- HOME
- Technical Information
- TORELINA™ PPS Resin
- Injection Molding
- Injection Molding
- Cylinder Temperature
Cylinder Temperature
The relationship between the cylinder and resin temperatures varies with the type of molding machine, the screw rotation speed during plasticization, and other factors. For a general molding machine, the resin temperature will be about 10℃ to 15℃ higher than that of the cylinder when the screw rotation speed during plasticization is 100 rpm.
For the injection molding of TORELINA™, an optimum cylinder temperature is 300℃ to 320℃ for unreinforced PPS resins and 310℃ to 340℃ for reinforced PPS resins. For elastomer improvement, reinforced PPS resins, such as TORELINA™ A575W20 and A673M, if the molding temperature is too high, the mechanical properties will be adversely affected due to the thermal decomposition of the elastomers and mold contamination, so make sure that the cylinder temperature does not exceed 340℃. If the cylinder temperature setting is lower than 300℃, this may result in insufficient melting of the resin, possibly causing the quality of the molded product to be adversely affected. It is important to set the temperature to within an appropriate range.
The results of examining the relationship between the cylinder temperature and the mechanical properties for the main grades of TORELINA™ are shown in Figs. 3.6 to 3.12. A cylinder temperature rise of 10℃ results in an increase in fluidity of about 9%, but over a temperature range of 310℃ to 340℃, changing the cylinder temperature has little influence on the mold shrinkage, mechanical properties (including welds), and so on.
Fig. 3.6 Cylinder temperature in relation to mold shrinkage (machine direction)
Fig. 3.7 Cylinder temperature in relation to mold shrinkage (transverse direction)
- ※Molded product shape: 80 mm × 80 mm × 3 mm t square sheet, molding conditions (settings): mold temperature: 130℃, injection pressure: lower limit molding pressure + 10 MPa, injection speed: 100 mm/s
Fig. 3.8 Cylinder temperature in relation to tensile strength
Fig. 3.9 Cylinder temperature in relation to tensile elongation
- ※Tensile test method: Conforms to ISO 527-1 and -2.
Fig. 3.10 Cylinder temperature in relation to flexural strength
Fig. 3.11 Cylinder temperature in relation to flexural modulus
- ※ Flexural test method: Conforms to ISO 178.
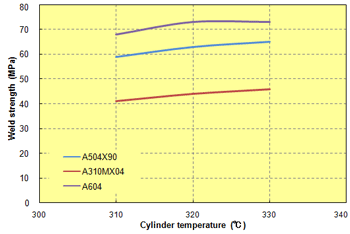
Weld molding conditions (settings)
* Molding temperature: 330 (℃)* Mold temperature: 130 (℃)
* Injection pressure: Lower limit molding pressure + 10 (MPa)
* Injection speed: 100 (mm/s)
* Tensile test method: Conforms to ISO 527-1 and -2.
For small- to medium-size injection molding machines, there are four to five sections for which the temperature must be set, as shown in Fig. 3.13. It is common practice to increase the preset temperature as you go from the hopper-side rear section to the nozzle. Note the following, as well as the characteristics of the molding machine being used, when setting the temperatures.
In the cylinder portion for which temperature control is possible, the rear section is a material supply zone. In general, to feed pellets toward the front section, the screw groove must be deep. Predried pellets have a high hardness because crystallization has progressed. If the temperature of the rear section is too low, non-molten, hard pellets may promote the wear of the screw or the cylinder. If the temperature of the rear section is too high, the pellets will melt and cling to the screw and so on, so that they cannot be fed sufficiently, worsening the biting properties of the pellets. It is, therefore, preferable to set a high temperature to the extent that the biting properties of the pellets do not worsen. A temperature of between 280℃ and 310℃ is appropriate.
The intermediate section is a compression zone for promoting the melting of the material and increasing the melt density. The screw groove is shallower than that of the rear section. In the intermediate section, the resin generates heat due to the shearing action of the screw. Thus, set this section to a temperature equivalent to or about 10℃ lower than that of the front section.
The front section is a measurement zone for purposes such as kneading, ensuring the uniformity of the melt density, and maintaining the temperature of the resin. Adjust the temperature within a range of 310℃ to 330℃, by checking the quality of the molded product, including the appearance. If the temperature of this portion is too low, problems will occur, such as there being insufficient fluidity and decreases in the gloss of the molded product (mold transferability). If, on the other hand, the temperature of this portion is too high, problems attributable to increases in the amount of gas are more likely to occur (such as burns, silver streaks, deposits adhering to the mold, and a worsened molding environment). If there is no alternative other than to increase the temperature of this portion to 340℃ or greater due to there being insufficient fluidity, appropriate measures must be implemented, such as modifying the mold (by, for example, increasing the wall thickness, increasing the size of the gate or the runner, and improving the gas venting) or changing the resin to a high flow grade.
The nozzle temperature has a major influence on the dimensional accuracy of the molded product, so it must be set carefully. More specifically, the temperature to be set differs depending on whether nozzle touch molding or automatic iteration molding is to be performed. For nozzle touch molding, heat is conducted to the mold, so the temperature should be equivalent to or about 10℃ higher than that of the front section. If the temperature is too low, this will cause problems such as nozzle clogging and the inclusion of cold slugs in the molded product. If the temperature is too high, the problem of cobwebbing will occur. The same applies to automatic iteration molding, but in this case the amount of heat conducted to the mold is small, so set a temperature lower than that of the front section temperature. If a closed nozzle is not used or if the nozzle is not a suck back type, drooling (resin leakage) from the nozzle is likely to occur. The nozzle temperature should be low but about 10℃ to 15℃ higher than the temperature at which nozzle solidification occurs.
Fig. 3.13 Sections of an injection molding machine