materials, the glass transition temperature (Tg), and the crystallization rate of injection molded products.
Ⅰ. Thermal Properties (Melting Point, Crystallization Temperature, and Glass Transition Temperature)
When a TORELINA™ injection molded product is heated at a rate of 20℃/min, endothermic energy appears gradually near 250℃ due to crystal melting, and then peaks near 278℃. (Fig. 6.1) This peak temperature is the melting point of the PPS resin, and indicates that the resin has changed from a solid state to a molten state. If the resin is cooled from the molten state at a constant rate, an exothermic peak (cooling crystallization temperature) appears due to crystallization. This cooling crystallization temperature is used as a rough guide for the solidification rate. The smaller the difference between the melting point and the cooling crystallization temperature (supercooling temperature difference), the higher the solidification rate of the material.
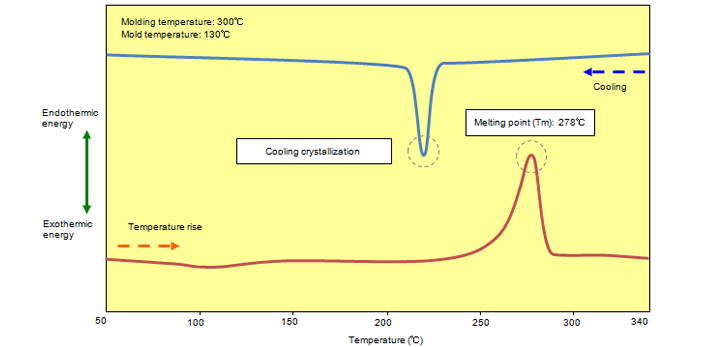
Fig. 6.1 DSC chart (A900)
If PPS resin is molded at a mold temperature equal to or less than the glass transition temperature (80℃ or less), a stair-like peak appears (it may not appear in some cases), showing the glass transition temperature (Tg), near 90℃ to 95℃ in the heating process, and then an exothermic peak (cold crystallization temperature) appears due to crystallization near 120℃ to 130℃. (Fig. 6.2) If this cold crystallization temperature is clearly observed, this indicates that the crystallization of the molded product has not progressed, causing decreases in the chemical resistance, dimensional fluctuations in a high-temperature environment, and so on. For this reason, if molding is performed with a low-temperature mold for purposes such as flash suppression, annealing (thermal) treatment must be performed according to the usage environment of the product to stabilize the crystal state. (The exothermic peak at the cold crystallization temperature disappears with annealing.)
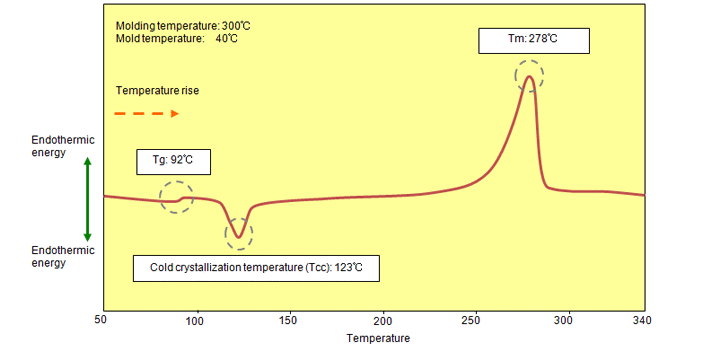
Fig. 6.2 DSC chart of a low-temperature molded product (A900)
Ⅱ. Specific Heat
Fig. 6.3 Temperature dependence of specific heat (cooling method)
The specific heat is the amount of heat (J) required to raise the temperature of 1 kg of a substance by 1 K. The higher the specific heat of a material, the harder it is to heat and cool the material. Specific heat is a property inherent to every substance, so a linear PPS and cross-linked PPS do not differ greatly in their specific heat values, but they are influenced by the specific heat inherent to the reinforcement. The specific heat tends to increase with temperature. (Fig. 6.3) For example, the specific heat determined with the heating method is used in thermal conductivity measurement (unsteady method), and the specific heat determined with the cooling method is used in flow analysis (CAE).