- HOME
- 技术信息
- AMILAN™ 尼龙树脂
- 射出成型
- 模具
模具
模具的构造和部件名称
脱模方式
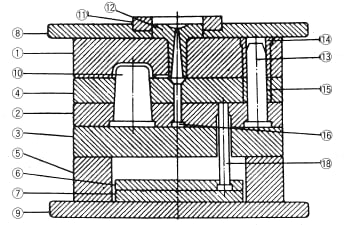
顶销方式
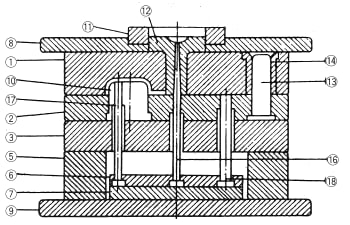
图3.1注塑成型用模具
- 固定侧模板(JISB5106)
- 动托模板(JISB5106)
- 受力板(JISB5106)
- 脱模板(JISB5106)
- 间隔块
- 上顶出板
- 下顶出板
- 固定配置板
- 动托模板
- 阳模
- 定位环(JISI∋5111)
- 注道衬套(JISB5112)
- 导销(JISB5107)
- 导销衬套(JISB5110)
- 导销衬套(JISB5110)
- 注道残料固定销
- 顶销(JISB5108)
- 回销(JISB5109)
控制模具温度的重要性
为了提高成型品的性能,有效化成型,使用模具温度调节器和筒式加热器等来控制模具温度是十分必要的。
尼龙因是结晶性高分子物,模具温度是影响结晶度的最大的因素。
Ⅰ. 功能特性
表3.1中显示了因模具温度产生的功能性变化。当提高成型品的刚性,并增加的拉伸和弯曲强度时,可以通过控制模具温度的提升来提高结晶度得以实现。然而,成型品会变得稍有脆性。如若与需求的性能相反,就降低模具温度。
Ⅱ. 成型品的外观
为了增加透明度,将保持较低的模具温度。为了提高表面光泽度,可以将模具温度控制在30℃以下,或是保持温度在80℃以上。
梨纹(也称坑洼)尽管可以通过模具表面完全的研磨而使其光滑,虽说是减少了表面产生无数凹凸点的不良成型品,但是要解决这个问题,还是需要将模具温度处于30℃以下的低温或是持续保持在80℃以上的高温
性质 | 単位 | 模具温度(℃) | 尼龙 | ||
---|---|---|---|---|---|
6 | 66 | 610 | |||
拉伸屈服强度 | MPa | 20 80 |
75~80 85 |
750 80 |
50 55 |
拉伸断裂伸长率 | % | 20 80 |
200< 150 |
150 100 |
200< 200< |
弯曲强度 | MPa | 20 80 |
95 120 |
100 115 |
72 95 |
弯曲模量 | GPa | 20 80 |
2.8 3.0 |
2.7 2.7 |
1.8 2.0 |
Ⅲ. 成型收缩率与密度
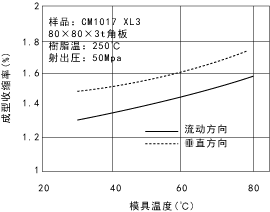
图3.2. 因模具温度而引起的成型收缩率的变化
图3.2所示的正是由模具温度所引起的成形收缩率变化。模具温度是成型条件中,影响成型收缩率的最大因素。因此模具铣加工尺寸值的推算上,是由可达到成型状态的模具温度值来决定的并估算的。
因模具温度,密度的变化如图3.3所示。密度与结晶度达成一定比例,所以模具温度在40℃以下的话密度值低,在80℃以上的话,可见密度值高且稳定。那模具温度在50~70℃的范围时,仅模具的温度的变化就能使结晶温度发生巨大的转变,在这个温度转变范围内会造成成型品品质的不稳定,所以请尽可能的避免。
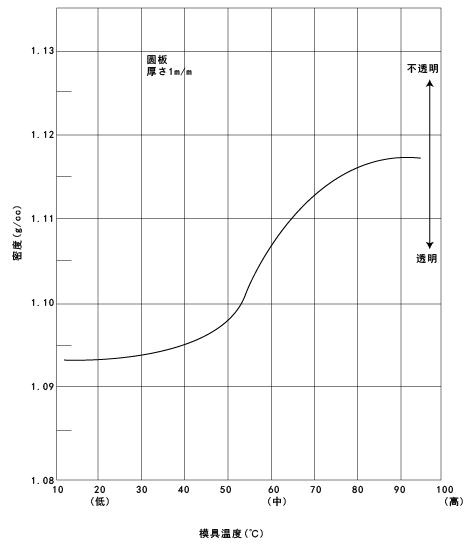
图3.3 成型后的密度和模具温度
Ⅲ. 成形性
熔融聚合物的流动性将会在后文描述,但成型时,模具的温度是越高越好。关于成型周期上,分别有降低模具温度,提升固化加速周期和提高模具温度,熔融聚合物易于填充加速成型周期这两种。无论采用哪种,都会因成型品形状,模具构造,成型品内压等不同而产生区别。
Ⅳ. 成型时模具温度的变化
模具可以被看做一种吸收熔融聚合物热量,并利用冷却水和模具表面进行放热的热交换机。
可稳定持久不变的模具温度,也就是将从熔融聚合物中吸收的热量和因冷却水等产生的放热互相抵消,采取两者平衡的稳定状态,这种持续恒温是存在的。调节温度,在模具中从成型开始到性质稳定这一期间需要少量时间的等待,但若不调节温度,那这段时间需要更长,且达到温度前的成型注出品皆是被作为不良品必须丢弃的。此期间的成型品尺寸不稳定,是无法得到稳定的良好的所期物性的。因此,为了杜绝浪费,模具温度的控制十分重要。
模具的预热上通常是使用煤气燃烧器和喷气燃烧器进行局部加热,但是请避免模具因热量发生变形现象。
Ⅴ. 防止冷却应变
因为不同成型产品部位的不均匀冷却,容易导致不均匀的应力收缩,所以模具的设计就非常重要了。当然,因为因分子流向和成型压力所引起的应变现象并不为零,可以冷却时应变现象还是可以通过适度调节模具的温度来避免的。
在实际的模具设计时,滑动型芯,顶销,模芯嵌件,还有Be-Cu的铸件阴模板等,都有为了均匀冷却阴模内部温度而无法如同事先计算好的配置冷却孔的情况出现。在这种情况下,需要将快速冷却的部分通过温水加热,打开阀门均衡全部的冷却(收缩)速度。进一步的,这种局部加热还会提升熔融聚合物在阴模中的流动提高成形性。
模具温度控制设计
Ⅰ. 设计上的原则
顶销冷却孔优先:是设计的原则。
一般情况下,阴模因为形状复杂,设计完顶销后,就会在模具构造上所许可的范围内配置冷却孔,通过适当的放入制冷剂和调节温度来冷却,诸如这种设计是相当多的。但是重要的是从模具温度的控制这个出发点来着手模具的设计。
Ⅱ. 模具传热面积
在控制模具温度的基础上必要的模具冷却孔的传热面积通过以下的公式来说明。(忽略对外放热,模板,喷嘴接触的传热影响)
此处,
A: 热传导表面积(m2)
W: 成型品重量(kg)
N: 每单位时间上内注出的数量(1/h)
Cp: 树脂的比热(1.4~2.1)(J/g・℃)
C: 冷却水的比热(4.2)(J/g・℃)
t1: 树脂温度(℃)
t0: 取出成型品时的温度(℃)
ΔT: 模具与冷却水的平均温度差(℃)
h: 冷却孔内膜的传热系数(90~140)(W/m2・℃)
λ: 冷却水的热传导率(600~700)(W/m・℃)
d: 管直径(m)
u: 冷却水流速(m/s)
ρ: 冷却水密度(1000)(kg/m3)
μ: 冷却水粘度(0.001)(Pa・S)
一定程度假定以上数据所得出的物性图如3.4所示。从中测出的传热面积可作为最小值作为参照。
问题案例1
1假设注出重量70g ,注出次数60次/时,在此情况下,计算成型时的冷却孔传热面积。
<解答>
图3.4的物性图中将对应W=70g的点与对应N=60shot/hr的点相连接,A线上的交叉点上的A=400cm2就是所要求的传热面积值。
问题案例2
模具的冷却孔粗设定为12.7φ,那上诉问题中的冷却孔长度可计算出。模具的大小为30cm厚的方材,那需要开几个直空最为合适?
<解答>
冷却口的长度至少需要在100cm以上。
而且,单一边,30CM的模具上就需要3.3个以上直孔,那也就是需要开4个孔。
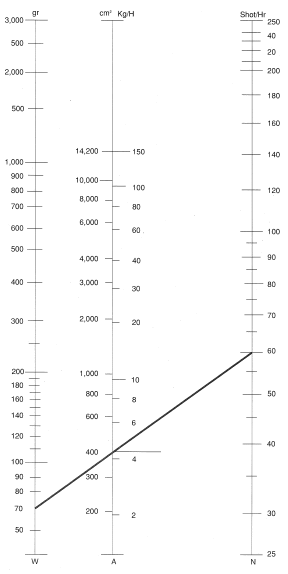
图3.4.模具所需的热传导表面积
Ⅲ. 冷却孔的分布和大小
就理论而言,熔融聚合物带入阴模内热焓的分布或重量的分布是相似的。
在冷却分布是否合理的相关测试中,需要检查缩短所需冷却时间并成型后的硬化状态。
冷却孔的粗细在9.5~12.7mmφ最为适当,且阴模表面到冷却孔需要有25~40mm的间隔。如若间隔太近,冷却将会不均匀产生成型品冷却品变形,如若太远,直到冷却成型需要一定时间。
冷却水的流向与主注道相对,从远的阴模开始向进出开始进入冷却,如若在同一个阴模内,冷却水与聚合物的流向相反进行回流是最理想的。
图3.5 角型阳模的冷却(1)
图3.6 角型阳模的冷却(2)
图3.7. 流式冷却水道
图3.8. 设置了防护板的冷却孔
图3.9. 粗圆形阳模的冷却
图3.10. 细核的冷却(喷流式)
图3.11. 棱状冷却水道
图3.12 设有探测柱的阳模
图3.13. 并列冷却阳模
图3.14. 阴模单侧的冷却方法
图3.15. 装有绝缘板的注口衬套
图3.16. 使用喷射阀的模具的冷却
图3.17 注口衬套的冷却
排气
为了优化成型性而一味地使用高速注塑,还提高模具精度,因为树脂的流向会将空气封闭在模具内从而变成成型不良的原因。因此,在成型品不飞边的范围内,或者即使有飞边,也可在快要成型之际进行简单的排气。
排气的方法详见图3.18至3.21。
因排气不良会引发的成型不良,燃爆所造成的坑洼(高温高压会造成压缩气体燃烧现象),熔接不良,吸入空气产生的气泡这些问题。
图3.18. 利用顶销排气
图3.19.4 连续排气单个成型
图3.20. 装有连续排气的模具
图3.21. 利用顶销排气
脱模斜度
脱模斜度会因为成型品形状的复杂程度、阴模的深度、成型品的薄厚等都会发生变化,通常需要1/2~1°。
顶出方法
为了顺利完成脱模,务必需要充分地研究顶销位置。此要点就是为了避免成型品脱模时的变形和翘曲,控制顶销位置的平衡点。方法有将顶销印迹要放置在成型品上不突出的位置,销顶表面需要充分研磨后可以易于脱模等。喷嘴的顶销形状可参照图3.22。
顶出成型品的方法中,关于顶销顶出方法详见于图3.23,脱模板顶出方法像详见于图3.24,套筒式顶出方法详见图3.25。请根据成型品的形状进行选择。
图3.22注口顶销和拉出方法法
A:Z型 B:倒锥形 C:沟槽 D:圆锥
1.可移动模板 2.流道 3.注口衬套 4. 固定模板 5.注孔图3.23 顶销法
1.顶出板(上) 2.顶销 3.可移动模板 4.固定模装板 5.注口 6.弹簧
7.动托模板 8.阳模 9.成型品 10.模孔 11.注口衬套 12.注口顶销
13.顶出护板 14.固定模板 15.受力板 16.回销 17.顶出板(下)
图3.24 顶出脱模板法
1.顶出板(下) 2.稳固螺栓 3.固定模装置版 4.弹簧 5.可移动模装置板
6.受力板 7.导销 8.成型品 9.注口衬套 10固定模板
11.脱模板 12.回销 13.可移动模板 14.模孔 15阳模
16.注口顶销 17.顶出板 18.顶出护板图3.25套筒式顶出法
1.套筒式顶出 2.模孔 3.可移动模装置板 4.动托模板 5.阳模 6.可移动模板
7.成型品 8.固定模板 9.注口 10.回销 11.前进可移动模板 12.冷却管道
13.模孔 14.顶出板(上) 15.顶出板(下)