- HOME
- Technical Information
- TOYOLAC™ ABS Resin
- Secondary processing
Secondary processing
Ⅰ. Machining
TOYOLAC™ can be easily cut, lathed, punched or filed. However, ABS resin does not conduct heat as well as metal, so take measures to minimize heat accumulation. Also, avoid using excessive contact pressure when cutting or otherwise machining. Generally speaking, cutting tools with sharp nose angles provide preferred machining results because they achieve deeper penetration and higher cut speeds and allow for easier removal of shavings.
Ⅱ. Welding
Ordinary ultrasonic or hot jet welding can be used favorably to weld TOYOLAC™. Generally, a welded section will have 80% the strength of ordinary TOYOLAC™.
Ⅲ. Adhesion
Select the adhesive depending on what material is being adhered to TOYOLAC™. A variety of adhesives can be used to adhere two TOYOLAC™ surfaces together. Solvents such as MEK and acetone achieve particularly fast adhesion. Adding to these solvents a solution comprising 10-20% dissolved TOYOLAC™ will produce even better results. Use a polyurethane or epoxy adhesive to adhere TOYOLAC™ to metal. To adhere TOYOLAC™ to nylon, use an adhesive solution comprising a mixture of ten parts formic acid, ten parts acetone, one part nylon resin and one part TOYOLAC™.
Ⅳ. Painting
Painting TOYOLAC™ can enhance appearance (e.g., multicolor finish, matte finish) and improve resin performance (e.g., a harder surface, weather resistance).
That said, ABS resin has inherent limitations in terms of resistance to solvents and heat. That limits the painting materials that can be used with TOYOLAC™ compared to what can be used with metal. TOYOLAC™ has a deflection temperature under load that is about 85-100°C. Do not bake above this temperature.
Painting materials that can be used with TOYOLAC™ include nitrocellulose lacquers, acryl lacquers, low-temperature-fired melamine alkyds, polyvinyl chlorides and two-pack urethanes.
Ⅴ. Grade for plating applications
TOYOLAC™ exhibits excellent stability under a broad range of etching conditions when subject to etching treatments aimed at forming a base layer for adhesion to a plating film. TOYOLAC™ achieves favorable adhesion even after short etching times and resists overetching during longer etching treatments. TOYOLAC™ is designed to achieve excellent adhesion with plating materials. See Table 7 for TOYOLAC™ 125 adhesion data. TOYOLAC™ 125 flows well and maintains heat stability, enabling a broad range of molding possibilities and providing a molded product that can be plated with little residual strain. Molding deficiencies often cause plating defects. Preventing defects such as silver streaking is critical to a plating process, so make sure the material has been sufficiently dried before processing. Select molding conditions to minimize residual strain—use a higher resin temperature setting, a higher mold temperature setting (50-60°C) and a slower injection speed.
Etching type | Cylinder temperature setting(°C) |
Etching time (min) |
Adhesion strength (Peeling strength) (N/cm) |
---|---|---|---|
High chromic acid type CrO3 430g/L H2SO4 220mL/L S.G. 1.49 Temperature 65°C |
220 | 3 5 10 |
8.3 13.2 14.4 |
260 | 3 5 10 |
8.8 14.7 15.7 |
|
High sulfuric acid type H2SO4(98%) 740mL/L H3PO4(89%) 320mL/L K2Cr2O7 40g S.G. 1.58 Temperature 65°C |
220 | 10 20 |
9.6 12.0 |
260 | 10 20 |
12.7 14.9 |
Ⅵ. Vacuum deposition
TOYOLAC™ can be used successfully in vacuum deposition and sputtering applications. The following is a typical vacuum deposition process.
- Pretreatment: Remove oil, fat and parting agents from the molded product surface.
- Undercoat: Apply a coating to strengthen adhesion with metal and achieve a smoother resulting surface.
- Vacuum deposition: Deposit metals such as aluminum on the molded product under a high vacuum state (not to exceed 10-3 mmHg) using a vacuum deposition apparatus.
- Topcoat: Apply a topcoat to enhance the deposited metal surface's resistance to oxidation and abrasion.
Ⅶ. Vacuum forming
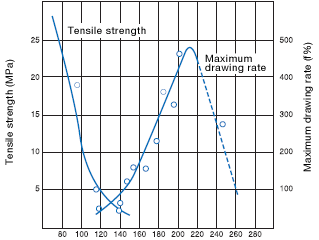
Figure 7: Relationship between temperature
and TOYOLAC™ 600 sheet maximum
drawing rate (sheet thickness: 1.5 mm)
TOYOLAC™ sheets can be vacuum-formed into products featuring complex shapes requiring deep drawing.
- Temperature dependence of TOYOLAC™ sheets
See Figure 7 for measures of suitability for vacuum forming—namely, the relationship between temperature and maximum drawing rate and the relationship between temperature and tensile strength. (Maximum drawing amount was measured using a form pack sheet tester.)
TOYOLAC™ 600 sheets exhibit high drawing rates. The rate of decline in tensile strength at high temperature also indicates superb suitability for vacuum forming. - Vacuum forming conditions
When vacuum-forming ABS resin sheets, select the optimal temperature based on the vacuum forming equipment type, sheet thickness and formed product shape. TOYOLAC™ 600 can be formed within the range of 120-200°C. Cooling time will vary depending on the mold material, mold temperature and sheet thickness. Cool until the sheet temperature falls to about 70°C. - Mold design
Standard wood, resin, metal or plaster is suitable as a mold material when vacuum-molding TOYOLAC™ 600. Avoid sharp edges and use a gradual radius where possible. Although these factors vary slightly depending on the shape or forming conditions, shrinkage is generally 0.5-0.7%, and a draft angle of 0.5° to 1° on the female mold and 3° to 4° on the male mold is appropriate. A mold temperature of 70-80°C is optimal.
Category | Engineering unit | Conversion coefficient | SI unit | |
---|---|---|---|---|
To SI unit | To engineering unit | |||
Tensile strength | kg/cm2 | 9.8/10-2 | 10.2 | MPa |
Flexural strength | kg/cm2 | 9.8/10-2 | 10.2 | MPa |
Flexural modulus | kg/cm2 | 9.8/10-2 | 10.2 | MPa |
Izod impact strength | kg/cm/cm | 9.8 | 1.02×10-1 | J/m |