- HOME
- Technical Information
- TORELINA™ PPS Resin
- Various Properties
- Secondary Processing
- Chemical Joining
Chemical Joining
Chemical joining methods for molded products include a method with the use of adhesives and a method that melts the surfaces of the molded products with the likes of an organic solvent. TORELINA™ is highly crystalline and offers excellent chemical resistance, so the latter method, solvent joining, cannot be used. The only chemical joining method that can be used with TORELINA™ is that which uses adhesive. Although slightly different from joining, potting can also be classified as a type of chemical joining. This involves encapsulating an electronic circuit in a box-shaped molded product for purposes of insulation.
Ⅰ. Adhesive Joining
Because of its high crystallinity and poor wettability with adhesive, PPS resin is classified as a thermoplastic resin having low adhesion properties. Adhesive joining is that method whereby the respective functional groups of the adhesive and the thermoplastic resin react with each other to join together to obtain joint strength. For PPS resin, epoxy, cyanoacrylate, silicone, polyimide, and other adhesives are generally used. Regardless of the type of adhesive that is used, the joint strength will be lower than that which is possible with physical joining and screw fastening. If using TORELINA™ for structural members, therefore, give sufficient consideration to this beforehand.
Ⅱ. Evaluation method
In the adhesive joining evaluation shown in Fig. 10.2, a dumbbell-shape sample (ASTM No. 1, with no surface treatment) is cut in half, adhesive is applied so that the adhesion area is 0.5 cm2, and then curing is performed under appropriate conditions for that adhesive. The curing conditions differ with the type of adhesive. Follow the recommended conditions supplied by the adhesive manufacturer. The bonded test piece, for which the adhesive has fully cured, is left in a standard environment for at least 24 hours, and then the shear fracture load (N) is determined using a tensile tester. This is then converted into a joining stress (MPa), according to the area of the adhesive.
When the fracture surface is observed, it can be classified into one of patterns (1) to (3). An interface fracture occurs if the strength of the joint surface (interface between the base material and the adhesive) is the lowest, a cohesion fracture occurs if the strength of the adhesive itself is the lowest, and a base material fracture occurs if the strength of the surface layer of the base material is the lowest.
◆Classification of fracture modes
- (1) Interface fracture:
Fracture (peeling) occurs at the interface between the PPS resin and the adhesive. - (2) Cohesion fracture:
Fracture occurs in the adhesive. - (3) Base material fracture (alternating fracture):
The fracture surface is entirely on the base material side (PPS) or is partially on the base material side (PPS) and partially on the adhesive side.
Fig. 10.2 Test method for adhesive-based joining
Ⅲ. Silicone adhesion
Silicone adhesive is available in various types. It is largely classified according to three factors: (1) curing temperature (room-temperature curing or thermal curing), (2) whether a curing agent is required (one-pack or two-pack), and (3) curing reaction (condensation reaction or addition reaction). Each type has its inherent features. In general, for the room-temperature curing type, curing progresses gradually starting from the surface that is in contact with the air (humidity) and moves towards the deeper portions. The curing speed is influenced by the room temperature, humidity (condensation reaction type), the area in contact with the air, the depth of the deeper portion, and so on, so it is hard to manage the curing time, and curing takes a long time. This increases tact time in production. For this reason, the thermal curing type is advantageous in terms of production management because curing progresses evenly and quickly, making time management easier. For the curing reaction type that is based on a condensation reaction, a reaction by-product (gas) is generated in the reaction process, so this type is not suitable for sealed systems. Because of this and from the perspective of the working environment, the addition reaction type is better suited for joining. Note, however, that the addition reaction type uses a platinum catalyst, and if the surface of the member to join contains a component that inhibits the reaction of the platinum catalyst (catalyst poison), it may not be possible to obtain sufficient joint strength due to curing inhibition.
For the silicone adhesion properties of TORELINA™, the silicone adhesives listed in Table. 10.1 were used.
Table. 10.1 Silicone adhesives (commercially available products)
Adhesive | Manufacturer | Product No. | Curing system | Curing conditions |
---|---|---|---|---|
Adhesive (1) |
Dow Corning Toray |
SE 1714 | One-pack, thermal, and addition curing |
150℃ × 0.5 hr |
Adhesive (2) |
SE 1816CV | Two-pack, thermal, and addition curing |
100℃ × 1.0 hr | |
Adhesive (3) |
Shin-Etsu Chemical | KE-1833 | One-pack, thermal, and addition curing |
150℃ × 1.0 hr |
◆Test example 1 - Types of adhesive and adhesion strength -
The results of testing the adhesion properties of the same types of TORELINA™ are listed in Table. 10.2. For all of the silicone adhesives used for this test, no curing inhibition was observed. Depending on the type of the adhesive, differences in the adhesion strength were observed.
Table. 10.2 Silicone adhesion properties of TORELINA™ (adhesion layer thickness: 1 mm, no surface treatment)
TORELINA™ Grade |
Silicone adhesive type | ||||||||
---|---|---|---|---|---|---|---|---|---|
Adhesive (1) | Adhesive (2) | Adhesive (3) | |||||||
Adhesion strength (MPa) |
Cure state | Fracture state | Adhesion strength (MPa) |
Cure state | Fracture state | Adhesion strength (MPa) |
Cure state | Fracture state | |
A504X90 | 1.9 | Cured | Cohesion | 1.0 | Cured | Cohesion | 2.9 | Cured | Cohesion |
A575W20 | 2.3 | Cured | Cohesion | 1.0 | Cured | Cohesion | 2.9 | Cured | Cohesion |
◆Test example 2 - Thickness dependence of adhesive layer -
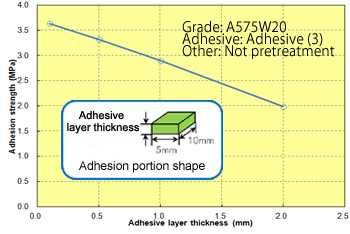
Thickness of adhesive layer in relation to the adhesion strength
For adhesive joining, the adhesion strength may differ depending on the thickness of the adhesive layer, as shown in Fig. 10.3 and Table. 10.3. The following tendency is observed: The thinner the adhesive layer, the higher the adhesion strength.
Table. 10.3 Thickness dependence of the adhesive layer
Item | Adhesive layer thickness(mm) | ||||
---|---|---|---|---|---|
0.1 | 0.5 | 1.0 | 2.0 | ||
Adhesion strength | MPa | 3.6 | 3.3 | 2.9 | 2.0 |
Cure state | Cured | Cured | Cured | Cured | |
Fracture mode | Cohesion | Cohesion | Cohesion | Cohesion |
◆Test example 3 - Durability of silicone adhesion pieces -
Fig. 10.4 Durability of adhesive joining (A575W20)
The results of conducting durability tests on test pieces of TORELINA™ A575W20, to which silicone adhesive (3) was applied (adhesion layer thickness: 1 mm, no surface treatment), are shown in Fig. 10.4 and Table. 10.4. For dry-heat treatment and moist-heat treatment, it can be observed that, by applying such types of treatment, the strength tends to become higher than the initial strength. Judging from the fact that the fracture mode changes from cohesion fracture to alternating fracture, it is assumed that the cured state of the adhesive portion changes with time and thus influences the fracture mode.
Treatment for ensuring durability |
Treatment time (hr) or treatment cycle | |||
---|---|---|---|---|
0 | 48 | 500 | 1000 | |
120℃ dry-heat | Cohesion fracture | Alternating fracture | Alternating fracture | Alternating fracture |
85℃×85%RH | Cohesion fracture |
Alternating fracture |
Alternating fracture |
Alternating fracture |
Cold cycle (-40⇔130℃、1hr each) |
Cohesion fracture |
Interface fracture |
Interface fracture |
Interface fracture |
For cold-cycle treatment, on the other hand, it is observed that the strength tends to fall below the initial strength, causing the fracture mode to change to an interface fracture. It is assumed that, for cold-cycle treatment, high and low temperatures are applied repeatedly, so that strain due to a linear expansion difference occurs at the interface between the molded product and the adhesive. Because of this, the joint strength of the interface decreases with time.
Ⅳ. Epoxy adhesion
Epoxy adhesion is used for not only joining but also encapsulating (potting) electrical circuits in box-shaped molded products for purposes of insulation. Recently, PPS resin has been used for the power module parts of hybrid cars and electric bicycles, among others, increasing the number of cases in which the ability to attain adhesion with epoxy resin is demanded.
Epoxy adhesive (epoxy resin) can be divided into several classifications, much like silicone adhesive. Its features include the fact that it can be cured with a variety of curing agents, such as amine, polyamide, imidazole, polymercaptan, and acid anhydride, and that it exhibits desirable properties such as heat and impact resistance, depending on the type of curing agent.
To determine the epoxy adhesion properties of TORELINA™, the epoxy adhesives listed in Table. 10.5 were used.
Table. 10.5 Epoxy adhesives (commercially available products)
Adhesive | Manufacturer | Base compound |
Curing agent |
Base compound/curing agent blend ratio |
Curing conditions |
---|---|---|---|---|---|
Adhesive (4) | SANYU REC | EC-260 | H-560 | 100 / 90 | 130℃×3hr |
Adhesive (5) | Nagase ChemteX |
XNR5002 | XNH5002 | 100 / 90 | 130℃×3hr |
PPS resin and epoxy adhesive have a relatively high affinity for each other, but the adhesion strength is not sufficient to encapsulate the car parts mentioned earlier. The TORELINA™ lineup includes A610EA1, for which the physical joining force has been increased (surface area increase and anchor effect) without the need for pretreatment such as blasting, as shown in Fig. 10.5, and A490MA50 and A495MA2, which both offer a higher chemical joining force by increasing the number of points at which reactions between the molded product surface and the epoxy adhesive occur, as shown in Fig. 10.6.
Fig. 10.5 Means for improving physical joining force
Fig. 10.6 Means for improving chemical joining force
◆Test example 1 - TORELINA™ grades with good epoxy adhesion -
The epoxy adhesion properties of TORELINA™ are listed in Table. 10.6. Those grades with good epoxy adhesion can produce a joint with a strength about two to three times greater than that possible with general high-filler grades. Only A610EA1 is of a mode in which fracture occurs on the surface layer of the PPS molded product (base material fracture). This is assumed to result from the difference in the mechanism of epoxy adhesion (Figs. 10.5 and 10.6).
Table. 10.6 Epoxy adhesion properties of TORELINA™ (adhesive (5), no pretreatment)
Item | General high filler | Good epoxy adhesion | Good epoxy adhesion and heat cycle resistance |
||
---|---|---|---|---|---|
A310MX04 | A610EA1 | A490MA50 | A495MA2B | ||
Density | (kg/m3) | 1970 | 1900 | 1820 | 1710 |
Adhesion strength |
(MPa) | 3.0 | 8.0 | 9.1 | 10.0 |
Fracture state | Interface | Base material | Interface | Interface |
◆Test example 2 - Types of adhesive and adhesion strength -
The results of testing the adhesion properties of the same types of TORELINA™ are listed in Table. 10.7. For TORELINA™ A490MA50 and A495MA2, no difference is observed with the different adhesive types used in the test, and a high adhesion strength was obtained with both.
Table. 10.7 Epoxy adhesion properties of TORELINA™ (no pretreatment)
TORELINA™ Grade |
Epoxy adhesive type | |||
---|---|---|---|---|
Adhesive (4) | Adhesive (5) | |||
Adhesion strength (MPa) |
Fracture state | Adhesion strength (MPa) |
Fracture state | |
A490MA50 | 9.5 | Base material/Interface | 9.1 | Interface |
A495MA2B | 10.9 | Interface | 10.0 | Interface |
White paper
Toray resin technology increases the reliability of electronic device componentsDramatically Improved Bonding Is Achieved Between the PPS Resin and the Sealing Material
Electronic device parts require the use of epoxy resins and silicone resins as sealants for conductor materials. Sufficient bonding between the high-performance thermoplastic resin used for manufacturing the exterior of an electronic component and the resin used for sealing it is extremely important in ensuring the reliability of the component.