- HOME
- Technical Information
- TOYOLAC™ ABS Resin
- Molding conditions
Molding conditions
TOYOLAC™ possesses superb flowability and heat stability and is easily molded using ordinary injection molding equipment. Standard predrying and molding conditions are provided below.
Ⅰ. Pre-drying
To obtain the desired ABS resin-molded product, preheat under appropriate conditions. Pellet water content should be no more than 0.1% (preferably no more than 0.05%)
to obtain the desired molded product. When using a box-type hot-air dryer, dry at 80°C for 3-6 hours or 90°C for 2-3 hours. Figure 1 illustrates the drying curve for TOYOLAC™.
Use higher drying temperatures than you would for standard grades to properly dry heat-resistant grade TOYOLAC™ or TOYOLACPAREL™.
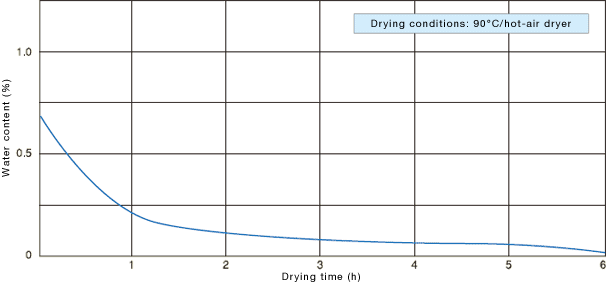
Figure 1: TOYOLAC™ drying curve
Ⅱ. Molding conditions
To set molding conditions, consider such factors as the molding equipment being used, the size and shape of the molded product and the mold structure.
Ⅲ. Cylinder temperature
A temperature setting in the range of 210-240°C is generally the most practical.
Figure 3 shows the relationship between the cylinder temperature setting and the spiral flow length of TOYOLAC™.
Ⅳ. Mold temperature
To obtain the desired surface finish and reduce residual stress, use a mold temperature in the range of 40-80°C, preferably as high within that range as possible. That said, using a higher mold temperature tends to lengthen molding cycle time, so use the mold temperature setting most appropriate for the individual product that is to be molded.
Category | Drying temperature/hours |
Cylinder temperature setting |
Mold temperature |
---|---|---|---|
Standard grade | 80-90°C/3-5hrs | 220-240°C | 40-80°C |
Abrasion-resistant high-sliding grade | |||
High-gloss grade | |||
Painting/Plating grade | |||
Detergent-resistant grade | |||
Transparent grade | 80-90°C/3-5hrs | 210-230°C | 40-70°C |
Scratch-resistant grade | |||
Heat-resistant grade | 90-100°C/3-5hrs | 240-260°C | 40-80°C |
Flame-retardant grade | 80-90°C/3-5hrs | 190-230°C (884:-210°C) |
40-80°C |
Durable anti-static grade | 85-95°C/3-5hrs | 210-240°C | 30-80°C |
Fiber-reinforced grade | 90-100°C/3-5hrs | 240-260°C (885VG20:-250°C) |
60-90°C |
ABS//PC alloy | 100-110°C/4-8hrs | 240-270°C | 50-80°C |
ABS//PBT alloy | 90-110°C/3-8hrs (VX10G20:-120°C) |
240-260°C | 60-80°C |
ABS//PA6 alloy | No drying required if molding immediately after opening. If stored after opening, dry at 80-90°C for 3-8 hrs to remove moisture. |
240-260°C | 60-80°C |
Ⅴ. Injection pressure
To reduce warpage and shrinkage, use sufficient injection pressure and holding time. Observe the appearance of the molded product to optimize injection pressure conditions.
Ⅵ. Mold design
An ordinary resin mold can be used to form TOYOLAC™. Using a slightly larger gate and runner than what is ordinarily used to mold polyethylene or polypropylene resins produces even better results. Otherwise, no special measures need be taken as far as the mold is concerned. If the mold has a rough surface or an undercut structure, use a parting agent. Otherwise, a parting agent is unnecessary because TOYOLAC™ is relatively less prone to stick to the mold during molding. Mold shrinkage varies depending on molding conditions and product shape. Ordinarily, TOYOLAC™ mold shrinkage falls within the range of 0.4 to 0.6%. A draft angle within the range of 1/200 to 1/100 is preferred. See Table 2 for data on TOYOLAC™ mold shrinkage.