- HOME
- Technical Information
- TORELINA™ PPS Resin
- Injection Molding
- Injection Molding
- Miscellaneous
Miscellaneous
Ⅰ. Cushion amount
After setting the cylinder temperature and the mold temperature, it is important to set an appropriate cushion amount. There are special molding methods that use a cushion amount of 0. However, with such methods, sufficient holding pressure cannot be applied to the molded product, so that defects, such as sink marks, insufficient fusion of welds, and mold shrinkage fluctuations, are more likely to occur. An appropriate cushion amount is about 5 to 10 mm. If the cushion amount is too large, the time of residence in the molding machine will increase, which may cause material deterioration. Check the cushion amount regularly, and if the cushion amount has become small over time, the backflow preventing ring, the screw, or the cylinder may have worn. Inspect and replace them if necessary.
Ⅱ. Injection pressure
The injection pressure (primary) must be set to a level that is high enough to allow the injection speed to be controlled at will. As a rough guide, the injection pressure (primary pressure) should be 1.2 to 1.5 times the molding lower limit filling pressure. If the injection pressure is too low, the injection speed cannot be controlled sufficiently, causing the quality of the molded product to be unstable, which may result in appearance defects, short shots, and other such defects. The latest injection molding machines often include types that enable you to check changes (waveforms) in the injection speed and injection pressure on their screens. The response differs from one model to another. Make appropriate settings according to the molding machine being used.
Ⅲ. Holding pressure
The injection process, in which about 95% to 98% of the mold cavity is filled at the primary injection pressure, is followed by the holding pressure process. In the holding pressure process in crystalline resin molding, volume shrinkage (sink marks) and voids, the two main causes of which are thermal expansion and crystallization, are suppressed. If the holding pressure is too low, this may result in appearance defects, as well as dimensional defects due to sink marks appearing on the molded product. If it is too high, this may result in an increase in the residual strain and flash and, in certain cases, may result in the breakage of the mold due to overpacking. Thus, in actual molding, adjust the holding pressure gradually while checking the balance between any sink marks and flash. Until the gate solidifies (gate seal), the holding pressure will have an influence on the molded product. Setting a holding pressure time equal to or greater than the gate seal time does not have an effect on the suppression of sink marks. If setting a sufficiently long holding pressure time does not eliminate the sink marks on the surface of the product, it may be that the effect of the holding pressure is not obtained due to the gate seal. In such a case, it is necessary to set a higher molding temperature or a higher mold temperature and review the mold design (including the gate size and the placement of sprues and runners).
Ⅳ. Injection speed
The injection speed influences various aspects of the molded product, such as the fluidity during molding, the appearance of the molded product, and the properties associated with the orientation of the reinforcement (mechanical properties, anisotropy, and mold shrinkage). Molten resin that is in the fluid state in the mold rapidly decreases in fluidity due to heat exchange with the mold (increases in the melt viscosity). It can, therefore, be said that it is preferable for the injection speed to be set to medium or high and thus fill the cavity promptly. If a relatively large gas vent is provided or if the mold has good gas venting because of, for example, vacuuming, it is possible to obtain molded products excellent in surface appearance and in the fusibility of welds by molding with a filling time of 1 s or less. If the fusibility of the welds is substandard due to a gas venting failure, gas may be trapped and adiabatically compressed air may burn the resin flow end. In such a case, it may be better to decrease the injection speed.
The injection speed indicates the rate of advance of the screw or the plunger. Even if the injection speed is constant, the flow rate of the resin that actually flows in the cavity varies with the wall thickness of the molded product. To achieve a stable level of product quality, it is preferable for the molten resin in the cavity to flow at a uniform rate. For those molded products that have large wall thickness differences, in particular, it is possible to eliminate defects in some cases by adjusting the injection speed for each stage.
Ⅴ. Screw rotation speed
The screw rotation speed is an important element that influences the plasticization capacity. Usually, set the speed so that measurement is completed within the cooling time. Most grades of TORELINA™ contain glass fiber, and, if the screw rotation speed is too high, this may lead to the mechanical properties being adversely affected, as well as wear to the machine, due to the glass fiber being damaged. Usually, set the speed to about 50 to 120 rpm. Usually, the measurement time is shortened according to the screw rotation speed. Depending on the screw structure and the cylinder specifications (such as L/D and thermal capacity), the screw rotation speed also influences the biting properties, so check that the measurement time for each shot is stable.
Ⅵ. Screw back pressure
In the measurement process for an in-line injection molding machine, the screw retracts while rotating, so that an amount of molten resin equal to the volume is fed to the nozzle side. The back pressure is the force applied in the opposite direction in an attempt to prevent the screw from retracting. This has the effect of expelling air between the pellets or any moisture and volatile matter in a pellet that are and increasing the plasticization density by increasing the kneadability. If the screw back pressure is too low, air and other gases may remain in the molten resin, resulting in burns, silver streaks, other flaws in the surface texture, insufficient fusibility of the welds, and so on. If the screw back pressure is too high, this will increase the material plasticization time, and may lead to drooling. In addition, this will increase the damage to the glass fiber and so on, possibly resulting in poorer mechanical properties, as well as problems attributable to remarkable increases in the resin temperature due to shear heating. As a rough guide, therefore, set the back pressure to about 0.2 to 5 MPa for grades that contain glass fiber and to 5 to 10 MPa for grades that do not, such as unreinforced PPS resins.
Ⅶ. Injection time
The injection time consists of the filling time and the holding pressure time. It refers to the time required for plasticized resin to fill the cavity and assume the shape of the molded product. The injection time differs with the product shape and size, molding temperature, mold temperature, and other factors. For a molding machine with a clamping force of less than 100 t, the time consists of a filling time of up to about 2 to 3 seconds and the holding pressure time until gate seal. Considering the internal stress, viscosity increases due to solidification in the mold, and so on, the filling time should preferably be short (less than 1 second). In principle, it should be as short as possible, provided that this does not present problems with gas venting and appearance. Adjust the holding pressure time according to the gate seal time to prevent voids and sink marks, as described in (3) Holding pressure.
Ⅷ. Suck back
Suck back is a function for forcibly retracting the screw after the completion of measurement. This is effective means of preventing resin leakage (drooling) from the nozzle. If, however, the suck back amount is too great, air is inhaled from the nozzle tip, which may cause burns to the molded product and silver streaks. As a rough guide, set it to 3 to 5 m.
Ⅸ. Material purge
After TORELINA™ molding, a purge should be performed sufficiently first, and then the material should be replaced with commercially available detergent, high-viscosity polyethylene, etc. (for example, an MI value of 0.05 g/10 min). Depending on the grade, TORELINA™ may increase in viscosity if it resides in the molding machine for an extended period. Thus, if molding is ever paused, perform a purge in the same way. The following tendency is observed: Even if TORELINA™ resides for a short time of about 10 minutes at a cylinder temperature of 320℃, its fluidity increases slightly, causing the weight of the molded product to increase. In this test example, eight shots are required to eliminate the influence of the residing resin remaining in the cylinder. Depending on the size of the molded product and the cylinder size of the molding machine, the number of shots required to reach the normal state will differ. (Fig. 3.25)
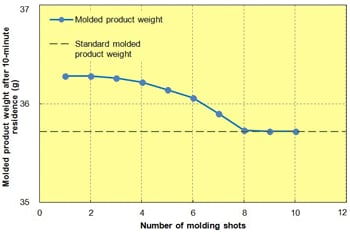
relation to product weight
Shape: 80 × 80 × t 3 mm square sheet
Injection molding machine: Toshiba IS75E
Molding temperature: 320℃
Mold temperature: 130℃
Molding cycle: Injection/cooling = 10/15 seconds