- HOME
- 技术信息
- TORELINA™ PPS树脂
- Various Properties
- 二次加工
- 其他(螺丝固定与自攻)
其他(螺丝固定与自攻)
Ⅰ. 螺丝(螺栓)固定
为了将塑料成型品固定到金属主体上或同树脂连接在一起,可使用以下所示的螺丝固定方法:通过事先在成型品上准备的孔,用螺帽和螺栓固定;将螺丝拧进成型品的内螺纹并上紧;以及将自攻螺丝打入到树脂凸起处的孔内,而不需要使用内螺纹。一般来说,在强度、蠕变性(应力释放)等方面,树脂不及金属。因此,可能会出现由于过度拧紧导致开裂、螺纹破裂和松开等问题。
(1) 螺丝各部分的名称
图10.35给出了螺丝各个部分的名称。
(a) 双螺纹,右旋,平行外螺纹
(b) 平行内螺纹和平行外螺纹的轴截面图
图 10.35 螺丝各部分的名称
- * 参考文献:日本机械学会编《机械工学手册》之A:基础篇和B:应用篇 新版第9次发行
(2) 螺栓紧固过程中产生的应力
图 10.36 螺栓紧固过程中的轴向力
如图10.36所示,将两个成型品通过使用螺帽和螺栓固定在一起的时,存在于螺栓轴上的张力F和压缩力F相互抵消(无外力作用),这个力被称为预应力(或轴向力),表征初始紧固力。
如果螺栓是外螺纹,螺帽是内螺纹,使用扭矩法紧固在一起,紧固扭矩T和轴向力F之间的关系见公式10.1。
公式10.1右边的第1项 是作用在螺丝面上的摩擦扭矩,第2项
是作用在螺栓轴上的扭矩,第3项
是作用在螺帽座面上的摩擦扭矩。在不使用润滑剂的情况下,采用扭矩法紧固,由于在第1项和第3项的摩擦,大部分扭矩能(大约90%或以上)将会转化为热能。为了增加紧固扭矩的有效性,必须降低摩擦系数。
如果将公式10.1应用到普通公制螺丝(α = 30°),可得到公式10.2。
(使用润滑剂情况下 ≒0.15),图10.37给出了紧固扭矩与轴向力的关系,表10.12列出了公制螺丝各自的公称直径(外径)。如果轴向力过大,从成型品紧固处传来,可能会产生放射状开裂。这是因为虽然压缩应力作用在成型品表面,但是螺栓孔会像插入的金属一样试图变形横向扩大,以至于成型品内部发生拉伸应力。如果轴向力超过了容许应力,可能导致破裂发生。
图 10.37 公制螺丝的扭矩与轴向力的关系
表 10.12 公制螺丝直径
Screw nominal designation | M2 | M3 | M4 | M5 | M8 | M10 | M12 | M14 | M16 | |
---|---|---|---|---|---|---|---|---|---|---|
Nominal diameter d | mm | 2 | 3 | 4 | 5 | 8 | 10 | 12 | 14 | 16 |
Pitch P | mm | 0.40 | 0.50 | 0.70 | 0.80 | 1.25 | 1.50 | 1.75 | 2.00 | 2.00 |
Effective diameter dp | mm | 1.74 | 2.68 | 3.54 | 4.48 | 7.15 | 9.03 | 10.86 | 12.70 | 14.70 |
Root diameter dr | mm | 1.57 | 2.46 | 3.24 | 4.13 | 6.65 | 8.38 | 10.11 | 11.84 | 13.84 |
公式10.3是松开螺帽的扭矩,因为公式10.1右边的第2项 是作用在螺栓上的扭矩,但在公式10.3中是反方向的作用力。从公式10.3看出,松开扭矩是紧固扭矩的80%。
Ⅱ. 自攻
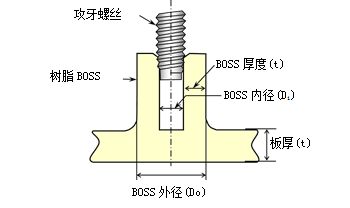
使用螺丝固定树脂部分还可能用到攻牙方法(图10.38),预先在成型品的树脂BOSS打个孔,然后将自攻螺丝打入孔内进行紧固。
1 自攻螺丝
对于TORELINA™的攻牙,可以使用A~C类攻牙螺丝中的任一种。但是需要注意的是,如果螺距少于0.8mm,螺丝有可能会刮破BOSS预留孔,导致紧固力不足。
2 树脂BOSS的设计
必须将树脂BOSS的设计与攻牙螺丝的形状相匹配,以便能完全利用螺丝的强度。
(1) ① 预留孔的直径与插入形状
合适的直径应该等于或略小于所使用的攻牙螺丝的有效直径,略大于内螺纹的外径,大约是螺丝公称直径的85%。公式10.4列出了螺纹咬合百分比应该在50%~70%之间。如果预留孔的直径太大,内螺纹的树脂BOSS将会在螺丝紧固时破裂,反之,如果直径过小,树脂BOSS或螺丝可能发生破裂。另外,预留孔的插入口必须尽可能设计成盘形的或弧形的,方便引入预留孔内(深度:约1mm,直径:螺纹外径+0.1~0.2mm),防止在紧固时插入孔周围区域被破坏。
(2) BOSS的外径
标准直径是螺丝公称直径的2.5倍。如果BOSS的外径太小,肉厚太薄,可能会导致短射、熔接痕以及其他成型不良问题。即使这些问题不发生,BOSS也可能会出现横向或纵向的断裂。
(3) 旋紧深度
标准深度是螺丝公称直径的2.5倍。如果旋紧深度太小,树脂的内螺纹会被破坏。
(4) 板厚
板厚必须与螺丝的公称直径差不多。如果强度不足,要确保R角半径在0.3~0.5之间,和采取合适的手段,例如加强筋。但是如果板厚太大,可能发生制品内部缩痕。
3 BOSS外径的设计
当螺丝紧固BOSS的时候,所产生的应力将会使在BOSS出现横向和纵向的断裂。
(1)纵向断裂
图 10.39 BOSS外径与发生应力的关系
例如,假设螺丝的公称直径是M3,= 2.57 mm,
=7.5 mm,M3型号螺丝自身的断裂强度是2450 N,求得发生应力与BOSS外径之间的关系。表10.12给出了所使用的M3型号螺丝的螺距和有效直径(
:= 0.5 (mm),
= 2.68 (mm)。如果知道了紧固扭矩,可根据公式10.2或图10.32算出轴向力。在这种情况下, 假设螺丝的断裂强度是最大轴向力F,将数据代入公式10.5和10.6,可以得出图10.39。从图中可以看出,当发生应力低于100MPa时,BOSS外径
应大于7mm。
(2)横向断裂
通过公式10.7可计算横向断裂。
在测定纵向断裂的同等条件下,求得BOSS外径与横向发生应力之间的关系,如图10.39所示。从图中可以看出,当发生应力低于100MPa时,BOSS外径 应大于6mm。
4 预留孔深度或螺丝有效长度的设计
如果旋紧深度 过小,可能会引起BOSS的内螺纹破裂。可根据公式10.8得出发生在内螺纹根部的剪切应力
。
图 10.40 螺丝的有效长度与拔出强度的关系
例如,假设螺丝的公称直径是M3, k=0.82,=65 MPa,图10.40显示了
和螺丝拔出强度的关系。如果有效深度达到或超过6mm,螺丝的拔出强度就超过了螺丝的断裂强度(2450 N)。
一个C型攻牙是在下部有3到4个波峰的锥形,而且这个锥形部分对于连接没有很大的作用。所以在估计BOSS预留孔的深度时,有必要考虑到这部分。
5 BOSS板厚的设计
可根据公式10.9计算出BOSS的板厚 。
例如,假设螺丝的公称直径是M3, 为2450 N(螺丝的断裂强度),
为65 MPa,
为7.5 mm,
为 2.57 mm,可计算得出 等于2.45 mm。因此,当使用公称直径为M3的螺丝时,BOSS的板厚最好在2.35mm以上。
6 试验例1
在TORELINA™ A504X90和A310MX04的6mmt的角板上,钻一个4.5mm直径的预留孔,使用3.92 N・m 的扭矩用一个M6自攻进行紧固,然后进行热循环处理(200℃ x 30 min ⇔ 室温 x 30 min x 10 个循环)。之后测定松开扭矩,A504X90和A310MX04的松开扭矩都下降到0.98 N・m (扭矩保持率:25%)。在热循环处理过程中,反复交替使用高温和室温处理,导致在螺丝与树脂BOSS接触面上线性膨胀出现了差异,从而造成松开扭矩下降。如果处理温度比成型时的模温高,由于重结晶化的影响,会引起尺寸发生变化。退火处理是有效的改善手段,但是由于线性膨胀差异是尺寸变化的主要因素,所以退火处理的抑制效果是有限的。鉴于此,当松开扭矩的保持率要求较高时,应该设计成金属插入的方式。
7 试验例2
如果在TORELINA™ A504X90和A310MX04的3mmt的角板上,钻一个1.8mm直径的预留孔(螺纹咬合率:35%),使用0.4 N・m 的紧固扭矩用一个M2自攻(d: 1.8 mm, dr: 1.46 mm)进行紧固,树脂BOSS的内螺纹就会破裂。如果将预留孔的直径设置在1.5~1.6mm之间(螺纹咬合率:73%~92%),将螺丝反复的拧紧、松开,摩擦扭矩就变得非常大,螺丝头的十字凹槽就会破裂。
使用M2.5型的自攻螺丝(d: 2.48 mm, dr: 1.90 mm),在紧固扭矩为0.5N/m 的条件下,拧入直径为2.1mm的预留孔内(螺纹咬合率:66%),反复的将螺丝拧紧、松开10次后,测定松开扭矩。可以得到松开扭矩在0.35~0.4 N/m 之间(保持率:70%~80%),而且未观察到螺纹和其他部分破裂。
Ⅲ. 压入装配
图 10.41 压入装配
在树脂成型品装配的工程中、有很多是通过压入装配的方式将金属轴等固定在成型品内(图10.41)。压入装配包含压入装配时由装配余量(公式10.10)产生的模量和轴与成型品之间的摩擦。压入装配所需的力在本质上应与拔出所需的力是相等的,但是在实际应用中,由于应力释放的影响,拔出力往往要小些。
1 容许应力
设计压入装配余量时,要求测定材料的容许应力 。容许应力等于基准强度除以安全率,如公式10.11所示。这是为了使材料在某段时间内(预设使用寿命)不发生破坏而设定的临界应力。如果导致制品破坏的主要因素是拉伸强度,那么基准强度是拉伸屈服强度或断裂强度。如果主要因素是疲劳性能,那么基准强度是抗疲劳强度。决定安全率的方法依限界条件而不同,例如:环境条件、制品形状(包括应力集中和熔接)和功能的重要性(安全性)。据推测,对于金属和其他部件,静态负荷下的安全率是3,动态负荷下的安全率在5~10之间。但对于热可塑性树脂,没有明确的指导数据,但其安全率应被设定在等于或略高于金属的安全率。
2 压入装配余量的设计
如果压入装配部分是一个BOSS,压入装配余量可根据公式10.12和10.13计算所得的容许应力而得出。
例如,测以下圆柱形成型品(外径 : 20 mm)的压入装配余量:TORELINA™ A504X90(拉伸断裂强度:190 MPa,杨氏模量:16,000 MPa,泊松比:0.36);A310MX04B(拉伸断裂强度:130 MPa,杨氏模量:25,000 MPa,泊松比:0.34);A900(拉伸断裂强度:80 MPa,杨氏模量:4300 MPa,泊松比:0.40)。如果将金属轴(外径:
: 10 mm)压入到以上制品中,制品上只有拉伸方向上的静态负荷,安全率为3。
◆计算TORELINA™ 压入装配余量示例
许用应力
根据公式 10.9,
代入公式10.13,
再代入公式10.10,
A504X90的内径为:
类似地,可以计算出A310MX04和A900 的内径:
A310MX04的内径为:
A900的内径为:
品名 |
临界压入装配余量 (%) |
---|---|
A504X90 | 0.72 |
A310MX04 | 0.31 |
A900 | 1.15 |
对于强化材含量高且弹性模量也较高的规格,在压入装配过程中变形的比例极限是很小的,所以压入装配余量也小。但在实际压入装配时,成型品的尺寸公差、图纸和工作环境的温度引起的线性膨胀,都可能影响压入装配的金属与成型品的内径产生波动。一旦压入装配余量太小,生产管理就会显得很困难。如图10.42所示,外径对压入装配余量的影响较小,但对材料的强度和模量影响很大。因此,压入装配余量很大程度上取决于安全率的取得方法,如图10.43所示。假设安全率为1,可将公式10.13转化成公式10.14,根据公式10.14可计算出TORELINA™各规格的临界压入装配余量率,数据见表10.13。因为PPS具有高刚性,其临界压入装配余量要低于其他塑料。如果压入装配余量超过临界值,BOSS可能会破裂和压弯。因此,要避免该值过大。
图 10.42 成型品外径与压入装配余量的关系(A504X90)
图10.43 安全率与压入装配余量的关系(A504X90)
3 加热压入装配
加热压入装配是将金属加热熔化成型品表面的树脂,同时进行压入装配的一种方法。这种方法适用于临界压入装配余量率较小的情况。加热的方法包括:加热压入装配(直接加热金属轴)、高频压入装配(使用高频波加热金属轴)和超声波压入装配(使用超声波产生的摩擦热加热金属轴)。在金属轴上压花纹或者凹槽设计能防止脱落,在这种情况下,熔融的树脂会流入到凹槽的部分,从而获得非常大的拔出强度。