- HOME
- Technical Information
- CAE Analysis, Analysis and Processing Technologies
- Analysis Technologies
- Instrument Analysis
- Instrument Analysis Case Study
Instrument Analysis Case Study
Visualizing the Bonded Layer: Analysis Instruments Reveal Changes Invisible to the Human Eye
Methods such as bonding and welding can be used to join things together. Bonds formed through these methods vary in strength, with some objects appearing to be bonded but peeling apart when lightly pulled, and others not coming apart even after large amounts of force are applied, with the base material breaking first. This case study was in response to a request to visualize not just the force when breaking bonds, but also the bond before breaking.
The mechanism of bonding can be described in many ways, but bonds are generally referred to as physical bonds, chemical bonds or mechanical bonds, with bond strength being based on one or a combination of these. This case study takes a closer look at how chemical bonds are visualized.
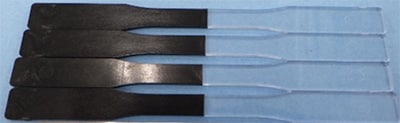
On the right is a sample of injection-welded black resin and transparent resin. Even if the bond layer, located at the point where the two resins meet, is observed with a microscope, it is not possible to observe any seeping of black resin into the transparent resin. In other words, the bond layer cannot be evaluated based on colors visible to the naked eye.
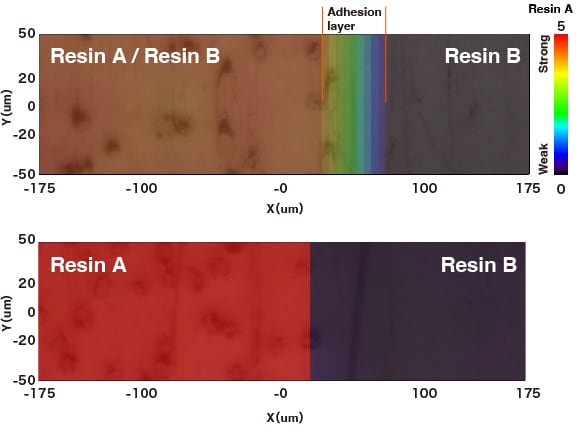
In this case study, we conducted an analytical evaluation using infrared spectroscopy, one of our instrument analysis technologies.
The graphs to the right show the structure of each resin and a comparison of their characteristic levels of infrared light absorption. The results shown in the top image are infrared spectroscopy results for an injection welded sample with a mixture of a black-colored resin (resin A) and transparent resin (resin B) on the left, and resin B on the right. A rainbow layer can be observed where the layers meet, which can be evaluated using the colors picked up through infrared spectroscopy. This reveals that resin A is seeping into resin B to form the bonded layer.
On the other hand, the bottom image shows an injection-welded solution of purely resin A on the left and resin B on the right. The location where the layers meet is clear, indicating that the chemical bond in the bonded layer has not been formed.
Download the White Paper
Toray resin technology increases the reliability of electronic device componentsDramatically Improved Bonding Is Achieved Between the PPS Resin and the Sealing Material
Electronic device parts require the use of epoxy resins and silicone resins as sealants for conductor materials. Sufficient bonding between the high-performance thermoplastic resin used for manufacturing the exterior of an electronic component and the resin used for sealing it is extremely important in ensuring the reliability of the component.
Simultaneous Pursuit of Heat Dissipation/Electromagnetic Wave Shielding/Airtightness and Weight ReductionProposal of Metal-Resin Joining Technology that will Contribute to the Production of New Products
While integrally molding metal and resin makes it possible to design products having both the heat dissipation and electromagnetic wave shielding characteristics of metal and the lightweight and easy processability characteristics of resin, ensuring airtightness is a major issue.This is a summary of a metal-resin joining technology designed to resolve this issue, and an introduction of use examples and anticipated future applications for this technology.